新穎底部填膠材料對覆晶封裝可靠度之研究
全文
(2) 新穎底部填膠材料對覆晶封裝可靠度之研究 Reliability studies of novel underfill materials for flip-chip packaging. 研 究 生:徐元辰. Student:Yuan-Chen Hsu. 指導教授:呂志鵬 教授. Advisor:Dr. Jihperng (Jim) Leu. 國立交通大學 材料科學與工程學系 碩士論文. A Thesis Submitted to Department of Materials Science and Engineering College of Engineering National Chiao Tung University in Partial Fulfillment of the Requirements for the Degree of Master in Materials Science and Engineering July 2006 Hsinchu, Taiwan, Republic of China. 中 華 民 國 九 十 五 年 七 月 i.
(3) 新穎底部填膠材料對覆晶封裝可靠度之研究. 研究生:徐元辰. 指導教授:呂志鵬 博士. 國立交通大學 材料科學與工程學系碩士班. 摘. 要. 關鍵詞:覆晶封裝、底部填膠、可靠度、熱機械性質、界面強度、有限元素法. 針 對 兩 種 bisphenol 樹 脂 基 材 之 底 部 填 膠 分 析 其 重 要 的 熱 機 械 性 質 (thermo-mechanical properties);利用熱機械分析(TMA)、示差掃描熱量計(DSC)、 奈米壓痕儀(NI)、四點彎矩(4PT Bending)和雙懸臂樑(DCB)試驗量測底部填膠的熱 膨脹係數(CTE)、玻璃轉換溫度(Tg)、彈性模數(E)、硬度(H)、彎曲彈性模數(Ef)和 界面強度(Gc)。 所量測底部填膠性質將利用ANSYS二維(2-D)有限元素法(FEM)模擬覆晶封裝 體中銲錫球(solder)和內連層(ILD)的熱應力分布情形,並根據模擬結果預測覆晶封 裝的可能失效部位及底部填膠影響可靠度的關鍵性質。 結果可發現模擬結果與熱循環試驗(TCT)結果有很好的相關性。對高鉛銲錫凸 塊(high lead solder)而言,選擇低熱膨脹係數(CTE)和高彎曲彈性模數(Ef)之底部填 膠可以有效提高其可靠度。 本研究並說明薄膜材料的界面強度量測方法,利用四點彎矩、雙懸臂樑試驗 量測晶片內連層的薄膜之界面強度和底部填膠與晶片之間的界面強度。. ii.
(4) Reliability studies of novel underfill materials for flip-chip packaging. Student: Yuan-Chen Hsu. Advisor: Dr. Jihperng (Jim) Leu. Department of Materials Science and Engineering National Chiao Tung University. ABSTRACT Key words:flip-chip, underfill, reliability, thermo-mechanical properties, Adhesion, FEM simulation, temperature cycling test. The thermo-mechanical properties of two bisphenol resin-based underfill materials including coefficient of thermal expansion (CTE), glass transition temperature (Tg), hardness (H), Young’s modulus (E), flexure modulus (Ef) and adhesion (Gc) were measured and validated against vendor’s data by differential scanning calorimetry (DSC), thermomechanical analyzer (TMA), nanoindentation (NI), four-point bend (4PT Bending) and double cantilever beam (DCB), respectively. Underfill properties data were then used as the input for calculating the stresses at the bump and Cu-low-k structure two-dimensional finite-elements-method (FEM) simulation by ANSYSTM in order to predict the loci of potential failure and identify critical properties of underfill. Excellent correlation was established between the temperature cycling test (TCT). iii.
(5) and stress simulation results. The results show that for high lead solder, underfill with low CTE and high modulus is preferred. Finally, the methodologies for characterizing thin-film adhesion such as four-point bending(4PT) and double cantilever beam(DCB) for measuring the fracture energy of interconnect and underfill/passivation interface were reported in this study.. iv.
(6) 誌. 謝. 經過了兩年的時光,碩士研究的生涯即將結束,在這兩年裡,從 一開始的建立實驗室,到後來的研究內容,經過了許多人的幫忙與指 導,才能順利度過了碩士生涯。 首先要感謝我的家人給予我的支持,有著二十幾年來家人對於我 經濟上和心靈上的支持,我才能夠順利完成碩士的學業。 在研究上要特別感謝呂志鵬老師在這兩年裡的教誨與指導,剛進 入交大碩士班的時候,對於學術研究、處理事務、待人接物等地方總 有其不足之處,也不免犯下不少過錯,感謝老師的容忍與細心指教, 不敢說現在已經到最好,但相信這兩年裡經過老師的指導,在各方面 都有相當的進步。 除了對於老師的感謝,這兩年裡也很感謝許多同學、學長和學弟 的幫忙,子豪和牧龍兩年來的相互扶持,國原學長和昱涵學長的建議 與幫忙,冠與學弟和季高學弟在實驗上也給予相當的助力,Gary 學長 在實驗上給予非常大的幫忙,還有許多曾經給予建議或幫助的同學 們,在這裡對你們表達我最大的感謝之意。 對於本研究,也要特別感謝聯華電子(UMC)透過 SRC 研究計畫. v.
(7) SRC-2005-KJ-1301 對於研究經費上的支持。與聯華電子(UMC)和矽品 (SPIL)共同合作利用 ANSYSTM 軟體模擬分析,並感謝聯華電子林鉅 富、陳韋志、陳國明和矽品王渝博、江東昇博士等人對於研究和實驗 材料上的建議與幫助。. vi.
(8) 目 錄 摘. 要 ..............................................................................................................................ii. ABSTRACT.....................................................................................................................iii 謝 .............................................................................................................................. v. 誌. 目 錄 ..............................................................................................................................vii 表目錄 ............................................................................................................................. ix 圖目錄 .............................................................................................................................. x 第一章. 前言 .................................................................................................................. 1. 1.1 電子封裝簡介 ....................................................................................................... 1 1.2 覆晶封裝製程簡介 ............................................................................................... 4 1.2.1 覆晶凸塊製作 ................................................................................................ 5 1.2.2 晶片接合 ........................................................................................................ 6 1.2.3 底部填膠 ........................................................................................................ 6 1.3 文獻回顧 ............................................................................................................... 8 1.4 研究動機 ............................................................................................................... 9 第二章 2.1 2.2 2.3 2.4 2.5 2.6. 底部填膠材性質量測 .................................................................................... 13. 前言 ..................................................................................................................... 13 底部填膠材料選擇 ............................................................................................. 13 底部填膠材料硬烤程序 ..................................................................................... 15 熱性質分析 ......................................................................................................... 17 機械性質分析 ..................................................................................................... 20 底部填膠材料性質總結 ..................................................................................... 27. 第三章. 應力模擬分析 ................................................................................................ 28. 3.1 前言 ..................................................................................................................... 28 3.2 有限元素分析法簡介 .......................................................................................... 28 3.3 線彈性材料之應力與應變關係式 ..................................................................... 29 3.4 模型建構 ............................................................................................................. 34 3.5 基本假設 ............................................................................................................. 36 3.6 有限元素模擬結果與討論 ................................................................................. 36 vii.
(9) 第四章. 界面破壞機制與測量 .................................................................................... 40. 4.1 前言 ..................................................................................................................... 40 4.2 線彈性破裂機制 ................................................................................................. 40 4.3 能量釋放率 ......................................................................................................... 42 4.4 混合模式破裂 ..................................................................................................... 45 4.5 巨觀界面破裂強度 ............................................................................................. 46 4.6 界面強度量測 ...................................................................................................... 48 4.6.1 四點彎矩試驗 ............................................................................................... 49 4.6.2 雙懸臂樑試驗 ............................................................................................... 54 第五章. 結論與未來建議 ............................................................................................ 70. 參考文獻 ........................................................................................................................ 73. viii.
(10) 表目錄 表 2.1 表 2.2 表 3.1 表 4.1 表 4.2. 廠商提供底部填膠材料性質及熱循環測試結果 ............................................ 15 底部填膠材料性質整理 .................................................................................... 27 底部填膠關鍵性質與應力分析結果 ................................................................ 39 內連層薄膜界面強度 ........................................................................................ 54 底部填膠材料化學組成成分 ............................................................................ 69. ix.
(11) 圖目錄 圖 1.1 電子封裝主要功能 ............................................................................................... 3 圖 1.2 電子封裝之層次 ................................................................................................... 3 圖 1.3 IBM C4(Controlled-Collapse Chip Connection)示意圖....................................... 4 圖 1.4 電鍍銲錫製作程序 ............................................................................................... 5 圖 1.5 凸塊對位及迴銲黏著 ........................................................................................... 6 圖 1.6 覆晶接合自我對正能力 ....................................................................................... 6 圖 1.7 底部填膠製程 ....................................................................................................... 7 圖 1.8 熱應力造成變形 ................................................................................................... 7 圖 1.9 兩種典型錫球失效 ............................................................................................ 11 圖 1.10 底部填膠與晶片保護層界面破裂 .................................................................. 12 圖 1.11 最上層 ILD/阻障層界面發生失效 (a)crack stop (b)blown fuse..................... 12 圖 2.1 EHS2-FCBGA 結構圖 ........................................................................................ 14 圖 2.2 示差掃瞄熱量計結構圖 ..................................................................................... 16 圖 2.3 底膠材料交聯反應(DSC)圖(a)underfill B(b)underfill C .................................. 17 圖 2.4 底膠材料硬烤熱反應(DSC)圖(a)underfill B(b)underfill C ............................... 17 圖 2.5 熱機械分析機 .................................................................................................... 19 圖 2.6 固化底部填膠材料熱機械分析圖 .................................................................... 19 圖 2.7 固化底部填膠材料示差掃描熱量分析圖 ........................................................ 20 圖 2.8 奈米壓痕儀簡圖 ................................................................................................. 21 圖 2.9 壓痕實驗負載-位移曲線圖 ................................................................................ 21 圖 2.9 奈米壓痕儀量測底膠彈性模數 (a)Underfill B (b)Underfill C........................ 24 圖 2.10 奈米壓痕儀測量底膠硬度(a)Underfill B (b)Underfill C................................ 24 圖 2.11 四點彎矩試驗示意圖....................................................................................... 26 圖 3.1 FCBGA 二分之ㄧ對稱模型 ............................................................................... 35 圖 3.2 銅/低介電層、FSG 結構和凸塊結構次模型 ................................................... 35 圖 3.3 FEM 模擬應力分布圖 (a)Underfill B (b)Underfill C ....................................... 38 圖 3.4 使用底部填膠 C,熱循環測試錫球失效圖...................................................... 38 圖 4.1 線彈性材料裂縫式意圖,x1、x2 座標軸平面垂直於裂縫前緣 ..................... 42 圖 4.2 線彈性材料裂縫在拉伸作用力下成長 ............................................................ 43 圖 4.3 負載-位移曲線圖,裂縫成長趨從性變大 ....................................................... 44 圖 4.4 三種破裂模式圖示 ............................................................................................ 46 圖 4.5 巨觀量測材料界面強度 .................................................................................... 47 圖 4.6 界面強度隨著破裂模式不同而改變 ................................................................ 47 圖 4.7 毫微米機械量測系統 ........................................................................................ 49 圖 4.8 四點彎矩試驗層狀結構試片 ............................................................................ 50 x.
(12) 圖 4.9 四點彎矩試片製作流程 .................................................................................... 51 圖 4.10 試片以 C 型夾固定.......................................................................................... 51 圖 4.11 四點彎矩試片結果圖....................................................................................... 52 圖 4.12 四點彎矩試驗負載位移曲線圖 ...................................................................... 52 圖 4.13 理想雙懸臂樑試驗 .......................................................................................... 55 圖 4.14 Si/Underfill/Si DCB 試片.................................................................................. 56 圖 4.15 雙懸臂樑試片變形量疊加示意圖 .................................................................. 57 圖 4.16 部分懸樑臂受到黏著層支持 .......................................................................... 59 圖 4.17 轉換斷面法計算截面轉動慣量 ...................................................................... 62 圖 4.18 DCB 試片製作流程圖 ...................................................................................... 65 圖 4.19 底部填膠厚度 .................................................................................................. 66 圖 4.20 底部填膠 B/SiN DCB 試片破裂面 ................................................................. 67 圖 4.21 DCB 試驗底部填膠材料 B 荷重-位移圖 ........................................................ 67 圖 4.22 DCB 試片屈從性分析其破裂長度 .................................................................. 68. xi.
(13) 第一章 前言 1.1 電子封裝簡介 隨著科技文明的進步與發展,微電子產品成為日常生活中所不可 獲缺的一部分。微電子產品製成程大略可分為晶圓(wafer)成長、電路 設計、晶片製造與封裝(Package);其中電子封裝技術為後段製程的關 鍵技術之ㄧ。電子封裝主要有以下四功能,如圖 1.1 所示[1]: 一、電源傳輸 二、訊號傳輸 三、提供散熱 四、晶片保護與支持 電子封裝製程技術可以幾個不同層級區分,如圖 1.2 所示[2]。第 一層級封裝為將積體電路(IC)晶片黏結於一封裝體上並完成其電路連 結及保護之製程;第二層級封裝為將第一層級完成的元件黏著到電路 板(PCB)上;第三層級指將數個電路板組合於一主機板上成為一次系 統。但隨著製程技術的進步,如晶片直接組裝(COB)可省略第一 層級組裝,技術層次的分野也逐漸模糊。 如今電子產品朝向輕、薄、短、小及高密度多功能的趨勢發展, 電子封裝技術也隨著不斷演進;從傳統通孔插裝(PTH)型態的單列式封. 1.
(14) 裝(SIP)及雙列式封裝(DIP),經歷表面黏著技術(SMT)所衍生出的四方 扁平封裝(QFP)和小型化封裝(SOP),至覆晶技術的球腳陣列矩陣 (BGA)及小體積的晶片級封裝(CSP)和覆晶封裝(Flip-Chip)。 而晶片與電路板的連結,主要可分為捲帶式接合(TAB)、打線接合 (wire bonding)及覆晶接合(flip-chip)三種技術。其中覆晶接合技術相較 其他技術有以下的優點: 一、 以面積矩陣做排列(Area Array),可提供較高的 I/O 數 二、 透過錫球(solder bump)直接與基板連接,可縮小晶片所佔面積 三、 合有引線短、低電容、低電感及雜訊容易控制等優良電性 四、 提供較大的散熱面積,有較好的散熱能力 五、 覆晶接合可同時完成所有 I/O 接點,有快速的接合能力 在朝向高功率,小體積化的趨勢下,覆晶封裝有較其他技術無可 取代的優勢,CSP、FCBGA、FlipChip 等封裝體在封裝產業中產能與 佔有率逐漸增加[3],覆晶封裝技術將成為未來封裝業的主流技術。 然而隨著電子元件體積不斷縮小,加上未來無鉛銲錫(lead free solder) 和低介電(dielectric)材料的使用,覆晶封裝的可靠度(reliability)將成為 重要的議題,本文將針對覆晶封裝技術中錫球和內連層的可靠度議題 進行研究。. 2.
(15) 圖 1.1 電子封裝主要功能. 圖 1.2 電子封裝之層次 3.
(16) 1.2 覆晶封裝製程簡介 IBM 在 1964 年時發表的 C4 (Controlled-Collapse Chip Connection) 技術為最早的覆晶封裝技術,如圖 1.3 所示[2],覆晶封狀技術是將凸 塊(solder bumping)成長在晶片 I/O 接墊(metal pad)上,將晶片反轉在銲 錫經過迴銲(reflow)之後使其與基板連結。其製程主要可分為凸塊製 作、晶片接合與底部填膠(underfill)三部份。. 圖 1.3 IBM C4(Controlled-Collapse Chip Connection)示意圖. 4.
(17) 1.2.1 覆晶凸塊製作 覆晶凸塊的種類很多,包括錫鉛共晶銲錫、高鉛銲錫及未來的無 鉛銲錫等,其合金成分取決於基板材料種類與後續組裝製程的條件。 其製作方法為先以蒸鍍、濺鍍等方法在金屬接墊上生成 UBM (Under Bump Metallurgy)層,UBM 由三層金屬層所構成,包括黏著層(Adhesion Layer)、擴散阻障層(Diffusion Barrier Layer)與潤濕層(Wetting Layer); 黏著層的功能在於加強凸塊與金屬墊及晶片保護層(Passiviation Layer) 之間的附著力(adhesion),一般以 Ti、Cr 等金屬材料為主;擴散阻障層 能阻止凸塊與接墊反應生成介金屬化合物(Intermetallic Compound),其 材料以 Cu、Ni 為主;潤濕層的功用則是提升凸塊與黏著層的黏性, 這一層是以 Au、Ag 等金屬材料為主。接著再以蒸鍍、電鍍或印刷法 在 UBM 上生成凸塊並經過迴銲成球狀,圖 1.4 為以電鍍法製作錫鉛凸 塊程序[4]。. 圖 1.4 電鍍銲錫製作程序 5.
(18) 1.2.2 晶片接合 凸塊製作完成後,在其上沾助銲劑(Flux),再將凸塊對準基板上 的銲墊,經過回銲完成基版與晶片的連接如圖 1.5 所示。在迴銲連接 的過程中凸塊有很好的自我對正(self alignment)能力,如圖 1.6 所 示[5]。. 圖 1.5 凸塊對位及迴銲黏著. 圖 1.6 覆晶接合自我對正能力. 1.2.3 底部填膠 底部填膠(underfill)為覆晶封裝中相當重要的關鍵技術。先將基板 預熱至 60~90℃以提高底膠的流動性,接著將底部填膠點在基板邊緣, 利用毛細作用(capillarity)填滿(dispensing)晶片與基版之間的空隙,再經. 6.
(19) 過約 150℃硬烤(curing)使膠材固化,如圖 1.7 所示。底部填膠的主要功 能是分散製程中熱漲冷縮作用下所引起的熱應力,如圖 1.8 所示。一般 底部填膠的成分包含環氧樹脂(epoxy resin)、硬化劑(hardener)、催化劑 (catalyst)、填充物(filler)及其他的添加物(additives)。其中催化劑會影響 膠材交聯(crosslink)反應的溫度及膠材的黏滯性(viscosity)[6];而填充物 的 作 用 在 於 降 低 膠 材 的 熱 膨 脹 係 數 CTE (Coefficient of Thermal Expansion)以減少因 CTE 差異造成的熱應力,並增加底膠的彈性模數 E (Young’s Modulus);但同時也會增加膠材的黏滯性(viscosity)減低其流 動性[7]。. 圖 1.7 底部填膠製程. 圖 1.8 熱應力造成變形. 7.
(20) 1.3 文獻回顧 電子封裝可靠度議題日益受到重視,Norris 和 Landzberg 於 1969 年時使用 Coffin-Manson equation 預測覆晶封裝在不同溫度循環下高鉛 錫球的可靠度,錫球的典型失效如圖 1.9 所示[8]。Chen 和 Nelson 首先 於 1979 年時對於不同熱膨脹係數與彈性模數材料之間的黏著層 (adhesive)進行熱應力的分析研究,並應用於說明電子封裝體中,主要 的熱應力作用於黏著層的邊緣[9]。Darveaux 和 Banerji 在 1991 年時對 於覆晶封裝體在不同的溫度及時間循環下分析高鉛錫球所受熱應力與 可靠度關係,結果可知錫球在溫度循環過程中承受較大的應力會有較 差的可靠度[10]。Popelar 研究覆晶封裝體中晶片和錫球大小對於覆晶 封裝可靠度的影響,說明錫球和體積愈小時會縮短其可靠度,而使用 底部填膠可平均分散錫球所受熱應力並提升其可靠度[11]。Lau 和 Pau 對於各種錫球的失效模式(failure mode)、淺變(creep)模型及可靠度問題 做了一系列的整理[12]。 除了凸塊的失效外,Lau 等人利用模擬分析不同性質底部填膠與保 護層(passivation)和阻銲膜(solder mask)之間破裂(如圖 1.10 所示)時的影 響,底部填膠的熱膨脹係數愈小時能有較好的界面強度 [13]。Zhang 等人則利用雲紋干涉法(moiré interferometry)分析在溫度循環下不同溫 度時底部填膠與保護層之間的界面應力強度因子(stress intensity factor). 8.
(21) 及不同方向應力作用比率(mode-mixity),說明介面較易發生破裂在溫度 最高和最低的狀態下[14]。 隨著電子元件不斷縮小,為了降低金屬連線的電阻-電容延遲時間 (Resistance Capacitance Time Delay,RC delay),低介電材料(Low-k Dielectrics)的應用日益重要,而低介電材料較差的機械性質容易導致封 裝時晶片內連層(Interconnect)的失效。Mercado 等人對 PBGA(Plastic Ball Grid Array)晶片中的銅導線/低介電材料(Cu/low-k)內連層以有限元 素法分析其在封裝下的熱應力分佈,結果發現最大應力將集中晶片的 角落,且在內連層的多層結構(multi-layer)中最大應力集中在靠近晶片 最上層低介電內連線(interlayer dielectric,ILD)界面,內連層的失效如 圖 1.11 所示[15]。Tsao 等人則對使用不同底部填膠的 FCBGA(Flip-Chip Ball Grid Array)封裝體,分析其晶片角落所受熱應力,發現較高彈性模 數的底部填膠容易引起內連層的失效[16]。 在針對底部填膠性質探討部分,Lau 和 Chang 對不同的底部填膠 分析其材料性質,包括熱膨脹係數、玻璃轉換溫度、彈性模數、彎曲 模數(flexure modulus)、黏著強度、吸水性及流動性等性質[17]。. 1.4 研究動機 隨著覆晶封裝的重要性逐漸增加,其可靠度(reliability)議題也變的. 9.
(22) 更加重要,電子封裝元件是由複雜的結構與不同性質的材料所組成, 在溫度變化時,因為各材料間的材料性質差異(矽晶片的 CTE 約為 2~3 ppm/℃而塑膠基板的 CTE 約為 17~20 ppm/℃)造成很大的熱應力及熱 應變而引起元件不同形式的失效,尤其在使用更高熔點的無鉛銲錫 (lead free)和機械性值更差的低介電(low-k)材料,如何減少熱應力的影 響增加其可靠度將成為關鍵。典型的失效可能出現在錫球、底部填膠 與晶片保護層界面或者晶片的內連層(Interconnect),如圖 1.9-1.11 所 示,利用底部填膠來分散熱應力以提升其可靠度為一有效的解決方法。 在探討覆晶封裝可靠度議題,材料之間的界面強度(adhesion)為一 項重要的關鍵性質,包括底部填膠與晶片和錫球之界面、內連層各層 材料間之界面強度,為影響其可靠度的重要關鍵。故如何量測薄膜之 間的界面強度成為重要的問題,本研究建立了材料薄膜的界面強度量 測儀器及方法,將探討多層結構內連層內材料之間的界面強度,以及 覆晶封裝中底部填膠與晶片保護層(passivation)之間的界面強度。 分析覆晶封裝體在溫度變化時產生的熱應力,為有效判斷其可靠 度及預測可能失效位置的方法,而以實驗方式分析熱應力分佈及其可 靠度有其限制之處及需花費大量時間,利用電腦模擬分析可節省大量 時間及成本。本研究利用有限元素法(Finite Element Method,FEM)分 析軟體 ANSYSTM,分析使用不同性質底部填膠對於 FCBGA 封裝體中. 10.
(23) 錫球和內連層在溫度變化產生的熱應力分布情形,並比對其溫度循環 試驗(Thermal Cycling Test,TCT)的結果,建立覆晶封裝的可靠度預測 機制及預測其可能發生失效位置,並找出底部填膠關鍵性質對於可靠 度的影響。 利用電腦模擬分析,正確的材料性質資料是影響模擬結果精準度 的重要條件,底部填膠材料為一熱固性(thermosetting)環氧樹脂(epoxy) 混合材料,其材料性質會因為不同的硬烤溫度及時間,而有其誤差存 在,故本研究針對底部填膠的重要熱性質及機械性質進行量測驗證, 以提高電腦模擬分析的精準度。. 圖 1.9 兩種典型錫球失效. 11.
(24) 圖 1.10 底部填膠與晶片保護層界面破裂. 圖 1.11 最上層 ILD/阻障層界面發生失效 (a)crack stop (b)blown fuse. 12.
(25) 第二章. 底部填膠材性質量測. 2.1 前言 正確的底部填膠性質對於模擬分析結果精確性有很大的影響。本 章將介紹量測底部填膠材料重要熱性質及機械性質所使用的實驗方法 及原理,及針對所使用的底部填膠材料量測其性質。. 2.2 底部填膠材料選擇 表 2.1 為由兩家不同廠商所提供的三種不同底部填膠材料性質及 溫度循環測試(Thermal Cycling Test,TCT)結果比較。其中溫度循環測 試是利用 EHS2-FCBGA 封裝體(如圖 2.1 所示)在 125℃到-55℃溫度範 圍經過 1000 次循環。其結構由 16mm x 16mm 低介電材料晶片(Cu/low-k die)和 40mm x 40mm 的塑膠基材由 100μm 高度的錫球和底部填膠組 成,其錫球結構為共晶錫鉛銲錫(eutectic solder)預先焊接(pre-solder), 然後主要銲錫為高鉛銲錫(high lead solder)。從表中可知底部填膠材料 A 有較低的玻璃轉換溫度(Glass Transition Temperature,Tg)及較高的熱 膨脹係數(Coefficient of Thermal Expansion,CTE)造成最差的可靠度測 試結果,而底膠材料 B 和 C 的組成同為 Bisphenol 環氧樹脂的化學結 構有較接近的材料性質,但只有在使用底部填膠材料 B 的情形下封裝 體可通過 TCT 測試而在使用底部填膠材料 C 時會發生銲錫球的失效。 13.
(26) 故本文選擇針對底膠材料 B 和 C 做熱應力分析來探討其與可靠度的關 聯並找出底膠材料的關鍵性質。而因為底膠材料 B 和 C 來自不同的製 造商,其量測材料性質會因為不同的底膠硬烤(curing)溫度、時間,不 同的量測樣品大小、形狀及缺陷,或因為在不同的測試環境條件下使 用不同的儀器而出現一定的誤差因素。為了減少模擬分析結果的誤差 值,本文所使用底部填膠材料將以實際封裝測試中所使用的相同溫度 及時間進行硬烤(curing),並且在相同的實驗條件及環境下重新驗證底 部 填 膠 材 料 之 各 項 重 要 熱 性 質 及 機 械 性 質 (thermal-mechanical properties),驗證過的底部填膠材料性質將利用電腦模擬熱應力分析來 找出其影響覆晶封裝可靠度的關鍵性質。. 圖 2.1 EHS2-FCBGA 結構圖. 14.
(27) 表 2.1 廠商提供底部填膠材料性質及熱循環測試結果 Vender. Supplier#1. Supplier#2. Units Type. A. B. C. Tg (TMA). ℃. 55. 80. 70. CTE1 (TMA). ppm/℃. 35. 32. 32. CTE2(TMA). ppm/℃. 115. 102. 110. GPa. 7.3. 8. 7. Fail worst. Pass. Modulus (below Tg) (3 pt bend) Packaging reliability. Bump crack. test (TCT). 2.3 底部填膠材料硬烤程序(curing profile) 底部填膠材料為環氧樹脂(epoxy)基材的熱固性(thermosetting)混合 材 料 , 利 用 合 適 的 硬 烤 程 序 (curing profile) 可 使 其 發 生 完 全 交 聯 (crosslinking)固化且盡量減少其硬烤時產生的殘留熱應力。示差掃描熱 量計(Differential Scanning Calorimetry,DSC)可用來找出底部填膠的合 適硬烤程序。本研究利用 Perkin PYRIS Diamond DSC 功 率 補 償 (power-compensation)示差掃描熱量計來分析底部填膠的硬烤反應過 程,示差掃描熱量計(DSC)的基本構成如圖 2.2 所示[18]。功率補償式 原理為將樣品與參考體置於加熱爐中,在樣品與參考體下方以熱電偶 (thermocouple)偵測樣品與參考體間之溫度,當樣品發生吸熱或放熱反 15.
(28) 應時,加熱系統會根據溫度的變化而調節輸入的能量,使樣品與參考 物溫度維持相同,根據加熱器的輸入能量變化量可知樣品的熱焓變化 量,儀器的使用溫度限制可達 600℃,量測能量的精確度為 1μw。 對所選擇的二底部填膠材料,利用示差掃描熱量計(DSC)量測其交 聯反應發生時的放熱量變化,液態底部填膠材料從室溫以每分鐘 10℃ 升溫速率加熱至 300℃,結果如圖 2.3 所示,底膠B和C的劇烈交聯反應 溫度分別為 146℃及 196.5℃。而考量到共晶錫球的熔點為 183℃及其 他熱性質的影響,兩種底部填膠的硬烤溫度選擇從室溫以每分鐘 4℃升 溫速率加熱至 150℃,並保持溫度於 150℃一個半小時,再以爐溫冷卻 回室溫以減少殘留的熱應力。圖 2.4 顯示此硬烤溫度、時間在經過 90 分鐘時已無放熱變化發生,表示二底部填膠材料已完全交聯反應。. 圖 2.2 示差掃瞄熱量計結構圖. 16.
(29) 圖 2.3 底膠材料交聯反應(DSC)圖(a)underfill B(b)underfill C. 圖 2.4 底膠材料硬烤熱反應(DSC)圖(a)underfill B(b)underfill C. 2.4 熱性質分析 底部填膠的重要熱性質包括其玻璃轉換溫度(Tg)及熱膨脹係數 (CTE)。利用熱機械分析,如圖 2.5 所示,在控制的溫度變化下,對樣 品施以微量的壓縮機械作用力,量測樣品在溫度變化時的尺寸變化 量。在微量機械作用力的作用可忽略的情況下,樣品的尺寸改變量即. 17.
(30) 為樣品的熱膨脹變化量,可量測其熱膨脹係數、玻璃轉化溫度和應力 釋放等訊息。 本 研 究 利 用 壓 縮 模 式 熱 機 械 分 析 (thermal-mechanical analyzer) TMA2940 儀器量測,儀器的溫度限制為-150℃~1000℃,靈敏度可達 100nm,試驗樣品厚度為 2mm 厚硬化底部填膠材料,試片從室溫以每 分鐘 5℃加熱速率加熱至 180℃,機械作用力設定為 10 毫克。結果如 圖 2.6 所示,底部填膠材料 B 和 C 的玻璃轉換溫度分別出現在 61.3℃ 和 60.2℃。熱膨脹係數可由樣品尺寸改變量對溫度變化的斜率計算得 知,底部填膠材料 B 和 C 的熱膨脹係數在玻璃轉換溫度以下分別為 29.1ppm/℃和 34.7ppm/℃,而在溫度高於玻璃轉換溫度時,底部填膠分 子間的距離因為溫度的上升而增加,使其分子間的排列變的較為鬆 散,熱膨脹係數因此升高為 101.3ppm/℃和 102.5ppm/℃。 比較實驗所得性質與廠商所提供性質,可發現底膠材料 B 的玻璃 轉換溫度相差了約 19℃,為了確認實驗數值的正確性,利用示差掃描 熱量計重新驗證底部填膠材料的玻璃轉換溫度,熱機械分析可能受到 試片形狀、大小、缺陷或機械力等影響出現實驗誤差,而示差掃描熱 量計則為分析底部填膠材料的化學熱反應,可量測其純材料性質的玻 璃轉換溫度,結果如圖 2.7 所示,示差掃描熱量計以每分鐘 10℃加熱 速率測得底膠材的料玻璃轉換溫度分別為 65.5℃及 64.4℃,且底部填. 18.
(31) 膠材料 B 的熔點出現在 150.9℃,根據其結果,可發現底部填膠 B 在高 溫時會出現熔點反應,表現出結晶行為,其結晶行為導會致其結構堆 疊較為緊密,所以兩種底部填膠有接近的玻璃轉換溫度而底部填膠 B 有較低的熱膨脹係數。. 圖 2.5 熱機械分析機 (Thermomechanical Analyzer). 圖 2.6 固化底部填膠材料熱機械分析圖. 19.
(32) 圖 2.7 固化底部填膠材料示差掃描熱量分析圖. 2.5 機械性質分析 底部填膠的重要機械性質包括彈性模數和硬度,傳統使用拉伸試 驗機或硬度測試機量測塊材 (bulk) 的楊氏模數(Young’s modulus) 和 硬度 (hardness), 但不適合用於量測薄膜材料,因為薄膜材料無法承 受過大的荷重。利用奈米壓痕儀(nanoindentation)可量測薄膜材料的楊 氏模數和硬度,圖 2.8 為其示意圖。奈米壓痕儀利用壓痕荷重對位移的 關係來量測薄膜機械性質,紀錄壓痕負載及卸載時的荷重位移關係 圖,如圖 2.9 所示。. 20.
(33) 圖 2.8 奈米壓痕儀簡圖. 圖 2.9 壓痕實驗負載-位移曲線圖. 21.
(34) 在卸載過程中,根據彈性變形模式,求取最大荷重時的接觸面積, 薄膜之硬度可定義為在負載下材料所支稱的平均壓力[19]:. H=. Pmax A. (2.1). 其中 H:薄膜硬度 Pmax:為最大負載 A :壓痕器接觸面積. 而薄膜之楊氏模數 E 可以下列式子分析:. S=. dP 2 Er A = dh π. (2.2). 1 (1 − υ 2 ) (1 − υ i ) = + Er E Ei 2. (2.3). 其中 S:初始負載剛性(initial stiffness) h:壓痕位移 Er:卸載時的變形模數(reduced modulus) A:彈性接觸時的投影面積. 22.
(35) E、Ei:薄膜、壓痕器的楊氏模數 ν、νi:薄膜、壓痕器的蒲松比(poisson’s ratio). 本研究利用 MTS Nanoindenter XP 奈米壓痕儀量測底部填膠材料 的楊氏模數(E)及硬度(H),其位移解析度為 0.1nm 負載解析度為 <500nm,壓痕深度範圍 25nm 至 500μm,可量測最小薄膜厚度為 1000A。量測試片以 10mm x 10mm 矽晶片為基材量測 200μm 厚度的底 部填膠,利用奈米壓痕儀在不同探針深度時的剛性計算薄膜的變形模 數,可分析在不同探針深度時薄膜的彈性模數與硬度,在探針深度較 淺時,薄膜材料的剛性會受到表面效應的影響(surface effect),而探針 深度較深時,則會受到基材效應的影響(substrate effect),在不受影響 的量測範圍內,可測得薄膜材料的硬度及彈性模數。故探針深度在 6000nm 時所測得的彈性模數與硬度為底部填膠材料 B 和 C 之材料性 質,結果如圖 2.10 及 2.11 所示,由十次量測平均所得,底部填膠材料 B 和 C 之楊氏模數分別為 11.0GPa 與 10.9GPa、而硬度則為 0.42GPa 和 0.29GPa。. 23.
(36) 圖 2.9 奈米壓痕儀量測底膠彈性模數 (a)Underfill B (b)Underfill C. 圖 2.10 奈米壓痕儀測量底膠硬度(a)Underfill B (b)Underfill C 24.
(37) 在分析覆晶封裝體的熱應力分佈時,底部填膠的彎曲彈性模數 (flexure modulus)為ㄧ項重要的性質,四點彎矩試驗,如圖 2.11 所示, 可用來量測樣品的彎曲彈性模數 Ef (flexure modulus)。根據樑柱理論 (Beam theory),樣品在彎曲試驗時所受最大應力 σ 為:. σ=. Mh 2I. (2.4). 其中 M:彎曲力矩(bending moment) I:截面轉動貫量 I (cross section moment inertia) h:樣品厚度. 樣品之彎曲彈性模數 Ef 可由其負載-位移曲線關係計算得知[20]:. 5PL3 Ef = 27 Bh 3 d. (2.5). 其中 P:負載荷重 L:支點間距 B:樣品寬度 d:負載點位移量. 25.
(38) 利用四點彎矩試驗測量底部填膠的彎曲彈性模數,底部填膠的樣 品大小為 66mm x 5.4 mm x 1mm,其荷重與位移曲線圖如圖 2.12 所示, 再以方程式 2.5 可計算其彎曲模數,底部填膠 B 和 C 的彎曲模數分別 為 8.5GPa 和 7.1GPa,與廠商所提供的性質並無太大的差異。. 圖 2.11 四點彎矩試驗示意圖. 圖 2.12 四點彎矩試驗荷重-位移圖 26.
(39) 2.6 底部填膠材料性質總結 兩種同樣 Bisphenol 環氧樹脂基材的底部填膠利用熱機械分析 (TMA)、示差掃描熱量計(DSC)、奈米壓痕儀(NI)、四點彎矩試驗(4PT Bending)量測其重要的熱性質及機械性質,結果如表 2.2 所示,兩種底 部填膠材料有接近的玻璃轉換溫度(Tg)、玻璃轉換溫度以上的熱膨脹係 數(CTE2)、和楊氏模數(E)。而主要差異的性質為玻璃轉換溫度以下的 熱膨係數(CTE1)、彎曲彈性模數(Ef)和硬度(H)。其中兩種膠材硬度都 相當的低,則對於覆晶封裝體的熱應力及可靠度的主要影響將來自於 底部填膠材料的玻璃轉換溫度以下的熱膨係數(CTE1)和彎曲模數(Ef)。. 表 2.2 底部填膠材料性質整理 Underfill B. Underfill C. Tg (TMA). 61.3 ℃. 60.2 ℃. Tg (DSC). 64.4℃. 65.6℃. CTE1 (TMA). 29.1 ppm. 34.7 ppm. CTE2 (TMA). 101.3 ppm. 102.5 ppm. Elastic modulus (NI). 11.0±0.2 GPa. 10.9±0.4 GPa. Flexure (4 pt bend). 8.5 GPa. 7.1 GPa. 0.42±0.01 GPa. 0.29±0.01 GPa. Modulus Hardness (NI). 27.
(40) 第三章 應力模擬分析. 3.1 前言 在針對電子元件可靠度的研究,可以實驗分析之或者以電腦模擬 分析之(Computer Aided Engineering,CAE)。在實驗分析之前,先以電 腦模擬排除ㄧ些實驗時可能發生的問題,可大幅減少實驗所需花費的 時間與成本。 覆晶構裝體中的典型失效包括銲錫球和內連層的失效,故本研究 將針對不同性質的新穎底部填膠對於覆晶封裝中錫球和內連層部位的 熱應力進行模擬分析,本章將簡單介紹有限元素的由來和模擬分析時 所用到的理論,並說明本研究使用 ANSYSTM 模擬軟體時所使用的基本 假設、模型建立,最後將模擬分析結果與可靠度實驗結果比對,找尋 其相聯關係,本研究中模擬結果為由聯電陳國明經理所提供[21]。. 3.2 有限元素分析法簡介[22] 有限元素分析法(Finite Element Method)為由美國加州大學教授 Clough在1960年時首先引用的名稱,在現代工程結構設計中,常常要 處理非常複雜的力學結構問題,如對一座橋樑做應力及變形的分析, 要用數學方式去寫出和求解其工程結構的微分方程式幾乎是不可能. 28.
(41) 的。而有限元素法可將複雜的工程結構,切割成ㄧ個個形狀簡單的小 單位元素,而對每ㄧ個小元素即可寫出其受力變形時的微分方程式。 根據有限元素法,將每個小原素拼接起來,加上原本結構的條件限制, 即可建立複雜工程結構的計算模型。隨著電腦功能不斷提高,有限元 素法可以處理更複雜更大量的結構問題。目前,有限元素法在線性結 構力學、溫度場和熱彈性變形分析、熱傳導、電磁場、流體場的計算 分析等領域已發展的相當成熟,而仍在發展的領域有:彈塑性(非線性 力學)分析、斷裂韌性計算、流體力學、結構體和流體相互作用問題的 分析、以及潛變、熱衝擊和黏彈性力學等。. 3.3 線彈性材料之應力與應變關係式 本文以有限元素模擬軟體 ANSYSTM 模擬覆晶封裝體中銲錫球和 內連層在溫度變化時所受的熱應力及應變。並假設所有材料為線彈性 材料(linear elastic),線彈性材料的應力與應變之關係式將依循虎克定律 以線性關係變化:. {σ} = [E]{εe}. (3.1). {εe} = {ε}−{εth}. (3.2). 其中{σ}:[σx σy σz σxy σyz σxz]T,應力向量. 29.
(42) [E]:彈性矩陣 {εe}:彈性應變向量 {ε}:[εx εy εz εxy εyz εxz]T總應變向量 {εth}:熱應變向量. 將 3.2 式帶入 3.1 式中,可得:. {ε} = {εth} + [E]-1{σ}. [E ]. −1. ⎡ 1 ⎢ Ex ⎢− υ ⎢ yx Ex ⎢ ⎢ − υ zx Ex = ⎢ ⎢ 0 ⎢ ⎢ 0 ⎢ ⎢ ⎢ 0 ⎣. (3.3). − υ xy 1. Ey. Ey. − υ zy. − υ xz − υ yz 1. Ey. Ez Ez. Ez 1. 0. 0. 0. 0. 0. 0. 0. 0. 0. 0. 0. 0. 0. 0. 0. G xy 1. G yz 0. ⎤ 0 ⎥ ⎥ 0 ⎥ ⎥ ⎥ 0 ⎥ ⎥ 0 ⎥ ⎥ 0 ⎥ ⎥ 1 ⎥ G zx ⎦. 上式中Ex為x方向的彈性模數(Elastic modulus),νxy為浦松比(Possion’s ratio),若材料具有等向性,則:. Ex = Ey = Ez = E νxy = νyx = νyz = νzy = νxz = νzx =ν 30.
(43) Gxy =Gyz =Gxz =G = E/2(1+ν ). 三維的熱應變向量可表示為:. {εth} = ΔT[αx αy αz 0 0 0]T. (3.4). 其中αx:x軸方向之熱膨脹係數,若材料為均質等向性則αx = αy = αz ΔT = T − Tref Tref:環境參考溫度 T:分析溫度. 將 3.4 式帶入 3.3 式中,可得:. {ε} = αΔT + [E]-1{σ}. (3.5). 則均質等向性材料中,其應變可展開為:. εx = εy =. εx =. σ x − υ (σ y + σ z ) E. σ y − υ (σ x + σ z ) E. σ x − υ (σ y + σ z ) E. + σΔT. (3.6a). + σΔT. (3.6b). + σΔT. (3.6c). 31.
(44) ε xy = ε yz =. ε xz =. σ xy. (3.6d). G. σ yz. (4.6e). G. σ xz. (4.6f). G. 應力也可展開為:. 1−υ 2 υ +υ 2 σ x = E( )(ε x − αΔT ) + E ( )(ε y + ε z − 2αΔT ) 1 − 3υ 2 − 2υ 3 1 − 3υ 2 − 2υ 3 (3.7a). 1 −υ 2 υ +υ 2 σ y = E( )(ε y − αΔT ) + E ( )(ε x + ε z − 2αΔT ) 1 − 3υ 2 − 2υ 3 1 − 3υ 2 − 2υ 3 (3.7b). 1 −υ 2 υ +υ 2 σ z = E( )(ε z − αΔT ) + E ( )(ε x + ε y − 2αΔT ) 1 − 3υ 2 − 2υ 3 1 − 3υ 2 − 2υ 3 (3.7c). 可計算其主應變 ε0:. ε x − ε0 1 ε xy 2 1 ε xz 2. 1 ε xy 2. ε y − ε0 1 ε yz 2. 1 ε xz 2 1 ε yz = 0 2. ε z − ε0 32.
(45) ε0 = [ε1 ε2 ε3]. (3.8). 最大應變差 εI:. ε I = MAX [ ε1 − ε 2 ε 2 − ε 3 ε 3 − ε1 ]. Von-Mises strain 或等效應變(Equivalent strain). εE =. [. (3.9). εE:. ]. 1 ⎛1 2 2 2 ⎞ − + − + − ( ε ε ) ( ε ε ) ( ε ε ) ⎜ ⎟ 1 2 2 3 3 1 1 + υ∗ ⎝ 2 ⎠. 1 2. (3.10). υ*:等校浦松比(Effective Possion’s ratio). 計算其主應力 σ0:. σx −σ0 σxy σxz σxy σy −σ0 σyz =0 σxz σyz σz −σ0 σ0 = [σ1 σ2 σ3]. (3.11). 最大應力差 σI:. 33.
(46) σ I = MAX [σ 1 − σ 2 σ 2 − σ 3 σ 3 − σ 1 ]. Von-Mises stress 或等效應力(Equivalent strain). [. (3.12). σE:. ]. ⎛1 ⎞ (σ 1 − σ 2 ) 2 + (σ 2 − σ 3 ) 2 + (σ 3 − σ 1 ) 2 ⎟ ⎝2 ⎠. σE = ⎜. 1 2. (3.13). 當 υ* = υ 時:. σ E = Eε E. (3.14). 3.4 模型建構 本文主要探討的模型為 EHS2-FCBGA 封裝體(如圖 2.1 所示),覆 晶封裝為三維立體結構,使用三維有限元素分析可得到較精確的結 果,但三維有限元素模擬需耗費相當長的時間,Zhao 等人曾分析以二 維有限元素模擬結果與三維模擬結果有相同的趨勢且其結果仍在誤差 可接受範圍內本[23]。故本文利用二維有限元素模型進行分析,主要模 型如圖 3.1 所示。其結構包含晶片(die)、基材(substrate)、散熱片(heat spreader)和銅固定環(Cu stiffener),而次模型如圖 3.2 所示,包含銅/低 介電材料、FSG 內連層結構和凸塊結構,凸塊的組成包含共晶銲錫 (pre-solder)和高鉛銲錫,將針對銲錫球和內連層進行熱應力模擬分析。 34.
(47) 而表 2.2 所量測得不同的底部填膠材料性質將做為模擬分析時的主要 變因。. 圖 3.1 FCBGA 二分之ㄧ對稱模型. High lead solder. Eutectic solder. 圖 3.2 銅/低介電層、FSG 結構和凸塊結構次模型. 35.
(48) 3.5 基本假設 本研究將針對覆晶構裝在溫度變化時,不同性質的底部填膠對於 錫球和內連層所受熱應力的影響。對於ANSYSTM有限元素模擬軟體給 予下列假設:. 1. 所有材料為均質、等向性、線彈性材料。 2. 封裝體內各材料界面假設有完美的附著力。 3. 二維模型在z方向沒有深度的限制。 4. 對二分之ㄧ的封裝體模型進行模擬。 5. 中線(Neutral Line)為不動邊界。 6. 將參考溫度設為125℃,即125℃時為不受應力影響的狀態。 7. 分析溫度從125℃冷卻至-55℃。. 3.6 有限元素模擬結果與討論 在經過溫度變化後,錫球和內連層的等效熱應力分部如圖 3.3 所 示,最大的應力出現在靠近 UBM 層的錫球邊緣和晶片的角落,其結果 對照於熱循環測試結果,如圖 3.4 所示,錫球的失效位置吻合於模擬最 大應力集中位置,而最大的等效應力値如表 3.1 所示,使用底部填膠材 料 B 和 C 時在銲錫球邊緣的最大等效應力分別為 159.0MPa 和. 36.
(49) 176.2MPa,使用底部填膠 C 時在銲錫球邊緣會產生較大的應力,導致 錫球的失效,其結果和熱循環測試結果吻合,而使用底部填膠 B 時則 能通過熱循環測試,較小的熱應不足以造成銲錫球的失效。而使用底 部填膠 B 和 C 在晶片角落產生的最大等效應力則分別為 60.9MPa 和 55.4MPa,使用兩種底部填膠在內連層產生較低的等效應力,在熱循環 試驗中都不足以造成內連層的失效,而結果可發現使用底部填膠 B 能 減少作用於銲錫球邊緣的應力但有較高的應力作用於內連層相較於底 部填膠 C。從表 3.1 可判斷底部填膠 C 有較高的熱膨脹係數和較低的彎 曲彈性模數導致有較大的熱應力產生作用於錫球,ㄧ般底部填膠擁有 較低的彎曲彈性模數會使內連層受到較小應力的作用以保護其內連 層,但由熱循環測試結果可知,過低的彎曲彈性模數將導致銲錫球的 失效。底部填膠 B 和 C 有很接近的性質,但只有使用底部填膠 B 時能 通過熱循環測試,可知選取合適性質的底部填膠對於覆晶封裝可靠度 的重要性。. 37.
(50) 圖 3.3 FEM 模擬應力分布圖 (a)Underfill B (b)Underfill C. 圖 3.4 使用底部填膠 C,熱循環測試錫球失效圖. 38.
(51) 表 3.1 底部填膠關鍵性質與應力分析結果 Source. NCTU. Type. Underfill Materials B Underfill Materials C. Tg (℃). 61.3. 60.2. CTE1 (ppm). 29.1. 34.7. CTE2 (ppm). 101.3. 102.5. E1 (GPa). 850. 710. E2 (GPa). 4.7. 4.0. Bump stress (MPa). 159.0. 176.2. 60.9. 55.4. Pass. Bump crack. Die corner low-k stress (MPa) Reliability result (TCT). 39.
(52) 第四章. 界面破壞機制與測量. 4.1 前言 在覆晶封裝中,包括內連層薄膜之間的界面強度和底部填膠與晶 片之間的界面強度為影響其可靠度的關鍵因素之ㄧ,本章將介紹界面 破壞力學的基礎理論,了解破壞力學的理論可幫助定義材料之間的界 面強度與失效的預測,本研究並建立了先進的界面強度量測方法,包 括兩種不同的模式四點彎矩試驗(Four Point Bending)和雙懸臂樑試驗 (Double Cantilever Beam)。. 4.2 線彈性破裂機制(Linear Elastic Fracture Mechanics) 如圖 4.1 所示[24],一線彈性材料中有一裂縫,裂縫受到一應力作 用使其成長,x1、x2 座標軸表示平面垂直於裂縫前緣。根據線彈性理論 模擬,在裂縫周圍的應力場,受到邊界效應影響,會因為裂縫及材料 的大小、形狀和受力的強度及分部情形而改變,且不考慮原子鍵結的 破壞過程,可以下式子表示:. σ ij (r ,θ ) =. K 2πr. ∑. ij. (θ ). (4.1). 其中 r:與裂縫前緣之距離. 40.
(53) θ:極性因子 K:應力強度因子。. 在計算複雜的邊界效應下,應力強度因子可以下式定義:. K = κσ L. (4.2). 其中 L:代表長度 κ:邊界效應定義的常數,與破裂長度和 L 的比例有關。. 例如在彈性平板中,有長度為 2a 的裂縫,而裂縫受到 σ 的拉伸應力, 則裂縫的應力強度因子可表示為:. K = σ πa. (4.3). 在線彈性材料中,當所受應力足以使裂縫成長,可以實驗最大承 受應力來定義材料的破裂強度 Kc (fracture toughness):. κσ c L = K c. (4.4). 41.
(54) 圖 4.1 線彈性材料裂縫式意圖,x1、x2 座標軸平面垂直於裂縫前緣. 4.3 能量釋放率(Energy Release Rate) 材料的破裂強度 Kc 必須經過複雜的邊界效應應力計算,所以利用 能量觀點來表示材料界面強度為更方便的表示方法。如圖 4.2 所示,一 線彈性材料中有一裂縫長度為 a 及界面面積 A,在受到一負載拉力 P 的作用下,負載點產生了位移距離 u,且同時裂縫長度在負載作用下成 長了 da 的距離,界面面積也增加 dA。材料在負載 P 作用下增加了彈 性位能–Π[25]:. 42.
(55) − ∏ = E STRAIN =. Pu 2. (4.5). 能量釋放率 G 可定義為裂縫成長時,每單位面積所釋放的能量,即:. G=−. ∂∏ ∂A. (4.6). P ⎛ ∂u ⎞ ⎛ ∂E ⎞ G = ⎜ STRAIN ⎟ = ⎜ ⎟ ⎝ ∂A ⎠ P 2 ⎝ ∂A ⎠. (4.7). P u. δA A δa. a. B. 圖 4.2 線彈性材料裂縫在拉伸作用力下成長[25]. 如圖 4.3 所示,因為 P 為常數,可得:. 43.
(56) u A u A+ dA = C A C A+ dA. PA = PA+ dA =. (4.8). ⎛ ∂u ⎞ ⎛ ∂C ⎞ ⎜ ⎟ = P⎜ ⎟ ⎝ ∂A ⎠ P ⎝ ∂A ⎠ P. (4.9). 其中 C(compliance)為材料的屈從性,而臨界能量釋放率 Gc 可定義為:. Gc =. 1 2 dC Pfracture 2B da. (4.10). 材料的屈從性會隨著破裂長度增加變大,兩者之間的關係可根據特殊 的結構計算得知。. P. Crack growth. 1/C. u uA + dA. uA. 圖 4.3 負載-位移曲線圖,裂縫成長趨從性變大[25]. 44.
(57) 4.4 混合模式破裂(mode-mixity fracture) 在破壞力學中,根據裂縫所受的應力模式,可歸納成以下三種不 同的破裂模式,包含模式一(mode I)拉伸模式、模式二(mode II)剪應力 模式及模式三(mode III)撕裂模式如圖 4.4 所示[26]。材料在三種破裂模 式作用下的應力強度因子 K 與能量釋放率 G 之間的關係可以下列方程 式表示:. 2 K I2 K II2 K III (1 + υ ) G= ' + + E' E' E. (4.11). 其中 KI、KII、KIII:三種破裂模式下的應力強度因子 E:材料彈性模數(Young’s modulus) υ:材料浦松比(Poisson’s ratio). 考量作用於 x-y 二維平面的作用力,主要為模式ㄧ與模式二拉伸與 剪應力的作用,其混合作用比例可以破裂相角度(fracture phase angle)Ψ 定義:. ⎛K Ψ = tan −1 ⎜⎜ II ⎝ KI. ⎞ ⎟⎟ ⎠. (4.12). 45.
(58) 當 Ψ = 0°時表示完全的模式一破裂由拉伸力作用,當 Ψ =90°時表示完全 的模式二破裂由剪應力作用,介於中間則為混合模式破裂。. Mode I. Mode II. Mode III. 圖 4.4 三種破裂模式圖示[26]. 4.5 巨觀界面破裂強度 材料本質的界面強度(intrinsic adhesion)Go 可視為其界面的化學鍵 結強度。而巨觀量測下得到的臨界界面強度 G c ,如圖 4.5 所示 Gc 與 Go 之間的關係可以下式表示[27]:. Gc = (ξ + χ + ζ) Go. (4.13). 其中 ξ:破裂界面形成時的能量損失 χ:表面不平整製造的額外能量 ζ:塑性變形造成的能量散失作用. 46.
(59) 不同的破裂模式將會造成不同程度的表面粗糙與塑性能量散失, 如圖 4.6 所示,在完全剪應力的破裂情況下,造成相當大的塑性能量 散失,而在完全拉伸應力破裂情形下,有較接近本質的界面強度。. 圖 4.5 巨觀量測材料界面強度[27]. 圖 4.6 界面強度隨著破裂模式不同而改變[27]. 47.
(60) 4.6 界面強度量測 傳統的界面強度測試方法,如 scotch tape 測試只能大約判斷其強 度好或不好[28],而 stud-pull 或者 shear test 會因為大量的塑性變形而 無法量測到其本質的界面強度[29,30],並且在針對薄膜間的界面強度 時,很難量測到希望量測的破裂界面強度。因此先進的界面強度量測 模式,利用層狀結構材料(sandwich),以計算薄膜界面破裂時的能量釋 放率來表示其界面強度,可更精準的控制破裂面,並減少塑性變形的 影響,更靈敏精準的量測界面強度。其中四點彎矩試驗(Four Point Bending)和雙懸臂樑試驗(Double Cantilever Beam)量測系統可利用不同 的破裂模式量測薄膜之間的界面強度。 本研究建立毫微米機械量測系統,如圖 4.7 所示,四點彎矩試驗或 雙懸臂樑試驗試驗,利用 Encoder Mike 線性控制(motion control)在控制 的固定位移速率下給予試片拉伸位移,其速度限制為 0.1μm/s 至 200μm/s,解析度為 0.1μm/s,所受負載則利用 Kyowa 荷重計量測,使 用荷重計的容量為 20N 及 100N,位移和負載荷重將由電腦紀錄,整體 量測系統由 Labview 軟體控制。 在固定的位移速率下,量測薄膜界面破裂時的臨界負載,可計算 薄膜界面在破裂時的臨界能量釋放率 Gc。. 48.
(61) Micromechanical Test System Actuator. Motion Control Card. 4 Point Bending. Power Supply. Load Cell. GPIB card. Multi-meter. Double Cantilever Beam. 圖 4.7 毫微米機械量測系統. 4.6.1 四點彎矩試驗(Four Point Bending) 四點彎矩試驗可用來量測晶片的內連層內薄膜材料包括銅和低介 電材料與阻隔層(SiC、SiN)之間的界面強度[31],其破裂模式為混合式 破裂,破裂相角度 Ψ 約為 43°。 四點彎矩試驗的層狀結構試片如圖 4.8 所示,dummy 晶片與 sample 晶片利用環氧樹脂膠黏結,FSG 薄膜主要目的為增強與環氧樹脂膠之 間的界面強度,或以電漿(plasma)處理晶片表面增加與環氧樹脂界面強 度以確保界面破裂出現在預期界面,試片的製作步驟如圖 4.9 所示,首 先依照希望量測薄膜界面備製層狀結構晶片,接著將層狀結構晶片與. 49.
(62) dummy 晶片切割成 70mm x 70mm 正方形,環氧樹脂膠 Epotek 375TM 利用 spin coating 在層狀結構晶片上,spin coating 速度先以慢速使環氧 樹脂膠均勻分部,然後第一段以 3000rpm 塗佈 30 秒,第二段以 6000rpm 塗佈 60 秒,再以 C 形夾和文書夾給予均勻壓力使環氧樹脂膠厚度均勻 如圖 4.10 所示,將環氧樹脂膠的厚度控制在 2μm 以下以減少其實驗時 力量受其分散影響,經過 150℃一個小時的硬烤之後,將其切割成 4mm x 70mm 長條形狀,最後在試片中央以鑽石切割機切出一 300~400μm 深度的刻痕,即完成試片備製。. 圖 4.8 四點彎矩試驗層狀結構試片. 50.
(63) 圖 4.9 四點彎矩試片製作流程. 圖 4.10 試片以 C 型夾固定. 51.
(64) 四點彎矩試驗的試片破裂結果如圖 4.11 所示,在界面出現破裂後 需確認破裂界面為所欲量測的破裂界面,不乾淨的破裂界面會有多餘 的能量散失,觀察方式可透過表面性質的差異,如銅與阻障層可由其 外觀和導電性的差異來判斷,或利用α-step 或 SEM 等觀察破裂面判 斷。而典型負載位移如圖 4.12 所示,給予足夠的負載使預留刻痕擴展 至破裂界面,可量測界面穩定破裂時所承受的臨界負載。. 圖 4.11 四點彎矩試片結果圖. 圖 4.12 四點彎矩試驗負載位移曲線圖 52.
(65) 四點彎矩試驗的界面臨界能量釋放率可以下式計算:. 21(1 − ν 2 ) PC2 L2 GC = 16 EB 2 h 3. (4.14). 其中 Pc:臨界負載荷重 L:支點間距 E:矽晶片彈性模數 ν:矽晶片的蒲松比 B:樣品寬度 h:晶片厚度. 本研究測量銅與 SiC、SiN 之間和低介電材料與 SiC 之間的界面 強度,結果如表 4.1 所示,銅和 SiC 之界面強度為 6.4 J/m2,銅和 SiN 之界面強度為 6.5 J/m2,低界電材料和 SiC 之界面強度為 2.9 J/m2,可 知在內連層內的薄膜之間的界面強度非常的弱,尤其是在低界電材料 的使用,如何減少內連層所受熱應力或增進其界面強度以避免其界面 出現剝離失效為封裝及後段連接上的重要議題。. 53.
(66) 表 4.1 內連層薄膜界面強度 Crack interface. Gc. SiC/Cu. 6.4 ± 0.8 J/m2. SiN/Cu. 6.5 ± 0.3 J/m2. Lowk/SiC. 2.9 ±0.9 J/m2. 4.6.2 雙懸臂樑試驗 底部填膠與晶片保護層之界面附著力,為影響其界面可靠度的關 鍵性質,如何量測其界面附著力,為覆晶封裝ㄧ項重要的課題,本文 利用經過改良過的雙懸臂樑試驗,理想雙懸臂樑試驗如圖 3.13 所示, 試驗中試片所受應力為完全拉伸應力,破裂模式為完全模式ㄧ破裂, 破裂相角度 Ψ 為 0°。究底部填膠與與矽晶片保護層之間的界面黏著強 度,因為底部填膠之厚度較厚,使用模式ㄧ破裂試驗可避免產生過多 的塑性變形能量,測得較接近本質的界面強度。根據樑臂理論(Beam theory)理想的雙懸臂樑試驗量測材料界面強度 G 可以下列式子計算 [32]:. 12 P 2 a 2 G= Eb 2 h 3. (4.15). 其中 P:負載拉力. 54.
(67) a:界面破裂長度 h:單懸臂樑厚度 b:懸臂樑寬度 E:懸臂樑彈性模數. 圖 4.13 理想雙懸臂樑試驗. 針對Si/UF/Si雙懸臂樑試驗,Kanninen以彈性支臂模型計算雙懸臂 樑試驗界面強度[33],Penado再利用Kanninen推導之結果求解懸臂樑中 間夾有黏著層(adhesive)之界面強度[34]。圖4.14為改良式雙懸臂樑試片 結構圖,量測底部填膠與矽晶片保護層的界面強度時,因為矽晶圓為 脆性材料,為了保護矽晶圓在試驗過程中不會發生斷裂,故以鋁合金 黏著於外側給予保護,並在晶片邊緣預留刻痕以減低界面破裂所需臨 界負載並確認界面破裂出現在晶片和底部填膠之間。. 55.
(68) 圖 4.14 Si/Underfill/Si DCB 試片. 本試驗方法為分析雙懸臂樑在到受應力作用下的變形量,計算其 支臂的屈從性與裂縫長度的關係,以方程式4.9分析其界面強度。 如圖4.15所示,將試片定義為兩部分,由A至B點定義為第一部分, B至C定義為第二部份,則A點受到拉伸應力作用時,受力點A的總變形 量可以疊加法(superposition)計算之:. δ A = δ A I + δ B II + dφ B II. (4.16). 其中δA:A點總變形量 δAI:第一部份中 A 點變形量 δBII:第二部份中 B 點變形量 dψBII :第二部份中 B 點轉動量. 56.
(69) 圖 4.15 雙懸臂樑試片變形量疊加示意圖. 利用有限元素模擬結果可知 δAI 相較於 δA 其變形量非常的小,我們 可以合理的假設 δAI 相近似於零,試片第一部份不易彎曲,將 δA 重新定 義為:. δ A = δ B II + dφ B. (4.17). 在 B 點的變形量需分別計算上支臂與下支臂之變形量,支臂如圖 4.16 所示,部分支臂受到黏著層支持,上下支臂可各自視為一彈性基座。 則 B 點的變形量可以ㄧ微分方程式表示之:. d 4α ( x ) + 4λ4 H ( x)α ( x) = 0 4 dx 57. (4.18).
(70) ⎧1 ⋅ ⋅ ⋅ x > 0 H ( x ) = ⎨ 其中 ⎩0 ⋅ ⋅ ⋅ x < 0. (4.19). k 4E x I. (4.20). λ4 =. Ex:支臂在 x 方向的有效彈性模數 I:支臂轉動慣量 k:基座彈性模數. 假設上支臂與下支臂彼此互不影響,而界面破裂於黏著層與上支臂, 則上支臂基座彈性模數(k top)可視為黏著層(kadhesive )與支臂(k adherend)串 聯作用:. k top =. 1 1 k adherend. +. 1. (4.21). k adhesive. 而下支臂基座彈性模數(kbottom)可簡單定義為:. k bottom = k adherend. (4.22). 而對於在平面應力作用下的均質材料,kadherend 與 kadhesive 可定義為:. 58.
(71) (1). k adherend =. 2E y b (4.23). heff ( 2). k adhesive. Ey w = ⋅ 2t 1 − υ xy ( 2 )υ yx ( 2 ). 其中 Ey(1):支臂在 y 方向的有效彈性模數 Ey(2):黏著層在 y 方向的有效彈性模數 heff:支臂的有效高度 b:支臂的寬度 w:黏著層的寬度. 圖 4.16 部分懸樑臂受到黏著層支持. 59. (4.24).
(72) 而在 B 點的變形量可解為:. δB. II. ⎡ λ3l 2 (2a + d ) ⎤ λ = α (−l ) = + A ⋅ l + B ⎢ ⎥ II 3 2 E x I II λ3 ⎣ ⎦ P. φ B II = −α ′(−l ) =. [. P λ3 (l 2 + 2dl ) + Aλ II II 3 2Ex I λ. (4.25). ]. (4.26). 則總變形量 δA 結合方程式 4.15、4.23 和 4.24 即為:. ⎡λ3l 2 (2a + d) ⎤ P δ A = II II 3 ⎢ + Aλ ⋅ l + B⎥ + II II 3 λ3 l 2 + 2dl + Aλ ⋅ d 3 2Ex I λ ⎣ ⎦ 2E I λ. [ (. P. ]. ). (4.27). 且額外的剪應變也必須考慮,則總變形量δA即為:. ⎡λ3l 2 (2a + d) ⎤ P + Aλ ⋅ l + B⎥ + II II 3 λ3 l 2 + 2dl + Aλ ⋅ d + δA = II II 3 ⎢ 3 2Ex I λ ⎣ ⎦ 2E I λ. [ (. P. ). ]. ⎛ 3lP ⎞ ⎜ ⎟ II II ⎜ 2bG h ⎟ ⎝ xy ⎠ (4.28). 結合上述方程式,則上支臂及下支臂在受力點相對的變形量可表示為:. 60.
(73) δA. top. ⎤ ⎡ λt 3 l 2 (2a + d ) λ A l B = + t t ⋅ + t⎥+ 3 ⎢ II II 3 2 E x I t λt ⎢⎣ ⎥⎦ ⎛ P 3lP 3 2 ⎜ λ λ + + ⋅ + l dl A d 2 t t t 3 II ⎜ 2bG II h II 2 E II I t λt xy ⎝ P. [ (. ). ]. ⎞ ⎟ ⎟ ⎠ (4.29). δA. bottom. ⎡ λb 3l 2 (2a + 2 ) ⎤ = + ⋅ + λ A l B b b t⎥+ II II 3 ⎢ 3 2 E x I b λb ⎢⎣ ⎥⎦ ⎛ P 3lP 3 2 ⎜ + + ⋅ + λ λ l dl A d 2 b b b II 3 ⎜ 2bG II h II 2 E II I b λb xy ⎝ P. [ (. ). ]. ⎞ ⎟ ⎟ ⎠. (4.30). 則雙懸臂樑試片的總變形量即為上下支臂變形量的總和:. δ = δ A top + δ A bottom. (4.31). 可得知雙懸臂樑試片的屈從性為:. (. ). ⎡ λt 3 2a 3 − 2d 3 ⎤ + At λt ⋅ a + Bt ⎥ + C = = II II 3 ⎢ 3 P E I t λt ⎣⎢ ⎦⎥. δ. 1. (. 1 E II I b λb II. 3. ). ⎡ λb 3 2a 3 − 2d 3 ⎤ ⎛ 3(a − d ) ⎜ + ⋅ + A a B λ ⎢ b b b⎥ + II II 3 ⎢⎣ ⎥⎦ ⎜⎝ bG xy h. ⎞ ⎟ ⎟ ⎠ (4.32). 61.
(74) 對於Si/UF/Si試片,其黏著層為底部填膠材料,而支臂為鋁合金與 矽晶片的複合材料,因為底部填膠有相對較薄的厚度及較小的彈性模 數,在試驗過程中,可忽略底膠層的剛性作用,則方程式3.30中:. It = Ib = I2. (4.33). I 2 為試片第二部份的截面轉動慣量,利用轉換斷面法(transformed section method)可計算鋁合金與矽晶元的複合材料截面轉動慣量,如圖 4.17 所示。而 h eff2 為試片第二部份的等效高度,由第二部份中心 軸截面轉動慣量 I2NA 計算可得:. heff 2. 12 I 2 =3 b. NA. (4.34). 圖 4.17 轉換斷面法計算截面轉動慣量. 62.
(75) 試片中矽晶片、鋁合金及底部填膠都以均質材料做計算,則可以 矽晶圓的彈性模數做為支臂的有效彈性模數。. II. Ex = E y. (1). = Es. (4.35a). II. G xy = Gs. (4.35b). Es 2(1 + υ s ). (4.35c). = EUF. (4.35d). υ xy ( 2 ) = υ yx ( 2 ) = υUF. (4.35e). Gs =. Ey. ( 2). 其中 Es:矽晶圓彈性模數 EUF:底部填膠彈性模數 Gs:矽晶圓的剪力模數 υs:矽晶圓的浦松比 υUF:底部填膠的浦松比. 試片的屈從性可簡化為下列式子:. C=∑. i =t ,b. (. ). 3 ⎤ ⎛ 3(a − d ) ⎞ 1 ⎡ λi 2a 3 − 2d 3 2 2 ⎟ a a 2 2 1 λ λ + ⋅ + ⋅ + ⎥ + ⎜⎜ t t 3 ⎢ ⎟ bG h 3 Es I 2 λi ⎣ ⎦ ⎝ s eff 2 ⎠. (4.36). 63.
(76) 而能量釋放率 在ㄧ受力 P 及裂縫長度 a 作用下可表示為:. P ⎧⎪ 1 G= ⎨ 2w ⎪⎩ 2 E s I 2. ∑. i = t ,b. ⎡ 2 2 4a ⎤ ⎛⎜ 3 + + + a 2 ⎢ ⎥ λi 2 λi ⎥⎦ ⎜⎝ bG s heff 2 ⎢⎣. ⎞⎫⎪ ⎟⎬ ⎟⎪ ⎠⎭ (4.37). 雙懸臂樑試驗量測界面破裂長度成長時試片所受的負載及其屈從 性,以方程式 4.35 分析其破裂距離 a,再用 4.36 式計算其臨界能量釋 放率 Gc 值,以計算方式分析破裂距離可以省略實驗量測破裂距離的步 驟,實際量測界面破裂距離有其困難之處,因為 Si 與底部填膠界面破 裂距離變化量很小難以量測,故以計算方式分析破裂距離為較方便的 方法。 底部填膠與晶片保護層 DCB 試驗試片準備步驟如圖 4.18 所 示[35],準備 70mm x 5mm 和 66mm x 5mm 大小 SiN 晶片和 76mm x 5mm 大小鐵弗龍薄片,將鐵氟龍薄片中心部位切割出 70mm x 3mm 凹槽,使用鐵氟龍脫膜劑在 70mm 長矽晶片一端噴上 30mm 長鐵氟 龍薄膜,其目的是再晶片邊緣預先產生破裂,接著將二矽晶片與鐵 氟龍薄片如圖 4.18 所示堆疊並以文書夾固定,SiN 晶片中間將形成一 與鐵氟龍厚度相同的間隙,如圖 4.19 所示,將試片至於加熱板上預熱 至 90℃以提升底部填膠流動速率,使用注射器將底部填膠注射於 64.
(77) SiN 晶片邊緣凹槽處,利用毛細現象使其填滿試片之間隙,然後將 試片至於烘箱依標準程序硬烤使底部填膠固化,硬烤完成後將鐵氟龍 薄片從間隙中取出,最後將鋁合金支臂以環氧樹脂膠黏著於試片兩 側完成試片。. 圖 4.18 DCB 試片製作流程圖. 65.
(78) 圖 4.19 底部填膠厚度. 底部填膠材料 B 與 SiN 晶片的實驗結果破裂面如圖 4.20 所示,破 裂面出現在底部填膠 B 與 SiN 晶片之間。而其負載位移關係如圖 4.21 所示,試片位移以每秒 3μm 速率給予拉伸力量,在負載至約 23N 時, 可打開預留的破裂界面,而在位移至約 750μm 時 SiN 和底部填膠 B 受 到約 0.9N 負載開始發生界面穩定破裂成長,分別於位移在 800μm 及 1000μm 時計算試片卸載時的負載-位移斜率的倒數為其屈從性,如圖 4.22 所示。試片的破裂長度可利用 4.35 利用量測得屈從性式計算出分 別為 26.7mm 和 29.7mm,再以 4.36 式計算其界面強度為 32.9 J/m2。而. 66.
(79) 底部填膠 C 和 SiN 晶片則有更好的界面強度,雙懸臂樑試驗中,無法 在其界面造成破裂,負載過程中,矽晶片支臂會因為過大的負載而發 生斷裂。觀察兩種底部填膠的組成成分可發現,如表 4.2 所示,底部填 膠 C 有添加額外的附著力增強添加物(silane adhesion promoter),其結 構式如圖 4.23 所示,在底部填膠內添加 silane adhesion promoter,可在 其界面上形成 Si-O 鍵結以提高其界面的強度[36],如圖 4.24 所示,故 底部填膠 C 與 SiN 晶片之界面強度較底部填膠材料 B 良好,添加 silane adhesion promoter 可有效提供底部填膠與保護層間之界面強度。。. Pre-notch. 圖 4.20 底部填膠 B/SiN DCB 試片破裂面. 圖 4.21 DCB 試驗底部填膠材料 B 荷重-位移圖. 67.
(80) 圖 4.22 DCB 試片屈從性分析其破裂長度. 68.
(81) 表 4.2 底部填膠材料化學組成成分. Composition Component Epoxy resin Filler. Underfill B Bisphenol F. 10~30%. Bisphenol F. Bispheno A. 1~5%. Bisphenol A. >5%. Fused Silica. 40~70%. Fused Silica. 50~60%. Amined-based. Hardener. Underfill C. 5~10%. Phenolic resin. 20~30%. 20~30%. 4,4'-metilenbis(2-etilanilina) Adhesion promoter. Additive. 3-(2,3-epoxypropoxypropyl) trimethoxysilane. 圖 4.23 附著力增強添加物結構式. 圖 4.24 附著力增強添加物反應式 69. <5%.
(82) 第五章. 結論與未來建議. 本研究建立了對底部填膠的熱性質及機械性質量測方法,利用熱 機械分析(TMA)、示差掃描熱量計(DSC)、奈米壓痕儀(NI)和四點彎矩 試驗(4PT Bending)量測底部填膠的熱膨脹係數(CTE)、玻璃轉換溫度 (Tg)、彈性模數(E)、硬度(H)、彎曲彈性模數(Ef),量測正確的材料性 質為有效模擬分析的必要條件,根據本研究結果可發現由廠商提供的 材料性質數據有需要重新驗証。 本研究的模擬結果與熱循環測試實驗結果有很好的相聯性,熱 循環測試中錫球的破裂位置,與模擬分析中最大熱應力位置相同,且 較高的熱應力才能引起其失效,應力模擬搭配熱循環測試,可有效的 預測錫球的可能失效位置,及其臨界所能承受的熱應力。而模擬分析 的結果,對於高鉛銲錫的使用,選擇低熱膨脹係數和高彈性模數的底 部填膠,能有效減低其所受熱應力並提升其可靠度,但相對會提高在 晶片角落的熱應力,要同時保護錫球和晶片的內連層,須選擇性質同 時能保護兩者的底部填膠。 針對薄膜界面的強度,本研究建立薄膜的界面強度量測方法,包 括四點彎矩和雙懸臂樑試驗為有效的薄膜界面強度量測方法,可量測 高精準度、高靈敏度的界面強度比較值,並可分析在不同破裂模式下. 70.
(83) 的界面強度。從界面強度測試結果中可發現晶片內連層內之薄膜材料 間的界面強度相當微弱,即使很小的殘留應力,也有可能造成其界面 的失效。 經過本次研究後,對於未來的研究建議,底部填膠的性質研究 與改善,可進一步從其化學組成結構進行改變,自行配製性質優良的 底部填膠,底部填膠為一環氧樹脂為基材的混合物,不同材料配上不 同的比例都會影響其性質,利用模擬分析可找出底部填膠的合適性 質,更重要的是能進ㄧ歩製備出合適性質的底部填膠。 在封裝體的應力分析上,可自行建立模擬系統,模擬分析封裝 體的力學現象為預測封裝可靠度的重要依據,包括錫球可靠度與熱應 力的模擬,材料薄膜界面強度與熱應力的模擬,建立模擬系統,可做 更全面的研究討論。雖然電腦能夠模擬複雜結構在熱循環下所售到的 熱應力分布情形,但能以實驗數據佐證,更可提升模擬結果的可靠 度,建立實驗量測材料受熱應力的分佈情形,如雲紋干涉法(Laser Moiré Interferometry)、彎柄儀(Bending Beam)等以光學原理量測熱應 力和分布,可做更全面的分析討論。 對於材料界面強度的量測,除了本質的材料界面強度外,可進 ㄧ歩研究實際環境因素對於界面附著力的影響,建立溫溼度環境控制 條件,可幫助了解溫度及溼度對於材料的界面強度及其可靠度的影. 71.
(84) 響,在了解材料的本質界面強度後,如何增進其界面強度已提高其可 靠度也是重要的研究,可利用界面強化物的添加或表面處理等方法進 行材料界面強化的研究。. 72.
數據
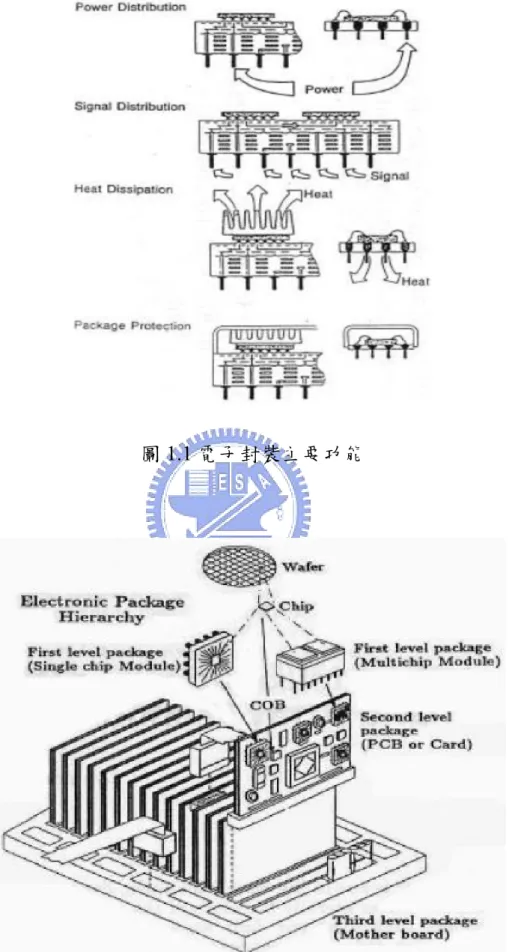



相關文件
The min-max and the max-min k-split problem are defined similarly except that the objectives are to minimize the maximum subgraph, and to maximize the minimum subgraph respectively..
By comparing and analyzing the advantages and disadvantages of using the FRP molded panels and hard PS insulation material on roof insulation and waterproof with the
Cheng-Chang Lien, Cheng-Lun Shih, and Chih-Hsun Chou, “Fast Forgery Detection with the Intrinsic Resampling Properties,” the Sixth International Conference on Intelligent
Zhong, "Design for Enhanced Solder Joint Reliability of Integrated Passives Device under Board Level Drop Test and Thermal Cycling Test," Electronics Packaging
Hwang, “An O (nk)-time algorithm for computing the reliability of a circular consecutive-k-out-of-n:F system,” IEEE Trans on Reliability, Vol.. Shantikumar, “Recursive algorithm
How, ”An Itermetallic Study of solder joints with Sn-Ag-Cu Lead-Free Solder,” Electronics Packaging Technology Conference ,2000,p.72. Poborets, “Evaluation of Moisture Sensitivity
Lee, ”Effects of Build-Up Printed Circuit Board Thickness on the Solder Joint Reliability of a Wafer Level Chip Scale Package (WLCSP),” IEEE International Symposium
This study observed that (1) micro bump with underfill reduces the DNP corner wrapage and bump with underfill does not provide a better DNP corner wrapage; (2) bump with