限制理論應用在晶圓廠晶圓母體庫存建立之實證研究
56
0
0
全文
(2) 限制理論應用在晶圓廠晶圓母體 庫存建立之實證研究 研 究 生:林金生. Student : Jin-Sheng Lin. 指導教授:李榮貴 博士. Advisor : Dr. Rong-Kwei Li. 國 立 交 通 大 學 管理學院(工業工程與管理學程)碩士班 碩 士 論 文. A Thesis Submitted To Department of Industrial Engineering College of Management National Chiao Tung University In Partial Fulfillment of The Requirements For The Degree of Master In Industrial Engineering June 2006 Hsinchu, Taiwan, Republic of China. 中 華 民 國 九十五 年. 2. 六 月.
(3) 限制理論應用在晶圓廠晶圓母體 庫存建立之實證研究 研 究 生:林金生. 指導教授:李榮貴 博士. 國立交通大學管理學院(工業工程與管理學程)碩士班 摘 要 在半導體供應鏈管理系統中,企業仍依循傳統以預測的方式決定庫存量水準與生 產安排。由於市場需求改變之不可預測性,也就常造成所謂預測之高度不準,導致依 預測方式生產時,不是產生過高之庫存,就是缺貨連連造成顧客抱怨與公司損失。本 研究即應用限制理論之拉式供應鏈配銷管理觀念與方法於晶圓廠晶圓母體庫存之生 產,驗證限制理論拉式的緩衝庫存管理方式可以幫助公司降低整體的庫存水準或缺貨 次數以及滿足客戶的需要。實際驗證結果顯示,限制理論拉式的緩衝庫存管理方式在 有效產出天‧元 ( Throughput-Dollar-Days ; TDD ) 與存貨天‧元 ( Inventory- Dollar Days ; IDD ) 的績效之整體衡量結果,優於驗證前之表現。. 關鍵字:供應鏈、限制理論、需求-拉式、緩衝管理. I.
(4) The Application of TOC Demand-Pull and Buffer Management To The FAB Wafer Bank Build Up Student : Jin-Sheng Lin. Advisor : Dr. Rong-Kwei Li. Department of Master Program of Industrial Engineering and Management National Chiao Tung University. Abstarct In semi-conductor industry supply chain and distribution management system , the enterprises still follow the traditional sales forecast to determine inventory level and production arrangement. However, the market demand is variable and unpredictable; the sales forecast can never be accurate. To use the unreliable sales forecast to plan the production, the enterprises usually have high inventory on slow moving parts, or supply shortage. The enterprises are suffered by the customer complaints and losses from the inefficient production plan. The study of supply chain and distribution management system, Dr. Goldratt starts the theory of constraints (TOC), and develops a demand-pull and buffer management model which can solve this kind of problems. This research is trying to apply this solution plus TOC performance measurement index TDD(Throughput-Dollar-Days) and IDD (Inventory-Dollar-Days) to the case study of FAB wafer bank build up. The result has proved the method is valid. Keywords: Supply Chain, TOC Demand-Pull, Buffer Management, TDD (Throughput-Dollar-Days ), IDD (Inventory-Dollar-Days). II.
(5) 誌 謝 時間飛逝,應於兩年前就該完成之學業,由於近年來面對工作上接腫而來之新挑 戰,加上人之惰性,讓論文進度近乎半牛步狀態。本論文於最後一刻得以順利完成, 首先要感謝恩師 李榮貴教授,感謝您悉心加耐心的指導與鼓舞。再者要感謝工作上 長官之關心支持,年邁雙親與家人之期盼,還有羅文明同學不斷的給我加油打氣,給 我很大動力。感謝 張盛鴻與 蔡志弘老師百忙中,抽空擔任口試評鑑委員,給我很多 寶貴建議與論文缺失之指正,使我獲益良多。還有要特別感謝堤歐西管理顧問公司顧 問 王勇華先生在論文撰寫之初給與之提攜指引與建議。最後也非常感謝同事們的協 助,提供我寶貴資料,讓我能順利完成論文。 在此感謝指導過我的所有師長與一起學習成長的同學,讓我得到很多有益於工作 與人生之新知與觀念,還有要感謝賢內助—美足,任勞任怨對家庭默默的付出與對我 全心全力的支持,讓我能在繁忙工作之餘,家庭得以妥善照顧與個人學業得以順利完 成。 畢業了,心喜完成了人生中一新的里程碑。然而在面對未來更多新的挑戰時, 也同樣要秉持著 "積極主動", "全力以赴", "團隊合作", "雙贏思維" 與 "持續成長"之原則,像時代的巨輪一樣,不停往前邁進。. 林金生 謹誌 于交大工工管碩士專班 中華民國九十五年六月. III.
(6) 目錄. 摘要 .............................................................................................................................................. I Abstract .................................................................................................................................... II 誌謝 .............................................................................................................................................III 目錄 .............................................................................................................................................IV 圖目錄 .........................................................................................................................................V 表目錄 .......................................................................................................................................VI 第一章 緒論 .............................................................................................................................1 1-1 研究背景與動機 .......................................................................................................1 1-2 研究目的與方向 .......................................................................................................2 1-3 研究架構與方法 .......................................................................................................2 1-4 研究範圍與限制 .......................................................................................................3 第二章 文獻探討 .....................................................................................................................5 2-1 供應鏈管理 ................................................................................................................5 2-2 限制理論 ..................................................................................................................12 2-3 限制理論Demand-Pull緩衝管理模式 ..................................................................14 第三章 個案研究與分析 .........................................................................................................21 3-1 現行作業 ..................................................................................................................21 3-2 依現行作業銷售預測與Demand-Pull緩衝模式不同銷售情境探討 ...............23 3-3 現行作業與Demand-Pull緩衝模式結果與分析 ................................................ 35 3-4 停售產品的運作模式 ............................................................................................ 43 第四章 結論與建議 ................................................................................................................ 44 4-1 結論 .......................................................................................................................... 44 4-2 建議 .......................................................................................................................... 45 參考文獻 ................................................................................................................................... 47. IV.
(7) 圖目錄. 圖1-1 研究架構圖 ......................................................................................................................2 圖2-1 供應鏈管理五大驅動元素 ............................................................................................6 圖2-2 將資料分享於整條供應鏈的好處 ...............................................................................8 圖2-3 同步化供應鏈之存貨流程 ................................................................................................8 圖2-4 限制理論架構圖 ...........................................................................................................14 圖2-5 典型供應鏈管理衝突圖 ..............................................................................................15 圖2-6 Demand-Pull 補貨模式圖 ...........................................................................................17 圖2-7 統計變異示意圖 ...........................................................................................................19 圖2-8 緩衝管理示意圖 ...........................................................................................................19 圖3-1 產品銷售比例 ...............................................................................................................21 圖3-2 Code轉子體產品客戶下單到出貨之作業流程圖 ...................................................22 圖3-3 產品AA5794緩衝庫存圖 ............................................................................................34 圖3-4 產品AA5794 修正銷售需求後緩衝庫存圖 ............................................................35 圖3-5 現行作業TDD與TOC Demand-Pull TDD月分佈圖 ................................................38 圖3-6 現行作業IDD與TOC Demand-Pull IDD月分佈圖(在庫庫存) .............................38 圖3-7 現行作業IDD與TOC Demand-Pull IDD月分佈圖(在庫+在途庫存) ..................39 圖3-8 在庫庫存—現行作業與TOC Demand-Pull月分佈圖 .............................................40 圖3-9 在途庫存—現行作業與TOC Demand-Pull月分佈圖 .............................................40 圖3-10 在庫/在途庫存—現行作業與TOC Demand-Pull月分佈圖 ................................41 圖3-11 晶圓投片—現行作業與TOC Demand-Pull月分佈圖 ...........................................41 圖3-12 整廠晶圓投片與產能比較之月分佈圖 ...................................................................42 圖3-13 TOC Demand-Pull 研究品項之每日晶圓投片之日分佈圖 .................................42 圖4-1 銷售需求曲線加入緩衝管理圖 ..................................................................................45. V.
(8) 表目錄. 表2-1 預測方法使用的比例表 ..............................................................................................10 表2-2 傳統補貨系統之優缺點比較彙整表 .........................................................................12 表3-1 模擬依銷售預測與Demand-Pull方式下之晶圓補貨與庫存比較 .........................25 表3-2 模擬依銷售預測與Demand-Pull方式下之晶圓補貨與庫存比較 .........................26 表3-3 模擬依銷售預測與Demand-Pull方式下之晶圓補貨與庫存比較 .........................27 表3-4 模擬依銷售預測與Demand-Pull方式下之晶圓補貨與庫存比較 .........................27 表3-5 模擬依銷售預測與Demand-Pull方式下之晶圓補貨與庫存比較 .........................28 表3-6 模擬依銷售預測與Demand-Pull方式下之晶圓補貨與庫存比較 ........................29 表3-7 情境討論彙整表 ...........................................................................................................29 表3-8 調節緩衝庫存作業 .......................................................................................................31 表3-9 調節緩衝庫存作業 .......................................................................................................32 表3-10 現行實際作業與模擬TOC Demand-Pull緩衝庫存生產值比較(在庫庫存) ......36 表3-11 現行實際作業與模擬TOC Demand-Pull緩衝庫存生產值比較(在途庫存) ..... 37 表 3-12 個別品項 IDD/TDD 改善情行 ...................................................................................37. VI.
(9) 第一章 緒 論 1.1 研究背景動與動機 俗話說:[水能載舟,亦能覆舟] ,存貨對一企業如同水之於舟。存貨建立能有助 於企業應付生產與市場需求之不確定,或因產能固定,以此來調節淡旺季生產,確保 交貨順暢與客戶需求能有效被滿足。適當合理之存貨建立有助於公司營運,提升競爭 優勢,然而存貨管理不善導致交貨不順,也會而此造成企業之停工缺貨,進而客戶報 怨與訂單流失而造成公司損失。或者企業基於對於市場過度憧憬而盲目的建立庫存, 造成資金成本積壓,當市場需求改變往往造成呆滯報廢損失,嚴重者恐影響公司資金 週轉,甚至會招來公司營運危機。 近年來因美國安隆事件喚起主管機關與企業對公司治理之重視,而存貨管理亦是 公司治理重視之一環。從各報章雜誌報導上可知,專業投資法人在投資標的選擇上, 供應鏈體系或個別企業之存貨水準已成為一重要投資參考指標。故公司經營階層莫敢 輕忽存貨水準之控管。在以顧客優先的今日,企業也普遍存在"以客為尊"理念,要 傾聽客戶聲音,並充份滿足"顧客需求"已成為企業經營之首要經營指導原則。存貨 的供應力是顧客服務中最重要的一環,而實體的存貨很難轉換成流動資產,因此存貨 是一種非常高風險之投資,故如何在存貨水準與顧客服務水準間拿捏,也正考驗企業 經營者之智慧。 在半導體供應鏈系統中,傳統上仍依循以銷售需求預測—推式(Push)的方式來決 定生產與庫存量水準,不可避免也陷入供應鏈中所謂長鞭效應(Bull Whip Effect)之泥 沼中,導致常有庫存過高或者缺貨產生,造成顧客抱怨與公司損失。而消費性電子 IC 普遍存在著消費性產品之特有特性,對產品價格敏感度相對高,產品與競爭對手相互 替代性高,客戶要求短生產週期,終端銷費產品生命週期短,自然的要做銷售需求預 測也就不容易。而通常生產預測又以銷售需求預測為依據,也普遍假設著銷售需求預 測是精準的,幻想著依之以求得擁有較低庫存水準確享有高客戶服務水準。運氣好當 然如願以償,運氣不好,前述之高庫存或缺貨也就不斷發生。何以常感慨後者之機率 1.
(10) 較高呢 ? 因為架構在一高度不確定之基礎上做生產安排,自然險象環生,前述之高庫 存或缺貨如何能不發生呢 ? 一般人皆認為造成上述供應鏈問題最大核心原因是預測不準、供應商不可靠與補 貨時間太長所致,同時不易克服。高德瑞特博士(Dr. Eliyahu M. Goldratt) 所倡導的限 制理論(Theory of Constraints ; TOC)卻不以為然,認為現實生活中,衝突其時是不存 在的,存在的是我们對衝途有錯誤之認知和假設。限制理論以科學之方法,確近乎常 識管理思維程序,發展出一套 Demand-Pull 拉式的緩衝管理模式來有效的解決上述 供應鏈上配銷管理上所遇到之問題,基於此而產生研究之動機。. 1-2 研究目的與方向 半導體產業發展已愈趨成熟且競爭愈趨激烈,是投資報酬起伏劇烈或形容成燒錢 之產業也不為過。面對高投資高風險低微利時代,如何透過好的之管理方法與策略, 以降低營運風險與成本,同時強化競爭優勢,適時滿足顧客需求與提升獲利已成經營 者一重要課題。限制理論以嚴謹之因果邏輯關係之思維程序(Thinking Process),發展 出系列的企業管理應用解決方案且已被廣範而有效的應用在生產管理、專案管理、財 務管理、配銷管理、市場行銷與人的管理上,讓企業組織得到顯著的改善與巨大利益。 W公司訂單式轉子體生產模式之消費性IC產品,正面對高度市場需求不確定之生 產模式下,顧客要求短生產週期,工廠必須事先備足晶圓母體,以隨時滿足顧客。一 來要避免接到訂單無法交貨窘境,同時避免需求不確定而產生過高存貨甚至造成呆 滯。此研究目的希望能以限制理論 Demand-Pull 拉式庫存緩衝管理模式為基礎,來提 高顧客服務水準同時又兼顧合理庫存水準,以提升企業之彈性應變能力與達成生產管 理目標--短生產週期、低庫存與準時交貨以滿足顧客需求,提高企業獲利。. 1-3 研究架構與方法 茲將資料蒐集與研究架構圖分述如下 : (1) 蒐集W公司消費性接單轉子體產品,自2003年到2004年在晶圓母體站"7919"平 2.
(11) 均存貨佔前80%產品之銷售資料與晶圓投片、晶圓母體庫存相關生產資料。 (2) 統計現行作業模式下之晶圓母體庫存水準,缺貨狀況與 IDD/TDD 值。 (3) 模擬限制理論 Demand-Pull 之緩衝庫存生產方式建立晶圓母體庫存,並統計晶 圓母體庫存水準、缺貨狀況與 IDD/TDD 值。 (4) 透過現行作業模式與應用限制理論 Demand-Pull 兩者做TDD/IDD值比較,驗證 後者生產方法整體而言有較佳結果。 (5) 研究架構圖說明如圖 1-1 所示. 研究方向. 研究目的. 資料蒐集與文獻探討. 現行作業模式 之 TDD 與 IDD. TOC Demand-Pull模. 式之 TDD 與IDD. 兩者模式比較分析 結論與建議. 圖 1-1 研究架構圖. 1-4 研究範圍與限制 本研究的範圍與限制說明如下: (1) 僅限於以“W"公司半導體消費性IC產品—訂單式接單轉子體生產模式,必 須事先依於晶圓廠建立晶圓母體之產品做研究。 (2) 晶圓針測良率是變動的,為便於研究採預測固定值。 (3) 晶圓廠製程複雜,每批晶圓之生產週期會有長有短,便於研究採預測固定值。 3.
(12) (4) 晶圓或粒銷售價格會隨時空改變而變動,為易於研究,採用2003年到2004 年產品品項之總銷售平均價為一固定值。 (5) 為易於研究不考慮晶圓投片日產能上限。. 4.
(13) 第二章 文獻探討. 2.1 供應鏈管理 根據美國生產與存貨管理學會 (APCIS) 對供應鏈與配銷的定義:供應鏈是從原 料端到最終端的產品使用者的一種程序,供應鏈整合與同步化此鏈中所有參與之程 序、人員與組織。而配銷是將物料成品或零件,從製造商送到客戶間的有關活動。基 本上有三種成員參與供應鏈與配銷的活動—產品製造者(例如生產工廠)、配銷通路內 成員(例如區域發貨倉庫)、最終尾端客戶(例如零售商)。這些成員可能屬於同一公 司,也可能分屬不同公司。[8] 供應錬管理是一種追求最佳組合的協調工作,意圖將供應鏈上所有生產、存貨、 地點和運輸等活動的參與者結合在一起,以便對服務的市場做出最適的回應,並能兼 顧企業利益。市場變遷的節奏和產業不確定,逼迫著企業不得不去明瞭自己所處在的 供應鏈和自己所扮演的角色,企業如果知道如何去建構強勢優良的供應鏈並參與其 中,將使自己擁有超群的競爭優勢。今天這快速變化的市場和科技環境裏,企業唯有 專注改善自己的核心競爭力,才是生存發展正途。有效供應鏈的管理必須能改善顧客 服務水平,同時又能促進各公司之內部營運效率。顧客服務最基本的定義就是訂單出 貨率高,準時交貨率高,退貨率低(不管任何原因)各公司的內部營運效率則是這些 組織在存貨和其他資產上面的投資可以得到較高之報酬,並找到降低營運成本和銷售 費用的方法。供應鏈管理是參與其中的企業進行生產、存貨、地點和運輸之協調,以 便在"回應能力"和"營運效率"上取得最佳組合來服務市場(如圖 2-1)。其目的或 使命,可以引用高德瑞特的話:「增加產出同時減少存貨和營運費用」來加以定義。[1]. 5.
(14) 1. 生產. 2. 存貨. (何物、如何、何時). (生產多少、儲存多少). 5. 情報 (上述四項決策的 基礎) 4. 運輸 ( 於何時用什麼方式來運 送產品). 3. 地點 (何處是從事某種項活 動的最佳選擇). 圖 2-1 供應鏈管理五大驅動元素圖 (資料來源:Michael Hugos [1]) 早期供應鏈是企業主導它要提供什麼樣的商品給客戶,非真正以客戶需求為核 心。因此供應鏈管理的再好,也僅能儘量減少因客戶需求變動所造成的影響。 以顧客優先的今日,如何以顧客為主軸創造顧客的價值,就成為下一階段企業 競爭力強弱的關鍵。誰能愈快掌握這種新的商業模式型,誰就能更快主宰市場。 而所謂的以顧客為主軸,就是以顧客的需求為出發點,依其需求之種類,快速 的拉動整個供應鏈,提供顧客需求的產品。[4]. 2.1.1 長鞭效應 今日供應鏈的挑戰與日俱增,主要在於需求端的改變,帶動整個供應鏈體系的變 動,談到客戶需求難測,善變及沒耐心的特性,就不得不談起供應鏈管理中著名的「 長鞭效應」。長鞭效應是將供應鏈視為一條長鞭,需求端在鞭柄,而供應端在鞭稍, 當需求端有些微變動時,好像輕輕甩動鞭柄,就會造成鞭子未稍巨幅擺動。供應鏈中 越往上游走,訂單數量變異性越增大的現象就是所謂由於下游需求資訊之誤差,造成 越往上游的需求變異數變動過大,形成長鞭效應,導致供應鏈之無效率。如剩餘或不 6.
(15) 足之產能、產品預測品質低、存貨過高、過多待補訂單、無效運輸、客戶服務品質低 落、過高的修正成本、不確定之生產規劃及延誤生產時程等無效率之營運。. 長鞭效應之所以會被引發,都因為資料的傳遞有時間差,而大家對市場需求又缺 乏總體大圖像,形成長鞕效應之成因眾多,根據張福榮[5]可歸納 5 點如下: 1. 需求預測之不易 2. 前置時間不易掌握 3. 批次訂單 4. 價格變動 5. 誇大的訂單. 而克服長鞭效應之 4 要點作法如下 : 1. 降低不確定性 2. 降低變異性 3. 減少前置時間 4. 建立略聯盟關係. 供應鏈在不同階段或位置的企業對市埸需求有不同見解而導致供應鏈協調中 斷,也因此常造成企業一開始是應付產品短缺,後來應付的卻是產品供應過剩。而企 業又普遍存在著此為無可避免的事,而單打獨鬥以強化自身能力方式來因應需求波 動,其實倘偌企業能聯合起來交換市場情報,從需求波動者本身著力的話,效果可能 更好更快。事實上雖然我們知道企業間分享情報有其困難與顧忌,但我們也知道假如 無法準時交貨的原因是其供應商遲交,顧客可能調頭走人,跑去向你的競爭者買貨, 因為那邊的供應商準時交貨,所以這已不是公司對公司之競爭了,而我們可看到供應 鏈對供應鏈之競爭會越來愈普遍。能合作共創有效供應鏈的企業將是未來大贏,而能 想出好辦法效分享資料的企業能創造最有力之供應鏈,顧客會被吸引到有效率之供應 鏈,因此有效率者終將瓜分效率較差者之市場。將資料分享於整條供應鏈的好處,使 7.
(16) 整條供應鏈可以變的更有效率。說明如圖 2-2 所示[1]:. 高. “Y” 供應鏈. 這條供應鏈保持較高的存貨 水平確只與競爭供應鏈提 供約略相同的顧客服誤水準. 存貨 水平. 競爭供應鏈. 低. 高. 服務水準. 圖 2-2 將資料分享於整條供應鏈的好處圖 (資料來源:Michael Hugos [1]) 對抗長鞭效應有效方法即將整個供應鏈視為一體,並將它的作業步調調整到 與實際市場需求同步。說明如圖 2-3 所示[1]:. 銷售和預測資料. 原物料. 緩衝. 製造廠 商. 緩衝. 配銷商. 緩衝. 零售商. 緩衝. 圖 2-3 同步化供應鏈之存貨流程 (資料來源:Michael Hugos [1]). 8. 市場需求.
(17) 2.1.2 需求預測 供應鏈管理決策的根基是預測,預測那種產品將為市場所需,需要多量,什麼時 候需要,需求預測也因此變成了許多公司制定內部作業計劃和彼此合作以滿足市場需 求之基礎,依 Michael Hugos[1] 所言,所有需求預測都是在處理四項重要變數,以判 定市場情況此四項變數為 : 1. 需求(Demand) 2. 供給(Supply) 3. 產品特殊(Product Characteristics) 4. 競爭環境(Competitive Environment). 需求預測指的是整個市場對某一種產品群或服務的需求量而銷售預測是預測某 個特定企業之產品在其所屬市場範圍內的需求,另列出四種基本預測方法 : 1. 定性分析(Qualitative) 2. 因果分析(Causal) 3. 時間序列(Time Series) 4. 模擬(Simulation). 定性分析依賴個人對市場的直覺或主觀判斷,因果分析法假設需求與某特定環境 或市場因素有密切關係,時間序列是最普遍用來做預測,其基本假設是歷史會重演, 過去型態是未型態很好指標,諸如:移動平均法和指數平滑法,模擬法則是因果分析 和時間序列之組合,用以模擬在不同情境下消費者可能行為。大多企業使用幾種方法 來做預測,然後再將這些預測結果結合起來,寫成自己真正的預測。需求管理所探討 之內容包括需求規劃與需求履行甚至包含客戶關係管理之探討,企業推動需求規劃之 主要目的在於找出一套有效的市場需求計劃,以了解產品之銷售與需求預測,其基本 內容包含[4]: 1. 需求預測〈Demand Forecasting〉 (1) 由上而下預測法〈Top Down Forecasting〉 。 9.
(18) (2) 由下而上預測法〈Bottom-Up Forecasting〉。 (3) 生命週期規劃法〈Life Cycle Planning〉。 (4) 行銷事件規劃法〈Event Planning〉。 (5) 相依需求預測法〈Dependent Demand Forecasting〉。 (6) 共識預測法〈Consensus Forecast〉。 2. 需求協同作業〈Demand Collaboration〉。 3. 彈性限制規劃〈Flex Limit Planning〉。 4. 淨預算值之計算。 在 J. Scott Armstrong所編的Principles of Forecasting 一書中提到幾種方 法被使用的比例,如表2-1所示[17]:. 表 2-1 預測方法使用的比例表(資料來源: Armstrong [17]). 在上表中可以發現,專家意見的預測方式佔較高使用比重,而在Armstrong 的書 中也列舉了相當多的問卷調查結果,顯示大多數的企業對於銷售預測方法的選擇上, 儘管越來越進步的預測工具不斷出現,企業似乎還是選擇用專家意見來作預測,如業 務人員或專業經理的預估為準,甚至有些調查結果中顯示還高達87%的受訪企業是運 用專家意見來作銷售(需求)預測的。然而,雖然專家意見佔了舉足輕重的角色,量. 10.
(19) 化的工具也不可忽視,因為大多數專家意見的基礎是來自一些量化工具分析的結果, 如移動平均預測法(Moving Average Forecast)或指數平滑預測法(Exponential Smoothing Forecast)來計算歷史銷售資料,推導出對未來的需求期望值,然後再將這 些預測結果結合起來,寫成自己真正的預測。. 2.1.3 存貨管理 傳統上存貨管理的目標是將存貨儘量降低增加存貨之財務報酬,同時卻仍然維持 良好的顧客服務水準。依 Michael Hugos[1]之存貨可分三種:. 1. 週期存貨:兩次訂同一種貨品之間隔期間裏,所必須保持足以應付需求之貨 品數量,經濟訂購量即為一例 2. 季節性存貨:當企業或供應鏈決定以固定產能來生產產品並將當期賣不掉之 產品累積起來時季節性存貨就會發生,假如未來的需求會超過現有之產能, 那當然作法是在需求低時多製造一些產品,以備未來高需求時出售。 3. 安全存貨:用來應付存在供應鏈中之不確定因素. 每家企業都會依據自己的成本結構來訂定最適之存貨水準,而任何企業或供應鏈 存貨管理作業也都是上述三種存貨之管理活動混合而成。限制理論將存貨視為一種緩 衝,目的為保護瓶頸增加有效產出。存貨短缺會造成顧客需求未被滿足,結果會造成 顧客延遲訂單,尋求替代品或是找其它供應商而致公司訂單流失。 傳統上業界一般使用之基本補貨系統大致可分為四類 [2]: 1. 使用經濟訂購量的再訂購點:在持續檢視下,當庫存量降低至再訂購點之下 時,訂購一固定的數量(經濟訂購量),安全庫存加補貨前置時間之預測需求 為再訂購點。 2. 使用最大存貨水準的再訂購點:在持續檢視下,當庫存量降低至再訂購點之下 時進行補貨,每次訂購數量不同,以將存貨水準補足到最大存貨水準為原則。 3. 使用最大存貨水準的定期檢視 : 定期檢視時點固定下進行補貨,補足到最大 11.
(20) 存貨水準。 4. 定期檢視再訂購點及最大存貨水準 : 定期檢視下,當庫存量降低至再訂購點 之下時進行補貨,補足到最大存貨水準。 上述四種補貨系統之優缺點比較彙整如表 2-2 :. 表 2-2 補貨系統之優缺點比較彙整表(資料來源: Edward [2]). 控制政策 優點 再訂購點 / 經濟訂購量 系統簡單、訂購量固定. 缺點 無法處理需求大幅變動. 再訂購點 / 最大存貨水準維持最大存貨水準的 再訂購點與EOQ 相同. 需過多計算除了A級品項均不 最普遍的控制政策,但其中 值 得投入心力進行復雜計算 可能會有多變的參數. 定期檢視 / 最大存貨水準需要協調相關品項的補貨 存貨持有成本比連續 、有定期機會修正最大 檢視系統來得高 存貨水準 定期檢視 / 再訂購點 整體所需的控制成本 需要過多計算不易暸解 / 最大存貨水準 最低. 說明 經濟訂購量計算可能不可靠. 適用於需求型態有固 定變化型態的品項 對於B、C 級品項的 計算成本過高. 2. 2 限制理論 限制理論是由高德瑞特博士所倡導,以科學方法之思維程序為基礎來解決組的經 營管理問題。認為每個企業體都是一個有機的系統並對組織做如下之基本假設:(李榮 貴/張盛鴻 [8]) 1. 一個組織最少有一個目標要達成。 2. 組織是由許多部門或單位組成彼此相互依賴(Interdependence)的系統。 3. 任何組織皆有限制,阻礙組織得到更好的目標績效的事情即為限制。 4. 莫非(Murphy)或不確定性行為(Uncertainty)因素是存在的。 限制理論是一種企業持續改善之方法,其強調的是一個系統的績效表現由該系統 中最弱之一環所決定,該最弱之一環則為系統之限制因子—瓶頸。只要找到最弱一環 並增加它的強度而非重量,就可強化整條鏈的強度(整個系統或組織的產出)。企業要 要加速組織目標的達成,要著重環之間的鏈結,也就是整條鏈的改善,而不是專注於. 12.
(21) 鏈條的每一環或每單位的改善。即組織要著重整體的最佳化(Global Optimum)取代傳 統上強調局部最佳化(Local Optimum)的績效評估。 限制理論從瓶頸管理出發,透過持續性地去除瓶頸與限制,達到全面營運的改善 與最大利益的追求,其最重要的貢獻在於指導企業如何集中利用系統中有限的資源, 把有限資源用中最重要的地方,解決整個系統的重要的資源限制因素,以求達到系統 最大的效益與目標。而企業的目標則是現在及未來均能持續的賺錢。如下是限制理論 提出產出觀管理之持續改善五個專注步驟 : 1. 指出系統限制:找出系統中最弱之一環。 2. 決定如何充份利用系統限制:使系統中最弱之一環得到最大產出。 3. 所有非限制充份支援步驟二所作的決策:要著重整體的最佳化取代傳統上強 調局部最佳化的績效評估 。 4. 打破系統限制:對限制做改善提升系統的限制。 5. 如果系統限制在步驟四被打破,回到步驟一。警告:不要讓惰性(典範)成為系 統限制。 限制理論很重要的觀念之一即在關鍵點導入適當保護措施的機制稱為緩衝管理 (Buffer Management),以做到對不確定因素做有效控管,以防莫非隨時來敲門,確保 預訂目標如期達成。 限制理論以其嚴謹思維程序,分別產闡述企業遭遇核心問題與並以嶄新觀念與穩 健的解決方案突破瓶頸,為企業帶來巨大利益,而獲不凡回響—如推行鼓-緩衝-繩 (Drum-Buffer-Rope; DBR) 解決方案於生產管理應用上、以專案緩衝與匯流緩衝之關 鍵鏈(Critical Chain)排程方法解決方案於專案管理應用上。以有效產出(Throughput; T= 整個系統透過銷售之賺錢速率)、投資(Investment;I=組織為了增加有效產出而 投資的錢—如廠房、機器設備、存貨)、營運費用(Operation Expense;OE=將投資轉 變成有效產出所需費用—如整備成本) 三項績效評估指標為羅盤,五個專注步驟為指 導方針應用在財務與績效評估。拉式配銷管理思維與IDD/TDD 績效衡量指標應用在 配銷與供應鏈管理。另外也包含以思維程序(Thinking Process)之三個重要思考步驟: 1. 要改變甚麼?(What to Change ? ) 13.
(22) 2. 要改變成甚麼?(What to Change to ?) 3. 要如何造成改變?(How to Cause the Change ?) 利用構建現況圖(Current Reality Tree ; CRT)找到核心衝途圖(Core Conflict),再以未 來圖(Future Reality Tree ; FRT)、負面分歧圖(Negative Branch Reservations ; NBR) 與條件圖(Prerequisite Tree ; PRT)、行動圖(Transition Tree ; TRT)交替運用解決方案應 用在市場行銷與業務管理,人的管理與策略與戰術管理上。總結限制理論架構如圖 2-4 所示:. 圖 2-4 限制理論架構圖 (資料來源: The World of Theory of Constraints [18]). 2.3 限制理論 Demand-Pull 緩衝管理模式 每企業經理人的目標都是要做好供應鏈管理,卻常落入又要馬兒好又要馬兒不吃 草或魚與熊掌不可兼得之典型供應鏈管理衝突。限制理論以衝突圖來闡釋—如圖2-5 所示:. 14.
(23) B. D. 讓成本(總庫存金 額)控制到最低. 備較小庫存. A. 做好管理工作 C. D’. 盡可能賣出最多的 貨品(降低缺貨次數). 備較大庫存. E :前置時間長. 供應商不可靠 需求變異大 預測不準. 圖2-5 典型供應鏈管理衝突. 為了想做好管理工作常為了讓成本控制到最低,故要備較小庫存,然而又想備較 大的庫存以儘可能賣出最多的貨品或是降低缺貨次數而陷入衝突。限制理論認為衝突 產生時,不是在兩個方案中尋找妥協方案,而是去尋找方案背後所提的假設,並設法 打破假設使得其中一個方案獲得解決,不至於產生衝突。檢視此衝突發現,要(C)盡 可能賣出最多的貨品或是降低缺貨次數,就必須(D’)備較大的庫存所做的假設是(E) 補貨時間長、供應商不可靠以及預測不準確。但是這假設是對的嗎?我們有沒有辦法 在不尋找更正確的預測系統,不投入更多的資本與不更換供應商之下,改善補貨時 間、供應商可靠度與預測準確度呢?資料來源:[12] 由上圖的衝突圖可以了解要打破此衝突圖,首先要改變的是前置時間長、供應商 不可靠,需求變異大以及預測不準確,茲說明如下: 1. 前置時間長:從供應鏈的庫存做考量,通常我們可以發現庫存都在供應鏈的 末端,也就是在零售商或批發商的手上,而零售商或批發商往往以補貨時間 的長短作為備庫存的依據,因此有效的縮短補貨時間也就可以減少供應鏈中 的存貨量。補貨時間是由訂單前置時間、生產前置時間以及運輸前置時間所. 15.
(24) 構成,在不增加成本的情況下,最有效縮短補貨時間的方法就是從訂單前置 時間與生產前置時間著手,目前造成補貨時間長的主要原因是因為許多的企 業都習慣以批量的方式做管理,以訂單前置時間而言,因為大批量可以獲得 較多的折扣以及不需花費太多的時間決定訂購數量,所以企業往往等存貨到 達訂購點時才發出訂單,以致於補貨時間拉長;另外在生產前置時間方面, 工廠為了追求作業效率及節省準備時間,在生產時也以批量生產方式進行, 這些都是造成補貨時間拉長的原因。 2. 供應商不可靠:對於供應商不可靠,企業可以選擇更換供應商或是對現有供 應商做訓練,以提升供應商的可靠度,但是這些方法對於企業有時可能緩不 濟急,所以企業面臨供應商不可靠時,往往用最直接的方式去解決,也就是 先備大量的庫存或建立更多供應商管道以因應。 3. 需求變異大:前後預測差異懸殊造成無所適從或說客戶因預期心理而累積需 求而延緩或提前下單情行,造成不同區間之需求差易很大,此會造成工廠端 對需求端之誤判而造成備太多之庫存積壓或太少庫存而缺貨趕工。若能充份 的分享上下游端之實既銷售或生產資訊能有效減少需求之變異。 4. 預測的不準確:預測系統只能預測趨勢,並不能精準預測實際的銷受需求。 當預測值高於實際需求時會造成庫存的現象,反之則會造成缺貨。而企業的 認知為缺貨比庫存嚴重,因此企業往往寧可備較高的庫存,以避免缺貨的發 生。但往往依預測備貨不是顧客不要的庫存過高,就是顧客要的確缺貨,要 解決上述的問題必須把過去的作業模式加以改變。. 典型的供應鏈與配銷系統以推式的作業模式—以平均需求當預測,且只為了盡力 做好猜測而已。為了方便省事或節省成本與減少生產換線時間,以批次作業處理訂單 或生產產品,使整個系統處於不穩定狀態。另以互信觀點來看,推式供應鏈與配銷管 理模式成員彼此不互信、保護自己、追求局部最佳。限制理論認為以拉式供應鏈與配 銷管理模式,將生產時間與補貨時間分離,降低批量與增大補貨頻率可以使補貨時間 縮短、且降低庫存、提高補貨可靠度。客戶與區域發貨倉庫與工廠倉庫間可彼此互信 16.
(25) 而減少以往不互信而造成之大量存貨。茲將限制理論拉式的運作模式茲說明如下: 1. TOC Demand –Pull 運作模式 TOC 打破過去公司將產品放在離消費者最近地方的觀念,將大部分的產品回 流至源頭也就是工廠內,而區域倉庫只需持有補貨前置時間內所要的需求 量,當客戶向區域倉庫下訂單的同時區域倉庫再向工廠訂購其所銷售的數 量,而工廠則以最迅速的方式將產品送至區域倉庫。方式說明如下: (1) 下游商儲存足夠庫存涵蓋可靠補貨期間內的需求,下游商用掉多少就對 上游(區域發貨中心/倉庫)訂購多少。 (2) 上游(區域發貨中心/倉庫)儲存足夠庫存涵蓋可靠補貨期間內的需求, 上游運送多少到下游商,就對上游(工廠倉庫)訂購多少。 (3) 工廠倉庫儲存足夠庫存涵蓋可靠補貨期間內的需求,工廠倉庫運送多少 到區域發貨中心/倉庫,就生產多少。「Demand-Pull」補貨方式如圖2-6 所示:. 工廠. 區域發貨中心/ 區域發貨中心/倉庫. 顧客. 拉的信息. Demand Pull 產品送至倉庫. Demand Pull 產品送至倉庫. 圖2-6 Demand-Pull 補貨模式 在限制理論 Demand-Pull 運作模式下,如何做好緩衝管理四要素,是此模式成功與 否的關鍵,此四要素即是:. 17.
(26) (1) 在何處是備庫存點 ? (2) 如何決定每個緩衝管理點的目標庫存量(緩衝存貨大小)? (3) 如何補貨?補貨的頻率與數量如何決定? (4) 如何監控緩衝?需求改變時如何調整目標庫存量?. 2.緩衝管理模式 TOC 在 "專案管理"提到之 Buffer 共管觀念,為何 Buffer 要共管,就是大家 都在抓 Buffer 而造成 Buffer 過多而讓一個專案原本可快速完成的,最後在怕金氏症與 學生症後群的作用下而造成專案之拖長甚至嚴重延誤。其實以此觀念應用在生管在回 覆訂單交期時有異取同工之妙。例:一個產品自生產到交貨共歷經 5 個生產站為 7 天, 每一個生產站均抓 10%之 Buffer,則總共要花(7 X 1.1) X 5 = 38.5 天(A),而若以 Buffer 共管之觀念,僅用單一生產站之 20%(二倍於先前單一生產站)為總 Buffer,則總 共要花 7 X 5 + 7 X 0.25 = 35 + 1.4 = 36.4 天(B)。很明顯 (B) 值小於 (A)值, 因為 Buffer 目的是保護莫非定律中所認為之不確定因子,但基本上 5 個生產站同時都 延誤之機率太小,故取單一生產站 2 倍之 Buffer 做為共管 Buffer 目標,實務上也證實, 實際生產週期亦接近上述方法(B)。同樣的, TOC 發展出 Demand-Pull Buffer Management 觀念時,提及愈往上游端做預測或備庫存會愈準—其實也是 Buffer 共管 觀念之延伸。就如同上游直接對終端市場(客戶)做需求預測,絕對會比自零售商給經 銷商再給代理商然後供應商,因為避掉了所謂的長鞭效應。 TOC 認為由於統計變異的計算上可知,個別計算的變異一定遠高於整體計算的 變異,因此若愈往上游的需求匯集處(Aggregation)作預測,則其準確率就遠高於散佈 各處銷售點所做預測的總和(如圖2-7所示),Fisher(1994)亦在其研究中印證了此點 [13]。. 18.
(27) 圖2-7 統計變異示意圖. TOC Demand-Pull 緩衝管理模式是一種監控工場及區域倉庫庫存量的方法。此 模式以補貨前置時間內之最大需求量視為其目標緩衝庫存量,當目標緩衝庫存量決定 之後將其分成三部份,分別為:(緩衝管理示意圖如圖2-8所示) (1) 忽略區(綠色線至黃色線) — 不採取行動並視狀況於必要時調降緩衝目標。 (2) 警告區(黃色線至紅色線) — 仍採取正常補貨行動並持續觀察監控。 (3) 趕工區(紅色線以下) — 採取緊急趕工以免緩衝庫存不夠造成缺貨並視狀 況於必要時調升緩衝目標。. G re e n B u ffe r. 600. Y e llo w b u ffe r. R e d b u ffe r. P h y s ic a l In v e n to ry. 500. 400. 300. 200. 100. 0 1. 24. 47. 70. 93 116 139 162 185 208 231 254 277 300 323 346 369 392 415 438 461 484 507 530 553 576 599 622 645 668 691 714. 圖2-8 緩衝管理示意圖 19.
(28) 當庫存水準一直在忽略區時就要適時的調降庫存量,相反的當庫存水準一直在趕 工區時要適時的調高庫存量,藉由緩衝管理的方法可以讓庫存維持在一定的水準下而 不發生缺貨的情形。 TOC 強調經反覆的調整即可得到符合需求情境的緩衝大小設定。 TOC 所主張 的緩衝管理也是降低營業費用的工具,若落在紅色管制區的次數太多,則必須增加緩 衝量以減少緊急訂單的行動,因為緊急訂單的交貨成本大於正常的交貨成本。. 3. TDD 與 IDD 績效衡量指標探討: 如何讓次系統做對的事,限制理論提出兩個績效評估指標確保「該做得很好的一 定做得很好」,同時不會造成「不該做得很好的一定做得很好」。 TOC 將過去配銷 常用的績效衡量指標如存貨週轉率、缺貨率等等,修正為有效產出天‧元(ThroughputDollar-Days ; TDD)與存貨天‧元(Inventory-Dollar-Days ; IDD),其基本定義如下: (1) 有效產出天‧元( TDD ):此指標主要是考慮到可靠度,其表示事情應該做的 很好但是卻沒有。所以當公司或部門對顧客訂單所承諾交貨日期無法達成 時便開使計算 TDD 值來顯示沒有達成之程度。計算方式:(有效產出之價 值) x (訂單延誤天數之總和)。當 TDD 值愈大表示訂單延遲過久,相對 會對企業造成潛在損失,企業可利用此指標,找出延遲交貨原因對症下藥, 以確保滿足顧客的要求。 目標:追求 TDD 值為零 (2) 存貨天‧元( IDD ) :此指標主要是考慮到效率,其表示事情不應該做的很 好但是卻做的很好。所以當企業或部門生產過多的存貨就是沒有效率,因 為這不僅造成潛在原物料的浪費,同時也使存貨成本提高。計算方式:(庫 存之價值) x (在倉庫停留天數之總和)。當 IDD 值愈大表示企業或部門 累積了愈多的庫存,造成庫存成本大幅增加,也可能暗示著其他物品可能 沒有原物料或產能進行生產而產生延遲交貨情形,利用此指標監控讓組織 有效效提生產的效率,同時減少不必要之存貨成本。 目標: 降低 IDD 值 20.
(29) 第三章個案研究與分析. W 公司是一專注於超大型積體電路設計、製造、行銷的高科技領域公司,秉持 著「正派經營、積極創新、滿足顧客、團隊合作」的理念,積極參與台灣科技島的建 設。目前產品類別概分為邏輯產品記憶體產品,前者可再細分為消費性語音、影像、 微控 IC、電腦與週邊相關 IC、網路通訊 IC 為主。後者為非揮發性記憶 IC, DRAM 與 Pseudo SRAM 記憶晶片為主. 2003 與 2004 年產品銷售比例概略如圖 3-1 所示:. 30%. 5%. Memory 70%. Logic. 52%. 2%. 網路通訊 IC 41% 電腦與週邊相關. IC 消費性 IC 其它. 圖 3-1 產品銷售比例. 3.1 W 公司現行作業模式 現行 Code 轉子體產品是屬於訂單式生產之消費性 IC,即收到客戶之訂單後才 啟動生產,此類產品內含客戶客製規格,啟動生產之後,只有客製規格下單客戶可使 用。W 公司 Code 轉子體產品一般用於消費性之電子產品如手機、電話、 遊戲機、 玩 具、禮物上之語音 IC 或電話之來電顯示 IC……等等,應用範圍很廣。圖 3-2 是 Code 轉子體產品客戶下單到交貨之作業流程之簡易圖示:. 21.
(30) Code 產品接單生產作業流程. 客戶提供 New Code. 供應商 市場研發 單位. 供應商 業務單位. 光罩製作. New Code 訂單. Repeat Code 訂單. 接單 轉子體. 視需要做部份確認. 晶圓投片 (訂購). 晶圓生產 (在途存貨). 母體庫存站 (在庫存貨). 晶圓產出. 晶粒銷售 出貨. 晶粒檢驗 入庫. 晶圓切割. 晶圓針測. 圖 3-2 Code 轉子體產品客戶下單到出貨之作業流程圖. 自晶圓投片到晶粒銷售之生產週期約略一個半月:為縮短生產週期,增加供貨之 彈性,研發人員充份應用供應鏈中"延遲差異化"之觀念,將 Family Product 晶圓先 行製造到一特定生產站停住,我們稱為晶圓母體庫存或 Wafer Bank,當客戶下單時即 可自母體庫存站之存貨往下一站繼續生產,生產週期約略可縮短 25 天以達快速交貨 滿足客戶需求。顧客服務水準之高低,悠關晶圓母體準備。通常備愈高之晶圓母體, 相對的擁有較高之顧客服務水準,但同時也隱含著高存貨成本之風險,最差狀況即市 場不再有需求時,會有呆滯存貨產生之風險。故如何備到恰到好處成為一重要課題。 W 公司對於如何建立晶圓母體之時機如下: 1. 依據銷售預測。 2. 依據公司政策於晶圓廠產能利用率較低時,建立較高水平之晶圓母體。. 依據銷售預測之作法說明如下: 1. 銷售與市場部人員會提供客戶未來半年銷售需求預測(以月為基準)。 2. 計算每週之平均晶圓投片淨需求(考慮扣除製程品與在製品之庫存狀況)。. 22.
(31) 3. 生管人員依據晶圓廠之生產週期 25 天(每 Layer 2.5 天)與晶圓投片流程 卡製作 3 天為生產前置時間內,提出晶圓投片需求工單給生產製造單位。 4. 每週定期給晶圓廠2次晶圓投片需求工單,可安排每天晶圓投片生產。 5. 若有緊急突發狀況,視情況需求另作安排處理。 6. 考慮安全庫存(15 天之預測銷售量)。. 3-2 現行作業與 Demand-Pull 緩衝模式於預測與實際銷售不同情境探討 在預測與實際銷售不同情境下,用簡單範例分述如下:(含 TOC Demand-Pull Model 之比較) 。表 3-1 之各欄位說明: 1. 敍述區間為 10 月~12 月,以一週為其日期單位。 2. 項次 1 為銷售需求預測值(將月銷售預測平均攤在每週)。 3. 項次 2 "BOH"欄位之值為期初庫存值。 晶圓母體(b):晶圓母體站之在庫庫存。 晶圓母體之前(a):晶圓投片尚未 run 至晶圓母體站之在途庫存。 Total WIP(c = a + b):晶圓母體在庫庫存加晶圓母體站前之在途庫存。 4. 項次 3 為銷售訂單(或說市場實際之潛在需求行為)。 5. 項次 4 為現行作業,依據平均銷售預測所需之晶圓投片。 6. 項次 4'為依 TOC Demand-Pull 方式所需之晶圓投片。 7. 項次 2'與項次 2 在日期欄下之數值,分別為依 TOC Demand-Pull 方式與現 行依預測生產方式下之在庫庫存與在途庫存值。 8. 項次 5 Buffer Inventory 為 TOC Demand-Pull 之緩衝庫存。 9. 項次 6 為生產週期內之累計需求用於 TOC Demand-Pull 建立緩衝庫存為參考 依據。 自晶圓投片到晶圓母體站之生產週期估 4 週(28 天) ,相關數值計算範例說明如 下: (本表模擬狀況未完全考慮晶圓生產每批 24 片之限制) (1) 晶圓母體(b)10/30 WK45 值 354“等於"晶圓母體(b)10/23 WK44 值 350 “加"項次 4 依據銷售預測所需之晶圓投片 10/2 WK41 值 144(生產 23.
(32) 週期為 4 週後入庫)“減"項次 3 銷售訂單 10/30 WK45 值 140。 (2) 晶圓母體之前(a)10/30 WK45 值 480“等於"晶圓母體之前(a)10/23 WK44 值 504“加"項次 4 依據銷售預測所需之晶圓投片 10/30 WK45 值 120 “減"項次 4 依據銷售預測所需之晶圓投片 10/2 WK41 值 144(生產 週期為 4 週後入庫) (3) 項次 4 晶圓投片“等於"第一個月總投片需求[式(1)+ 式(2)+ 式 (3)“減"BOH wip]“除以"4 週,再依晶圓最小批量 24 片微調平均每週 投片需求即“等於"[560+ 560+ 280“減"910]“除以"4“等於"123, 再將投片計劃概略微調成 WK41. 144 , WK42. 120 , WK43 120 , WK44. 120 WK41~WK44 累計銷售預測需求 560 ……………式(1) WK45~WK48 累計銷售預測需求 560 ……………式(2) 15 days 安全庫存“等於"式(2) X 0.5“等於"280 ……………式(3) (4) 晶圓母體之前(a)之 BOH 值 630,分 4 次 140, 140 ,140, 210 各別依次 分成 4 週入庫於 10/2. WK41, 10/9. WK42, 10/16 WK43, 10/23 WK44. 中。. 3.2.1 預測與實際銷售在不同情境下探討 情境(一) — 為實際銷售需求與平均銷售預測需求值完全一樣的情況下,所作現 行作業(簡稱甲方法)與 TOC Demand-Pull(簡稱乙方法)之分析,從表 3-1 之數字 上可知: 1. 甲、乙二方法無缺貨情形,也正如我們所預期一樣。 2. 甲方法之平均庫存 744 片較乙方法之 533 片多出 211 片,也正如我們所預期— 乙方法在維持相同之服務水準下,能有效降低存貨。. 24.
(33) 表 3-1 模擬依銷售預測與 Demand-Pull 方式下之晶圓補貨與庫存比較. 10/2 10/9 10/16 10/23 10/30 11/6 11/13 11/20 11/27 12/4 12/11 12/18 12/25 1/1 平均庫存 BOH WK41 WK42 WK43 WK44 WK45 WK46 WK47 WK48 WK49 WK50 WK51 WK52 WK53 WK01. 1.銷售需求預測 2.未測晶圓在製品存貨 Total WIP(c =a+b) 晶圓母體之前(a) 晶圓母體(b) 缺貨(d)--> 3.銷售訂單 4.晶圓投片 依據 Sale Forecast (e) 4'.晶圓投片. 140 140 140 910 914 894 874 630 634 614 594 280 280 280 280. 依據 TOC Demand-Pull (f). WIP大於 Buffer,有銷售而不需投片--WIP大於Buffer,額外晶圓投片---> 910 2'.未測晶圓在製品存貨 Total WIP(c' =a' +b' ) 晶圓母體之前(a') 630 晶圓母體(b') 280. 140 854 504 350. 140 834 480 354. 140 790 456 334. 140 746 432 314. 140 702 408 294. 140 658 384 274. 105 649 384 265. 105 640 384 256. 105 631 384 247. 105 622 384 238. 105 613 384 229. 744 459 285. 140 140 140 140 140 140 140 140 140 105 105 105 105 105 144 120 120 120 120 96 96 96 96 96 96 96 96 96 0 0 70 140 140 140 140 140 140 0 70 105 105 105 140 140 70 105 35 770 630 560 560 560 560 560 560 560 455 420 420 420 420 490 350 280 210 350 490 560 560 560 420 350 315 280 385 280 280 280 350 210 70 0 0 0 35 70 105 140 35. 533 400 133. 缺貨(d')-->. 5. Buffer Inventory 6.生產週期內之累計需求. 560 560 560 560 560 560 560 560 560 420 420 420 420 420 560 560 560 560 560 560 525 490 455 420 420 315 210 105. 情境(二) — 實際月銷售需求與預測值一樣,但假定實際銷售需求不平均的分佈 在每週,其結果為表 3-2:. 1. 甲方式在 11/6 WK46 週有缺貨 86 片情形發生,而乙方式沒有缺貨情形發生, 因為甲方式依平均銷售預測值投片,有其缺點即實際銷售值不同於預測值 時,並未能即時反應到晶圓投片計劃中,以致在某幾個區間內之總實際需求 已侵蝕預測值需求所建立之安全庫存而沒能即時反應導致有缺貨情形發生。 乙方式是依實際銷售多少而生產多少,故當某區間內需求增加時能即時反 應,而減少缺貨情形發生 2. 甲方式平均庫存 703 片,乙方式 529 片,故乙方式仍然較優. 25.
(34) 表 3-2 模擬依銷售預測與 Demand-Pull 方式下之晶圓補貨與庫存比較. 10/2 10/9 10/16 10/23 10/30 11/6 11/13 11/20 11/27 12/4 12/11 12/18 12/25 1/1 平均庫存 BOH WK41 WK42 WK43 WK44 WK45 WK46 WK47 WK48 WK49 WK50 WK51 WK52 WK53 WK01. 1.銷售需求預測 2.未測晶圓在製品存貨 Total WIP(c =a+b) 晶圓母體之前(a) 晶圓母體(b) 缺貨(d)--> 3.銷售訂單 4.晶圓投片 依據 Sale Forecast (e) 4'.晶圓投片. 140 910 630 280. 140 140 140 140 140 140 140 140 140 914 614 734 854 694 480 600 720 840 634 614 594 504 480 480 480 480 480 280 0 140 350 214 0 120 240 360 (86) 140 420 0 0 280 420 0 0 0 144 120 120 120 120 120 120 120 120. 依據 TOC Demand-Pull (f) 0 WIP大於 Buffer,有銷售而不需投片---> 140 WIP大於Buffer,額外晶圓投片---> 910 770 2'.未測晶圓在製品存貨 Total WIP(c' =a' +b' ) 晶圓母體之前(a') 630 490 晶圓母體(b') 280 280. 370 50. 0. 0 260 140 20 280. 0. 0. 105 597 432 165. 105 669 384 285. 105 741 336 405. 105 708 288 420. 105 675 288 387. 703 462 240. 315 0 0 105 105 72 72 72 72 72. 0 315. 0. 0 105 105. 720 720 720 700 420 420 420 420 420 420 420 420 420 720 580 370 630 400 400 400 140 315 315 315 420 210 0 140 350 70 20 20 20 280 105 105 105 0 210. 529 408 122. 缺貨(d')-->. 5. Buffer Inventory 6.生產週期內之累計需求. 700 700 700 700 700 420 420 420 420 420 420 420 420 420 560 700 700 700 700 420 315 315 315 420 210 210 210 105. 情境(三) — 實際月銷售訂單大於銷售預測值而能掌握到需求潛在性增加,但銷 售預測卻未即時更正時如表 3-3: 1. 從表 3-3 中得知甲方式同樣有缺貨情形發生,而且為連續缺貨,而乙方式亦 有小幅缺貨情形。 2. 在平均存貨方面,甲方式 655 片仍高於乙方式之 612 片,但差距已大符縮小, 且不明顯。乙方在情境(三)平均庫存 612 明顯高於情境(一)平均庫存 533 片 與情境(二)平均庫存 529 片,主要因其緩衝庫存目標因應需求增加而提高之 故。 3. 甲方式在情境(三)平均庫存 655 片不但未高於情境(一)744 片與情境(二)703 片,反而下降,主要因為晶圓生產依據預測,若預測不準而未即時更新,即 有可能維持相同水準之投片計劃,但在實際銷售需求增加情形,存貨已銷售 但未有效增加投料生產,自然存貨水位會降低,但因未控制得宜,即出現缺 貨情形。 或許我們會認為只要甲方式能即時修正預測能解決問題,這是當然的且從下 表 3-4 得知缺貨情形明顯改善,但 11/6 WK46 仍有小幅度缺貨且平均庫存 771 片較修正前提高了且還是高於乙方式 667 片。 26.
(35) 表 3-3 模擬依銷售預測與 Demand-Pull 方式下之晶圓補貨與庫存比較. 10/2 10/9 10/16 10/23 10/30 11/6 11/13 11/20 11/27 12/4 12/11 12/18 12/25 1/1 平均庫存 BOH WK41 WK42 WK43 WK44 WK45 WK46 WK47 WK48 WK49 WK50 WK51 WK52 WK53 WK01. 1.銷售需求預測 2.未測晶圓在製品存貨 Total WIP(c =a+b) 晶圓母體之前(a) 晶圓母體(b) 缺貨(d)--> 3.銷售訂單 4.晶圓投片 依據 Sale Forecast (e). 140 910 630 280. 140 914 634 280. 140 140 140 140 644 484 532 584 504 480 532 584 140 4 0 0 (16) (20) 140 210 210 210 280 140 140 144 120 120 120 120 172 172. 4'.晶圓投片. 依據 TOC Demand-Pull (f) 140 WIP大於 Buffer,有銷售而不需投片---> WIP大於Buffer,額外晶圓投片---> 910 910 2'.未測晶圓在製品存貨 Total WIP(c' =a' +b' ) 晶圓母體之前(a') 630 630 晶圓母體(b') 280 280. 140 824 614 210. 140 734 594 140. 140 612 612 0 (20) 140 148. 140 105 640 659 640 592 0 67 (20) 140 105 148 124. 105 650 516 134. 105 641 464 177. 105 632 412 220. 105 623 384 239. 655 540 115. 105 105 105 105 96 96 96 96. 210 140 210 140 140 0 105 65 105 75 105 105 105 70 140 140 35 80 30 910 840 840 700 700 560 525 450 450 420 420 420 420 700 700 700 700 630 490 385 310 275 350 350 390 390 210 140 140 0 70 70 140 140 175 70 70 30 30. 612 500 112. 缺貨(d')-->. 5. Buffer Inventory. 910 910 840 840 700 700 525 525 450 450 420 420 420 420 770 910 840 770 700 560 525 490 455 420 420 315 210 105. 6.生產週期內之累計需求. 表 3-4 模擬依銷售預測與 Demand-Pull 方式下之晶圓補貨與庫存比較. 10/2 10/9 10/16 10/23 10/30 11/6 11/13 11/20 11/27 12/4 12/11 12/18 12/25 1/1 平均庫存 BOH WK41WK42WK43WK44WK45WK46WK47WK48WK49WK50WK51WK52WK53WK01. 1.銷售需求預測 2.未測晶圓在製品存貨 Total WIP(c =a+b) 晶圓母體之前(a) 晶圓母體(b) 缺貨(d)--> 3.銷售訂單 4.晶圓投片 依據 Sale Forecast (e). 140 910 630 280. 140 914 634 280. 210 210 280 140 140 828 748 824 780 736 688 744 824 696 592 140 4 0 84 144 (16) 140 210 210 210 280 140 140 140 144 120 224 200 200 200 96 96. 4'.晶圓投片. 依據 TOC Demand-Pull (f) 140 WIP大於 Buffer,有銷售而不需投片---> WIP大於Buffer,額外晶圓投片---> 910 910 2'.未測晶圓在製品存貨 Total WIP(c' =a' +b' ) 晶圓母體之前(a') 630 630 晶圓母體(b') 280 280. 140 824 614 210. 210 838 698 140. 140 692 488 204. 105 788 384 404. 105 755 360 395. 105 722 336 386. 105 689 312 377. 105 656 288 368. 771 547 224. 140 105 105 105 105 105 96 96 72 72 72 72. 210 140 210 140 140 0 105 65 105 75 105 105 105 70 140 140 35 80 30 910 840 840 700 700 560 525 450 450 420 420 420 420 700 700 700 700 630 490 385 310 275 350 350 390 390 210 140 140 0 70 70 140 140 175 70 70 30 30. 612 500 112. 缺貨(d')-->. 5. Buffer Inventory 6.生產週期內之累計需求. 910 910 840 840 700 700 525 525 450 450 420 420 420 420 770 910 840 770 700 560 525 490 455 420 420 315 210 105. 情境(四) — 實際月銷售訂單大於銷售預測值,而於初期未能掌握需求潛在趨勢 時: 1. 從表 3-5 中得知甲方式同樣有缺貨情形發生,而且為連續 4 週缺貨,而乙方 27.
(36) 式也有嚴重缺貨,但適時調高換緩衝後缺貨兩週即停止情形。 2. 基本上乙方式於 10/16 WK43 時母體庫存已低於緩衝的三分之一即紅色趕 工區,若能確時落時趕工,相信嚴重缺貨情形能有效改善。 3. 由此觀之,在此情境下對銷售趨勢看錯以至緩衝值設錯會有不良後果,但有 警告機制適時提醒。 4. 從此情境(四)中可學到可另建一機制控管緩衝目標— 即三分之一補貨期間 內之實際累計需求若大於紅色緩衝線時,應考慮是否該適時的調高緩衝目標。. 表 3-5 模擬依銷售預測與 Demand-Pull 方式下之晶圓補貨與庫存比較. 10/2 10/9 10/16 10/23 10/30 11/6 11/13 11/20 11/27 12/4 12/11 12/18 12/25 1/1 平均庫存 BOH WK41 WK42 WK43 WK44 WK45 WK46 WK47 WK48 WK49 WK50 WK51 WK52 WK53 WK01. 1.銷售需求預測 2.未測晶圓在製品存貨 Total WIP(c =a+b) 晶圓母體之前(a) 晶圓母體(b) 缺貨(d)--> 3.銷售訂單 4.晶圓投片 依據 Sale Forecast (e). 140 910 630 280. 140 914 634 280. 140 140 140 140 644 484 532 584 504 480 532 584 140 4 0 0 (16) (20) 140 210 210 210 280 140 140 144 120 120 120 120 172 172. 4'.晶圓投片. 依據 TOC Demand-Pull (f) 0 WIP大於 Buffer,有銷售而不需投片--- 140 WIP大於Buffer,額外晶圓投片---> 910 770 2'.未測晶圓在製品存貨 Total WIP(c' =a' +b' ) 晶圓母體之前(a') 630 490 晶圓母體(b') 280 280 缺貨(d')-->. 5. Buffer Inventory 6.生產週期內之累計需求. 140 824 614 210. 140 734 594 140. 0 490 210 280 560 840 350 700 210 140. 210. 140 612 612 0 (20) 140 148. 140 105 640 631 640 564 0 67 (20) 140 105 148 96. 105 622 488 134. 105 613 436 177. 105 604 384 220. 105 595 384 211. 645 532 113. 105 105 105 105 96 96 96 96. 0 0 0 105 65 105 75 105 105 105 280 140 140 35 80 30. 840 700 700 560 700 700 700 210 140 0 0 350 (140) (140) 560 560 840 840 700 700 525 770 910 840 770 700 560 525. 525 450 450 420 420 420 420 105 170 275 350 350 390 390 420 280 175 70 70 30 30. 577 420 157. 525 450 450 420 420 420 420 490 455 420 420 315 210 105. 情境(五) —為當實際銷售低於預測,即便不用表列即可推知如下之結果: 1. 甲方式之庫存水準較乙方式來得高,因晶圓投片依據預測值之故,且甲式庫 存水準較前 4 種情境高。但是乙方式之庫存水準卻低於前 4 種情境,因 TOC 強調的是“賣多少補多少"。 2. 兩者不會有缺貨情形。. 28.
(37) 表 3-6 模擬依銷售預測與 Demand-Pull 方式下之晶圓補貨與庫存比較. 10/2 10/9 10/16 10/23 10/30 11/6 11/13 11/20 11/27 12/4 12/11 12/18 12/25 1/1 平均庫存 BOH WK41 WK42 WK43 WK44 WK45 WK46 WK47 WK48 WK49 WK50 WK51 WK52 WK53 WK01. 1.銷售需求預測 2.未測晶圓在製品存貨 Total WIP(c =a+b) 晶圓母體之前(a) 晶圓母體(b) 缺貨(d)--> 3.銷售訂單 4.晶圓投片 依據 Sale Forecast (e). 140 910 630 280. 140 954 634 320. 140 954 614 340. 140 974 594 380. 140 1024 504 520. 140 1074 480 594. 140 982 408 574. 140 890 336 554. 140 798 264 534. 140 682 168 514. 105 673 216 457. 105 664 264 400. 105 655 312 343. 105 646 384 262. 105 625 372 253. 828 396 432. 100 120 100 70 70 140 140 140 140 105 105 105 105 105 144 120 120 120 120 48 48 48 24 96 96 96 96 84. 4'.晶圓投片. 依據 TOC Demand-Pull (f) 0 WIP大於 Buffer,有銷售而不需投片--- 100 WIP大於Buffer,額外晶圓投片---> 910 810 2'.未測晶圓在製品存貨 Total WIP(c' =a' +b' ) 晶圓母體之前(a') 630 490 晶圓母體(b') 280 320. 0 0 40 70 140 105 105 100 105 75 105 105 105 120 100 30 35 35 40 30 690 590 560 560 560 525 490 450 450 420 420 420 420 350 210 40 110 250 355 420 450 415 385 385 390 390 340 380 520 450 310 170 70 0 35 35 35 30 30. 526 331 195. 缺貨(d')-->. 5. Buffer Inventory 6.生產週期內之累計需求. 560 560 560 560 560 560 525 525 450 450 420 420 420 420 390 360 380 420 490 560 525 490 455 420 420 315 210 105. 茲將尚述情靜討論彙整如表 3-7 : 表 3-7 情境討論彙整表 情境. 描述. 甲方式 (單位:片晶圓 乙方式(單位:片晶圓) 結論 平均總庫存 缺貨 平均總庫存 缺貨. 實際銷售需求與平均銷售預測 需求值完全一樣的情況下. 744. 0. 533. 0 乙方式為佳. 實際月銷售需求與預測值一樣 (二) ,但假定實際銷售需求不平均 的分佈在每週. 703. 86. 529. 0 乙方式為佳. 實際月銷售訂單大於銷售預測 (三) 值而能掌握到需求潛在性增加 ,但銷售預測卻未即時更正時. 655. 76. 612. 0 乙方式為佳. 情境(三) 之銷售預測於一週後 做更正. 771. 16. 612. 0 乙方式為佳. 實際月銷售訂單大於銷售預測 (四) 值,而於初期未能掌握需求潛 在趨勢時. 645. 76. 577. (五) 為當實際銷售低於預測. 645. 0. 577. (一). (三)'. 29. 280. 乙方式為劣, 但緩衝監控系 統之趕工機制 ,可降低缺貨. 0 乙方式為佳.
(38) 3.2.2 緩衝庫存調整作業 TOC Demend-pull 緩衝庫存生產方式是應用了一種簡單而可行之邏輯觀念,即" 有需求才生產",需求多少生產多少,沒有需求則不生產,也就是沒事不要找事做, 有事趕緊做。另一觀念即"緩衝"即"保護"之觀念,讓緩衝庫存能保護瓶頸不受不 確定因素之干擾,以達最大產出。 以 W 公司為例,回應 Demand-Pull 緩衝庫存生產之四個基本要素分述如下: 1. 在晶圓母體站備庫存。 2. 依據顧客服務水準高低決定,原則上以生產週期內之最大需求作為緩衝庫存 值。但因公司產能有限,不同時期產品為了因應不同市場變化會有不同配額 考量,有了此配額再依產品事業中心之不同策略考量分配到各產品型號上或 以預建庫存方式調節緩衝庫存目標。 3. 現行作業是每週給生產工單 2 次,可每天生產,每批生產最小批量為 24 片晶 圓,若有特殊狀況再視情況調整,可依 TOC 不累積需求觀念與縮短前置時間 而改變成,每天給工單,但給的是第三天下線之工單。 4. 緩衝庫存高低之調整是此方法生產之一關鍵因子。. 調高緩衝庫存之時機 : 1. 當需求持續強勁,造成庫存低處於紅色趕工區間,而非生產因延遲造成的時 候。 2. 季節性需求明顯之產品,預計旺季需求到來前之一個以上生產週期以上。 3. 當生產週期變長時。. 調降緩衝庫存之時機 : 1. 當需求趨緩,庫存長時間處於綠色忽略區時段。 2. 季節性需求明顯之產品,預計淡季來臨前之一個以上生產週期以上。 3. 當產品面臨生命週期結束時。 4. 當生產週期縮短時。 30.
(39) 在現行產能有限情況下,如何建立緩衝目標之參考做法如下: 1. 可將一年可分成 4 個或適當個區間。 2. 將每個產品在不同區間內生產週期之最大需求量列出在一試算表中並在區間 下做小計。 3. 將此需求量視為要建立之緩衝庫存。 4. 比較緩衝庫存目標是否在可供給之產能範圍內。 5. 調節個別產品緩衝庫存目標值使其可在產能之內,如表 3-8 。 6. 調節標準產品使可供給產能滿足緩衝庫存目標值,如表 3-9 。 7. 依需求與產能滿足狀況採取適當因應對策。. 表 3-8 調節緩衝庫存作業 Case1--調節緩衝庫存 產品 區間 1 調節前 A 300 緩衝庫存 B 200 C 目標 800 D 900 緩衝庫存 小計 2200 可供給產能 2300. 區間 2 600 500 500 400 2000 2200. 區間 3 800 800 400 300 2300 2000. 區間 4 500 400 700 400 2000 2200. 區間 5 400 300 300 200 1200 1800. 區間 6 700 400 600 500 2200 1800. 小計 3300 2600 3300 2700 11900 12300. 產品 調節後 A 緩衝庫存 B C 目標 D 緩衝庫存 小計 可供給產能. 區間 1 300 300 800 900 2300 2300. 區間 2 600 700 500 400 2200 2200. 區間 3 800 500 400 300 2000 2000. 區間 4 500 400 700 400 2000 2200. 區間 5 800 300 300 200 1600 1800. 區間 6 300 400 600 500 1800 1800. 小計 3300 2600 3300 2700 11900 12300. 產品 調節後 A 緩衝庫存 B C 差異 D 緩衝庫存 小計. 區間 1 0 100 0 0 100. 區間 2 0 200 0 0 200. 區間 3 0 -300 0 0 -300. 區間 4 0 0 0 0 0. 區間 5 400 0 0 0 400. 區間 6 -400 0 0 0 -400. 小計 0 0 0 0 0. 31.
(40) 表 3-9 調節緩衝庫存作業. Case2---調節可供給產能 產品 區間 1 區間 2 區間 3 區間 4 區間 5 區間 6 A 300 600 800 500 400 700 B 200 500 800 400 300 400 C 800 500 400 700 300 600 D 900 400 300 400 200 500 緩衝庫存 小計 2200 2000 2300 2000 1200 2200 可供給產能(初始) 2300 2200 2000 2200 1800 1800 可供給產能(調節後) 2200 2000 2300 2200 1400 2200. 小計 3300 2600 3300 2700 11900 12300 12300. 產品 區間 1 區間 2 區間 3 區間 4 區間 5 區間 6 E (被調節之標準產品) 100 200 -300 400 -400. 小計 0. 有了上述之緩衝庫存目標決定後(若遇產能瓶頸,可利用 TOC 法決定產品組 合),各個產品以此做為 TOC Demand-Pull 生產依據並適當時機做調整。基本上 TOC Demend-Pull 緩衝庫存生產為一動態監控機制,是隨時隨著市場脈動,貼近市場之一 種生產方式,而其緩衝庫存管制圖示法亦是一個生產與市場銷售人員溝通之共通平 台。只要市場銷售人員能告訴工廠未來在生產週期內之最大需求,則工廠保証讓市場 不缺貨之互信基礎下,就能讓此方式功效發揮到最大,如前述圖 2-2 可知,相同之顧 客服務水準卻以較少之庫存水準達成或相同之庫存水準確有較高之顧客服務水準。同 時工廠端也要改變作法,產品落入紅色趕工區即為急件,想辦法減少庫存水準停在趕 工區。而市場銷售人員則想辦法針對庫存落於綠色忽略區或以上者努力向顧客催單。 相關單位行為與觀念要做改變,工廠急件趕工之依據是以庫存值是否落在紅色趕工區 而急件趕工,不再是依長官或銷售人員說急件趕工。好處是有明確共同之語言,而市 場銷售人員要確實掌握市場與產品銷售需求趨勢狀況,告知未來生產週期內客戶之最 大銷售需求,(當然工廠生產週期之變化要即時告知市場銷售人員以利計算緩衝庫存 目標)以利能更正確的建立緩衝庫存,不再需要去猜測遙不可及之未來六個月之每月 銷售預測。 然而當所建立之緩衝庫存水準不能滿足市場需求時,亦要即時告知客戶讓其有所 因應以降低不必要之損失。拜科技之賜, IT 人員之支援建立緩衝庫存監控管制圖示 32.
(41) 表與相關管制資訊程式化已非難事,此更能強化 TOC 之應用並達成其預期之效果。 TOC 方法也將可促使銷售人員與客戶聯絡,以簡單之方法了解其需求趨勢,而 非苦苦追求精準之銷售預測,進而拉近與客戶之距離,加上生產能即時滿足客戶需 求,相信此舉能建立起與客戶長期友好關係,進而有利業務推廣與市場之擴大而增加 公司收益,藉由將生產資訊公開給市場銷售人員亦有助於工廠人員努力表現,力求生 產交貨順暢,同時庫存過高時亦會給市場銷售人員壓力,努力接單並同達成滿足市場 需求降低庫存使公司朝向增加獲利之共同目標前進。. 3.2.3 產品舉例說明 TOC Demand-Pull 方式 W 公司現行作業實際情形類似上述之情境(二)與(三),即庫存相對低,但有缺 貨情形發生,茲舉一產品 AA5794 以 TOC Demand-Pull 方式作做比較,在讓缺貨情 行變零之情境下列(100% 顧客服務水準),在庫庫存水準約略增加約四分之一,說明 如下表: 1. 現行作業 — IDD 值 $NT 2.48M,TDD 值 $NT 38.4M 2. 模擬 TOC Demand-Pull (1) — IDD 值 $NT 3.32M,TDD 值 $NT 0M. 圖 3-3 為產品型號 AA5794 之緩衝庫存圖表: 1. 日期區間為 1/1/2003~12/31/2004 Q4 為旺季,Q2 為淡季,Buffer 值以每季 前後一個月區間之補貨週期內之最大銷售需求值。 2. 若遇特定事件,則以不影響緩衝之設定下,可酌情與以扣除。 3. 2003/Q1,Q2,Q3,Q4 緩衝庫存依序設為 413, 612, 1306, 1377 4. 2004/Q1,Q2,Q3,Q4 緩衝庫存依序設為 1377, 657, 511, 464. 33.
(42) Green Zone. 1600. Yellow Zone. Red Zone. On hand. 1400. 1200. 1000. 800. 600. 400. 200. 0 1. 24 47 70 93 116 139 162 185 208 231 254 277 300 323 346 369 392 415 438 461 484 507 530 553 576 599 622 645 668 691 714. 圖 3-3. 產品 AA5794 緩衝庫存圖. 另從現行作業下之訂單情形,我們不難發現需求有累積下單情形,也就是我們猜 測客戶並非依其工廠實際生產需求下單,這種情形表示供應鏈並未建立在互信基礎 下,也因此容易造成供應端之誤判而提高緩衝庫存值,會有建立過高之庫存以求滿足 累計之極端值。我們若作個假設,客戶端工廠之實際生產平順,每三天取貨一次,則 原客戶需求重新予以平均化、理想化後,我們可發現庫存水準相對低很多,也不需較 高之緩衝之庫存以保護不確定因素,說明如下:. 模擬 TOC Demand-Pull (2)---- IDD 值 $NT 1.89M,TDD 值 $ NT 0 M 較 TOC Demand-Pull (1) IDD 值 $NT 3.32M 少 $NT 1.43 M 也低於現行作業之 IDD 值 $ NT 2.48M。. 34.
(43) 圖 3-4 為修正之產品型號 AA5794 之緩衝庫存圖表 : 1. 日期區間為 1/1/2003 ~ 12/31/2004 2. Q4 為旺季,Q2 為淡季 3. 2003/Q1,Q2,Q3,Q4 緩衝庫存依序設為 238, 480, 1180, 1180 4. 2004/Q1,Q2,Q3,Q4 緩衝庫存依序設為 880, 536, 420, 416. Green Zone. 1400. Yellow Zone. Red Zone. On hand. 1200. 1000. 800. 600. 400. 200. 0 1. 24 47 70 93 116 139 162 185 208 231 254 277 300 323 346 369 392 415 438 461 484 507 530 553 576 599 622 645 668 691 714. 圖 3-4 產品 AA5794 修正銷售需求後緩衝庫存圖. 3.3 個案研究分析資料彙整 經過上述之各種情境探討後,模擬所有產品以 TOC Demand-Pull 緩衝庫存生產 與現行實際作業之彙總資料說明如下: 表 3-10 為現行實際作業與模擬 TOC Demand-Pull 緩衝庫存生產值對在庫庫存之 IDD 與 TDD 值之比較。從資料顯示,個別產品品項之 IDD 值各有高低之差異,但整 體而言 TOC Demand-Pull 之 IDD $ NT 114.2M,優於現行作業之 IDD $NT 133.9M。. 35.
數據


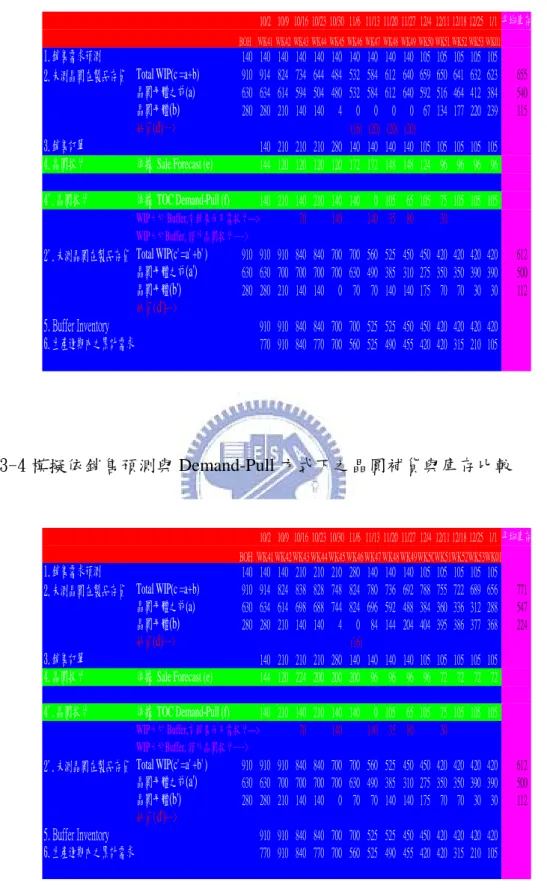

+5
相關文件
�您�� BIOS 設定完成後,請選擇本項目以�認所有設定值存入 CMOS 記憶體內。按下 <Enter> 鍵後�出現一個詢問視窗,選擇 [Ok],�設定值存 Ok],�設定值存 ],�設定值存 入
黑木耳 (Auricularia polytricha) 是台灣普遍的食用 菌之一,為一種低熱量的食品,亦是一種富含食用纖維及
以 2011 年經濟部統計處針對各製造業所做的調查,糕餅業所屬 的其他烘焙麵食品之生產值占食品製造業中 3.68%,在 33 項品向中排
油壓開關之動作原理是(A)油壓 油壓與低壓之和 油壓與低 壓之差 高壓與低壓之差 低於設定值時,
微陣列玻片資料庫 (The Microarray Database,以下簡稱 TMD) 為本研究嘗 試建置的一套提供存取、分析微陣列玻片 (Microarray)
介面最佳化之資料探勘模組是利用 Apriori 演算法探勘出操作者操作介面之 關聯式法則,而後以法則的型態儲存於介面最佳化知識庫中。當有
由於醫療業導入 ISO 9000 品保系統的「資歷」相當資淺,僅有 三年多的年資 11 ,因此,對於 ISO 9000 品保系統應用於醫療業之相關 研究實在少之又少,本研究嘗試以通過
Hogg (1982), “A State-of-the-art Survey of Dispatching Rules for Manufacturing Job Shop Operation,” International Journal of Production Research, Vol.. Gardiner (1997), “A