以六標準差改善流程提升手機組裝線生產力之研究 - 政大學術集成
90
0
0
全文
(2) 中文摘要 摩托羅拉於 1987 年開始推動六標準差改善計畫,但當時並未受到企業特別 的重視,直到奇異公司於 1995 年重新啟動六標準差品質計畫,才使得這套成效 卓著的改善工具受到企業的肯定。早在 1991 年,國內便有學者著書將六標準差 知識體系介紹給國人(林秀雄,1993) ,到直到 1999 年以後,才開始有長榮航太、 金寶電子、英業達、漢翔航空等國內企業陸續推行六標準差,並從中受益。如今, 六標準差已是最高品質的代名詞,它不只是一系列的改善活動,更是企業追求卓 越的經營模式。. 治 政 個案研究的方式,將國內某通訊產品業者首次應用六標準差改善流程(DMAIC) 大 立 執行手機生產線改善的推動歷程,進行深入的報導,研究重點在於個案公司如何. 本研究有鑒於六標準差品質改善手法對於國內企業競爭力助益匪淺,故採取. ‧ 國. 學. 運用六標準差改善流程之界定、衡量、分析、改善、控制五個階段,提升生產線 之生產力,減少浪費,最終滿足顧客的需求。. ‧. 個案公司乃運用六標準差改善流程,找出影響生產力之關鍵影響因素,包括. sit. y. Nat. 瓶頸工站工時、工時變異性程度、生產線平衡率,並結合生產線改善與平衡的手. io. er. 法,發展出具體可行之解決方案,達成專案初期所設定的目標,最終並發展有效 的控制方式,使專案效益能夠持續。. n. al. Ch. i n U. v. 另外,本研究試圖以系統化的歸納方式,整理出個案公司的成功經驗與遭遇. engchi. 問題,並說明個案公司所提之解決方案,希冀本論文之付梓對於有志推動六標準 供之企業,能夠有借鏡學習之參考作用。. 關鍵字:六標準差、改善流程、手機製造、生產線平衡. II.
(3) 目次. 中文摘要 ....................................................... II 目次 ...........................................................III 表次 ........................................................... IV 圖次 ............................................................ 1 第壹章 緒論...................................................... 2 第一節 第二節 第三節 第四節. 研究背景與動機 .............................................2 研究目的 ...................................................3 研究流程 ...................................................4 論文架構 ...................................................4. 政 治 大. 第貳章 文獻探討 .................................................. 5. 立. ‧ 國. 學. 第一節 流程管理 ...................................................5 第二節 六標準差品質改善手法 ......................................14 第三節 生產力 ....................................................22 第參章 研究方法 ................................................. 25. ‧. 界定階段 ..................................................25 衡量階段 ..................................................27 分析階段 ..................................................29 改善階段 ..................................................30 控制階段 ..................................................31. er. io. sit. y. Nat. 第一節 第二節 第三節 第四節 第五節. al. n. v i n C h......................................33 第一節 全球手機市場發展現況 U i e h n c g 第二節 個案公司簡介 ..............................................37. 第肆章 個案研究 ................................................. 33. 第三節 個案公司 G 手機生產線改善前之流程說明 ......................38 第四節 六標準差改善專案推動步驟 ..................................42 第伍章 結論與建議 ............................................... 79 第一節 研究結論 ..................................................79 第二節 研究建議 ..................................................80 第三節 未來研究方向 ..............................................82 參考文獻 ....................................................... 83. III.
(4) 表次 表 2-1. 企業流程定義彙整............................................6. 表 2-2. 流程再造之取向觀點..........................................8. 表 2-3. 流程圖相關性分析...........................................11. 表 2-4. 六標準差之發展階段.........................................15. 表 2-5. 六標準差三大管理策略.......................................18. 表 4-1. 2004 年全球手機銷售數量統計表 ..............................34. 表 4-2. 全球 ODM 廠與 CEM 廠之比較...................................36. 表 4-3. 全球 ODM 廠與 CEM 廠之優劣勢分析.............................36. 表 4-6. 衡量標的之單元工時數據(衡量階段).........................50. 表 4-7. 衡量系統分析數據...........................................51. 表 4-8. 衡量系統分析結果...........................................52. 表 4-9. 液晶面板壓焊工站之單元工時數據(分析階段之假設檢定).......57. ‧. ‧ 國. y. Nat. sit. 表 4-4. 學. 表 4-5. 治 政 G手機生產線改善前工時數據.................................45 大 立 專案團隊章程...............................................48. io. er. 表 4-10 液晶面板焊接工站之單元工時數據(分析階段之假設檢定).......58 表 4-11 擴音器與麥克風焊接工站之單元工時數據(分析階段之方案驗証).65. n. al. Ch. i n U. v. 表 4-12 遮蔽蓋組裝工站之單元工時數據(分析階段之方案驗証).........69. engchi. 表 4-13 面鏡與上機殼壓合工站之單元工時數據(分析階段之方案驗証)...70 表 4-14 電流與充電測試工站之單元工時數據(分析階段之方案驗証).....72 表 4-15 G手機生產線預期工時數據...................................73 表 4-16 G手機生產線之整合性改善方案...............................74 表 4-17 在製品堆貨記錄表...........................................76 表 4-18 定時工時量測表.............................................76 表 4-19 六標準差改善流程重要準則...................................77 表 4-20 直接效益之改善分析表.......................................78 表 5-1 分析輔助工具對照表 ..........................................81. IV.
(5) 圖次 圖 2-1. 企業流程、工作流程及要素說明................................6. 圖 2-2. 方法研究之分析方法.........................................12. 圖 3-1. 定義階段步驟流程圖.........................................25. 圖 3-2. 衡量階段步驟流程圖.........................................28. 圖 3-3. 分析階段步驟流程圖.........................................29. 圖 3-4. 改善階段步驟流程圖.........................................30. 圖 3-5. 控制階段步驟流程圖.........................................32. 圖 4-1. G手機生產流程.............................................39. 圖 4-4. 專案時程表.................................................47. 圖 4-5. 液晶面板壓焊工站之製程能力分析圖(衡量階段)...............54. 圖 4-6. 液晶面板壓焊工站佈置.......................................55. 圖 4-7. 液晶面板壓焊工站作業流程圖.................................55. 圖 4-8. 液晶面板壓焊工站之人機圖...................................56. 圖 4-9. 液晶面板壓焊工站之製程能力分析圖(分析階段之假設檢定).....58. ‧. ‧ 國. io. sit. y. Nat. n. al. er. 圖 4-2. 學. 圖 4-3. 治 政 G手機生產線改善專案之 SIPOC 圖.............................43 大 立 G手機之改善前生產線平衡圖.................................46. Ch. i n U. v. 圖 4-10 液晶面板壓焊工站之製程能力分析圖(分析階段之方案驗証).....59. engchi. 圖 4-11 擴音器焊接工站之製程能力分析(衡量階段)...................60 圖 4-12 擴音器焊接工站佈置.........................................61 圖 4-13 擴音器焊接工站作業流程圖...................................62 圖 4-14 柏拉圖(擴音器焊接工站之變異來源統計).....................63 圖 4-15 擴音器焊接工站之製程能力分析圖(方案驗証).................66 圖 4-16 麥克風焊接工站之製程能力分析圖(方案驗証).................66 圖 4-17 遮蔽蓋組裝工站之製程能力分析(方案驗証)...................69 圖 4-18 面鏡與上機殼壓合工站之製程能力分析(方案驗証).............71 圖 4-19 電流與充電測試工站之製程能力分析(方案驗証)...............72 圖 4-20 預期生產線平衡圖...........................................74. 1.
(6) 第壹章 緒論 第一節 研究背景與動機 八○年代初期,全公司品管與田口式品質工程之推動,讓日本獲得「品質第 一」的殊榮,當時由日本公司所生產的電子產品之缺點數維持在 5σ的品質水準, 相較之下,美國同業僅有 4σ的品質水準。Motorola 執行長 Bob Galvin 由於深 刻體認到品質作為企業競爭力的重要性,以及作業流程改造之於品質提升的影 響,遂於 1987 年提出一連串精進改革作法,成立 Motorola 大學負責提供六標準 差的訓練課程,全面推動六標準差改善活動。推行數十載,六標準差帶給 Motorola. 政 治 大 股價成長 20%等。六標準差不僅為 Motorola 帶來可觀的財務效益,同時也協助 立 許多世界級企業展現傲人的實績,其中最著名的例子,莫過於奇異公司導入六標. 的具體成效包括,每年銷售成長五倍、淨利成長近 20%、成本節省達 140 億美元、. ‧ 國. 學. 準差的案例,其不僅讓奇異公司邁向營運的高峰,同時也成為執行六標準差的標 竿企業。該公司的執行長傑克.威爾許(Jack Welch)便曾經讚揚六標準差為「奇. ‧. 異所推行過最重要的方案」。由上述兩家國際級企業推行六標準差之成功實例,. sit. y. Nat. 充份証明企業藉由六標準差所獲致之效益不容小覷,因而促成全球各型企業爭相. io. er. 仿效,欲以六標準差改善手法提升企業競爭力。早在 1991 年,國內便有學者著 書將六標準差知識體系介紹給國人(林秀雄,1993) ,到直到 1999 年以後,才開. al. n. v i n 始有長榮航太、金寶電子、英業達、漢翔航空等國內企業陸續推行六標準差,並 Ch engchi U 從中受益。六標準差甚至已成為「品質提升」與「企業再造」的代名詞。 個案公司為一家生產通訊產品之國內企業,旗下包含衛星通訊、行動通訊與 資料通訊三大產品線。就行動通訊市場而言,目前由 Nokia、Motorola、Samsung 等世界級大廠所主導,這些一線大廠囊括了全球市場近八成左右的市佔率,剩餘 的低階市場則由為數眾多的區域型二線廠商所把持,隨著一線大廠紛紛宣佈進入 低階手機市場以提升獲利,預期低階市場的競爭程度將有增無減。個案公司為二 線手機代工廠,早期從 PHS 手機之研發生產業務開始,漸漸拓展到 GPRS 手機, 近年來,由於競爭程度與日俱增,個案公司之行動通訊產品業務面臨到前所未有 的嚴苛挑戰。儘管激烈的競爭環境影響到該產品線的獲利情況,但個案公司仍究 以優越的研發實績與良好的品質,獲得顧客的肯定與信賴,從個案公司近來接獲 2.
(7) 的訂單數量便不難証實此觀點。隨著訂單數量漸漸逼近現有產出的上限,個案公 司開始思考提升生產力的方式與可能性。個案公司體認到,欲在短時間內提升生 產力,須有一套有效的改善流程,於是在外部顧問團隊的建議下,決定藉此機會 導入六標準差改善手法,除了短期間能夠滿足訂單需求之外,同時為個案公司建 立一套系統化的改善流程,作為其回應市場的競爭利器。本人有幸參與個案公司 六標準差改善專案,負責蒐集、研究六標準差系統知識,並協同執行小組共同發 展具體可行之改善方案,以及執行最終的導入工作。在此前提下,遂決定以六標 準差改善流程作為本論文研究之主體,這是本篇論文之主要研究動機。 國內推動六標準差的企業日漸增多,但由於缺乏實務經驗,因此常須仰賴管 理顧問團隊或專案的意見,成本高昂,而成效卻未必顯著。在學術上探討六標準. 政 治 大 寶貴的知識來源,因此若能藉由個案實例介紹,深入探討六標準差在實務推動過 立. 差的個案研究極為少見,但此類文獻對於有意推動六標準差之企業而言,卻是最. ‧ 國. 學. 程當中的成功經驗與遭遇難題,相信對於卻投入六標準差學習行列的企業而言, 將有莫大的助益,此亦為本篇論文另一研究動機。. ‧. 第二節 研究目的. y. Nat. sit. 本研究以個案研究(Case Study)的方式,介紹個案公司推動六標準差的過. n. al. er. io. 程,研究重點放在個案公司如何運用六標準差改善流程,進行生產線改善,並創. i n U. v. 造出高績效的改善成果。因此,本研究的目的可歸納如下:. Ch. engchi. 1. 藉由文獻探討,歸納出一套配合個案公司專案特性之六標準差改善流程。 2. 運用所歸納出之六標準差改善流程找出影響生產力之關鍵因素,並據此發展 解決方案。 3. 藉由本研究之規劃與執行,為個案公司建立一套生產線改善之示範模式。. 3.
(8) 第三節 研究流程 本研究在確定研究主題,動機與目的之後,便開始蒐集及閱讀六標準差相關 文獻資料,同時調查個案公司生產線相關資料。隨後,再與個案公司高階主管及 專案執行小組進行專案的界定工作,最後便進行個案研究內容的撰寫。研究流程 如圖 1-1 所示。 確定六標準差之研究主題,動機與目的. 蒐集及閱讀相 關文獻資料. 立. 調查個案公司 生產線狀況. 政 治 大. 學 撰寫個案研究內容 (個案公司運用六標準差改善流程進 行生產線改善之歷程). Nat. io. sit. y. ‧. ‧ 國. 與個案公司高階主管及專案執行小組 進行專案的界定工作. n. al. er. 個案公司推動成功經驗及結論與建議. C圖h1-1 研究流程 U n i engchi. v. 第四節 論文架構 本論文共分為五章,第壹章之緒論乃說明本研究之背景、動機、目的與論文 架構。第貳章之文獻回顧方面,以闡釋六標準差起源、系統概念、推動架構為重 點。第參章之研究方法則是根據文獻蒐集,同時配合個案公司現況,發展出最適 之六標準差改善流程,以作為專案執行之依據。第四章之個案研究將個案公司執 行六標準差之經過進行詳細說明,並將專案效益彙整於本章的最後。第五章之結 論與建議則歸納個案公司執行六標準差之成功原因與遭遇問題,並提出本研究之. 4.
(9) 第貳章 文獻探討 第一節 流程管理 一、流程的定義與分類 根據王貳瑞(民 90 年)的定義,流程乃為達成某一特定目標或結果所必須 具備的種種系列性作業活動,這些作業活動內容包括人員、設備、材料、制度、 方法與時間。而 Hammer(1993)則定義流程為從事相關活動的一個有組織團體, 齊心協力創造一個對顧客有價值的結果。 殷宜萱、黃俊哲、賴谷鑫及謝清佳等人於 2002 年共同研究之矩陣調整法進. 1.. 政 治 大 流程是以活動為單位的結構。此結構是設計用來針對特定的顧客及市場來產 立 生特定的產品或服務。. 2.. 流程具有開始與結束,同時能夠界定何者為輸入,何者為輸出。流程是用來. 行作業流程再造的報告中,強調流程需要滿足下列幾點:. ‧ 國. 學. 主導工作及如何進行工作的結構。 流程也代表評估改善與衡量的尺度,例如:衡量成本、時間、產品品質、顧. sit. y. Nat. 客滿意度。. 假設以顧客的觀點來界定流程,組織必須要從事一些可以符合顧客價值觀的. io. 必要工作。. er. 4.. ‧. 3.. al. n. v i n 綜上所述,可以瞭解到流程為一群具有相關性的跨功能工作,透過一連串有 Ch engchi U 順序的活動來服務顧客,以達成特定的企業目標。而藉由流程觀念的建立,企業 內的任何作業或活動邏輯便能夠清楚地定義,各種分析、訓練與改善也才有清晰 可循的依據。 流程可簡單分為企業流程(Business Process)與工作流程(Work Process) 。 企業流程為在特定目標下,多個相關工作流程的組合,而每一個工作流程任務則 是經過多個個體(Individuals)組合成群體(Team) 。如圖 2-1 所示,每一個流 程階段皆須從能量、品質、成本、時間、競爭力、資源及控制各功能上,考慮其 是否能夠創造附加價值。. 5.
(10) 目 標. 企業流程. 工作流程 (一). 工作流程 (二). 工作流程 (三). 附加價值 能量 品質 成本 時間 競爭力 資源 控制. 附加價值 能量 品質 成本 時間 競爭力 資源 控制. 附加價值 能量 品質 成本 時間 競爭力 資源 控制. 圖 2-1. 學. ‧ 國. 立. 政 治 大. 企業流程、工作流程及要素說明. 資料來源:王貳瑞,流程管理,華泰書局,民國 90 年。. ‧. 而所謂的企業流程,乃是指針對企業體系之運作目標,發展出一組具邏輯性. y. Nat. sit. 之相關任務,能夠有效整合資源,創造出產品或服務,以達成明確的企業成果。. er. io. 本研究將各家學者對於企業流程的定義進行彙整,如表 2.1。. n. a表l 2-1 企業流程定義彙整 i v n Ch U i e n g c h企業流程定義. 學者 Gohre(1985). 流程是組織訂定的一些規則,結合金流、物流、資訊流 及文件流等,用以創造及提供產品與服務。. Pall(1987). 企業流程為產生特定結果的活動,是由人員、物料、能 源、設備與程序等合乎邏輯的組織。. Hammer & Champy (1990). 企業集合各類原料,製造所需產品的一連串活動。. Daveport & Short (1990). 一組邏輯相關任務,用來達成企業預定的成果。. Murray(1991). 企業流程是一組功能或工作組合,能夠有效整合並創造 出產品或服務。. Daveport(1993). 企業流程是一組行動的結構,指為特定顧客或市場生產 特定產品所安排有結構、可衡量的一組行動。. Daveport(1993). 為跨越時間與地點的一組特定有次序工作,其有清楚的 6.
(11) 投入與產出、開始與結束的關係。 Johansson et al. (1993). 用來將投入轉換為產出的一組連結活動,它可將投入加 值與創造出使受惠者得到更為有用與有效的產出。. Scherr(1993). 指特定時間產生特定結果的顧客與供應商系列關係。. Manganelli & Klein (1994). 是將企業投入轉為產出的相關系列任務. Teng et al.(1994) 是指用來達成企業特定產出的一組邏輯相關工作。 Weiss(1994). 企業流程是可以取得訂單更快與更有效的步驟。. Gilmore(1995). 企業流程是指用來達成特定企業成果的一組邏輯相關 任務。. Bryant & Chan(1996) 企業流程即是企業內部任務,為改造作業的核心所在。 寶成工業附設訓練暨 一個完整的投入產出與附加價值的過程,而此過程必須 研發中心(2000) 滿足顧的需求為目的。. 政 治 大. 一群具有相關性的跨功能工作,透過一連串有順序性的 活動來服務顧客,以達成特定的企業目標。. 籃柏林(2000). 學. ‧ 國. 立. 二、企業流程再造的定義與構面 (一) 企業流程再造的定義. ‧. 企業流程再造的定義各家不一。Hammer 與 Champy(1993)定義企業流程再. y. Nat. 造為「根本性的重新思考,徹底翻新作業程序,以期在企業的營運成本、服務、. io. sit. 品質及速度上獲得巨幅的改善」;而 Davenport 等(1993)卻認為企業流程再造. n. al. er. 乃對組織內或組織間的營運流程重新進行分析與設計。相較之下,前者比較傾向. i n U. v. 於激進式的改變(Radical Change), 而後者則是小幅的改善(Continuous. Ch. engchi. Improvement) ,儘管如此,兩者的精神皆在於針對顧客需求,重新規劃工作方式, 以提供最好的產品與服務。 賴秀鳳(民 86 年)則分別從「程序」、「組織」、「技術」三個角度,針對流 程再造,歸納出各家學者之觀點,結果如表 2-2。. 7.
(12) 表 2-2 學者. 定義. Spencer(1992). 以顧客為基礎,透過程序以致力於提升生產力及品質的方法。根據 邏輯設計的服務程序可以用效率、效能及適應性來加以評估。. Davenport(1992). 程 序 取 向. 流程再造之取向觀點. 對組織內部或組織間的工作流程來作程序分析與再設計。. Carr(1993). 透過徹底、顧客為中心的變革,協助企業創造具策略價值的績效突 破。. Hammer & Champy (1993). 以程序的觀點,檢視企業內部的活動而重新設計現有的工作方法, 以達成大幅提昇績效的目的。. Belmonte & Murray (1993). 徹底重新設計企業程序,以顯著地提升績效的一種整合程序之方 法。. Thomas(1994). 主要在於描述對企業程序作激進的細查、提出疑問、重新定義並重 新設計之,以減少對程序目標沒有影響的活動,增加自動化的活動 以減少人為判斷的輸入。. Omarani(1992). 為企業營運的一種基本重新方法,包括產品是如何去製造、市場 化、銷售,以及最終如何到達顧客手中. 政 治 大. 立 對組織作根本的分析,並重新設計組織結構、工作定義、薪資結構、. ‧ 國. Richman & Koontz (1993) Taiwar(1993). 為顧客服務與企業效率上達到劇烈改善的一種方法。. io. sit. y. 將組織中具策略性和附加價值的事業,及其相關系統、政策和組織 結構激進地作一重新設計,以促成組織工作流程和生產力達到最適 水準。. er. Nat. Klein(1994). Romney(1994). 將工作程序、組織結構、資訊科技、工作內涵與流程作徹底的重新 設計,以大幅提昇顧客價值與生產力。. ‧. 組 織 取 向. 學. Guha et al.(1993) 企業的工作程序與控制程序。在某些情況下,甚至是對組織文化與 管理哲學的重新評估。. 一種革命性工程,挑戰所有老舊的組織結構、工作流程、工作特性、 管理程序、控制和組織的價值文化。. al. n. v i n Ch 為了配合大環境的變化,讓組織中的核心技術能夠有效運作,所做 吳思華(民國 86 年) engchi U 的一種組織重新設計。 組織為利用人力素質與科技變遷所帶來的利益,而重櫎設計工作方 式。其中人力素質上的變化乃是由教育水準的提高,使組織獲得有 Schnitt(1993). 知識、有經驗的員工,有能力去完成整個工作;而科技上的變革使 得資訊可以同時出現在組織的各角落,極使得必須使用同一資訊的 工作得以同時進行。. 技 術 取 向. Parker(1993). 組織利用一些變革的工具,以科技作為觸發的手段,以促使組織從 事激烈的變革,以迎合顧客之需。. Canton(1994). 再造工程不只是一個行銷的使命,更是利用政策上的努力,使主管 相信只要購入新的硬體設備或是問題解決導向的軟體,就能解決所 有企業的問題。. Teng et al.(1994). 使用科技改變序的基本性質,驅動使用最佳化的科技以支援業務工 作,並且促使資訊科技與組織之間的配合更自然與合理化。. Furey et al.(1994). 策略性再造工程是結合資訊科技,重新設計整個運作過程,來讓顧 客心目中的價值極大化。 8.
(13) 綜合以上學者的定義,可針對企業流程再造歸納出以下結論: 1.. 企業流程再造的最終目標,是要以提高顧客滿意為目的,並且以跨越組織界 限的方式,善加運用各項資源,重新建構新的企業流程,以提升企業的競爭 優勢。. 2.. 企業流程再造乃是企業為求提升組織的整體績效,以資訊科技為基礎,所進 行的一種躍進式企業流程變革。. (二) 企業流程再造的構面. 林晉寬等(民 86 年)將企業流程再造分為再造範圍、再造層次、再造方式 與再造目標等四個構面,說明如下: 1.. 再造範圍. 政 治 大 入與產出之整體企業流程,甚至以跨越現有流程範圍為對象,亦可以企業主 立. 企業流程再造的範圍可從顧客價值出發,並以較為廣泛的思考方式,涵蓋投. 再造層次. ‧ 國. 2.. 學. 要流程為主的中度範圍,或縮小至如客戶運交作業的小範圍。. ‧. 從層次劃分,企業流程再造可以最基本的作業次為對象,亦可擴大到涉及組 織結構調整與人員權責重新劃分的組織層次,或者提升到整個經營體系變革. y. Nat. er. 再造方式. io. 3.. sit. 層面的策略層次。. al. n. v i n C radicalh change)或連續與小幅的改造(Continuous engchi U. 再造觀念就是一種變革,由於企業所處環境不同,方式可分為一次與劇烈改 造(One-shot and. improvement)兩種。前者主要適用於競爭較為激烈的經營環境,需要以較. 大幅度變革才能創造企業利基或達到績效提升目標,但風險相對較高;後者 則認為企業是建立在經營而非賭注觀念上,因而要有改造是一種持續過程, 績效提升則是建立一連串努力上的理念。 4.. 再造目標 再造目標可分為效率或效果兩個層次。. 9.
(14) 三、流程分析之工具與方法 (一) 流程分析工具. 企業流程再造的重點在於流程,因此需要有流程的分析工具來輔助說明企業 目前的流程,以及改善後的流程。拜資訊科技的發達與企業再造議題的熱門,因 而發展出各式的電腦輔助工具,如 IDEF、CIM-OSA、ARIS 等。然而,企業流程再 造應把焦點放在如何藉由改善工具與方法,達到顧客滿意的提升,而不是輔助軟 體的學習。 由於圖表具有將諸多文字敘述作一簡單彙整的概念,在許多企業營運的作業 程序、活動、任務與資訊系統設計時,流程圖的製作往往能針對資源投入、處理 與產出等連續程序作一緊密連結,並將所有工作相關流程的意義與內容清楚表. 政 治 大 運資料的處理,流程圖可分為以下幾種類別(王貳瑞,民 90): 立. 示,有助於組織目標的達成,確實為流程管理相當有效的一項工具。針對企業營. 系統流程圖:表示作業與作業程序間的關係。. 2.. 程式流程圖:顯示個別電腦程式作業情形。. 3.. 資料流向圖:表示作業間資料流向的合理性。. 4.. 文件流程圖:顯示文件在各部門間的流通關係。. 5.. 系統圖:提供電腦系統設備之配置情形。. 6.. 控制流程圖:顯示一項作業所需的內部控制文件表單之詳細流向。. ‧. ‧ 國. 學. 1.. n. er. io. sit. y. Nat. al. Ch. engchi. 而流程圖之間的相關性則如表 2-3 所示。. 10. i n U. v.
(15) 表 2-3 名稱. 流程圖相關性分析. 無法說明之要點. 補充流程圖. 1. 無法完全掌握文件在哪一部門存放 控制流程圖 2. 對於資訊流及文件流區分不清 3. 檔案的存檔方式(以日期、文字或數字存檔)無法得知 4. 缺乏文件控制查核點 文 件 流 程 圖. 5. 未考慮資料庫的設置. 資料流程圖 系統流程圖. 6. 對於與客戶或廠商間支票、現金及發票的流向無法得知 資料流程圖 7. 與廠商的採購流程無法清楚得知 8. 僅知文件流向,但對於作業間的資料流向則描述不清 9. 無法清楚顯示外界個體與系統之間資料流程情形 10. 缺乏電腦作業系統的作業程序. 系統流程圖. 11. 缺乏電腦系統配置情形. 系統圖. 治 政 大 12. 不知系統所使用的程式 立. 系統圖. y. 控制流程圖. sit. 程式流程圖 系統流程圖. 4. 缺乏作業設備的配置情形 5. 對於各個作業的核准權責無法得知. io. n. al. 7. 無法得知電腦作業系統的作業程序. Ch. er. 6. 缺乏系統所使用的程式名稱. 控 制 流 程 圖. ‧. ‧ 國. 學. 1. 無法知道各個作業該由哪一部門或人員來處理 文件流程圖 2. 對於表單的茫數、原始發出部門及其流向,無法清楚得 控制流程圖 知 3. 無審核的工作. Nat. 資 料 流 程 圖. 系統/程式流 程圖. i n U. v. 系統流程圖. 1. 缺乏詳細的資料流向 2. 無法得知與客戶或廠商間支票及現金的流向. 資料流程圖. 3. 未考慮資料庫的設置. 資料流程圖 系統流程圖. 4. 未提及電腦系統設備配置情形. 系統圖. 5. 缺乏電腦程式作業情形. 程式流程圖. 6. 缺乏電腦作業系統的作業程序. 系統流程圖. engchi. 資料來源:王貳瑞,流程管理,華泰書局,民國 90 年。. 11.
(16) (二) 流程分析方法. 張國良等(民 86 年)認為流程再造的分析方法應該具備簡單、易學及易懂 的特性,讓所有參與再造的成員都可以快速應用且瞭解流程圖代表的含意,而將 所有精神放在流程再造本身。 王錦川(民 88 年)提出方法研究的目的在於研究制定最佳的工作方法,即 制定為產出或產品而經濟地運用人、設備或材料的方式,可透過大處著手來分析 整個程序或作業,亦可由較細暢分析作業研究的動作。其中大處著手的工作分析 上,包括程序分析、作業分析與資訊分析三個部分,小處著手的工作分析,包括 動作分析與動作經濟原則,如圖 2-2。. 政 治 方法研究 大. al. 操 作 人 流 程 圖. 人 機 流 程 圖. Ch. 圖 2-2. 多 人 圖. y. sit. 資訊分析. 多 人 機 流 程 圖. 系 統 流 程 圖. engchi U. er. 組 作 業 程 序 圖. 工作分析 (小處著手). ‧. 線 圖. n. 流 程 程 序 圖. 作業分析. io. 操 作 流 程 圖. 工作分析 (大處著手). Nat. 程序分析. 學. ‧ 國. 立. 表 單 流 程 圖. 資. v ni 料 流 程 圖. 動 作 分 析. 動 作 經 濟 原 則. 方法研究之分析方法. 資料來源:王錦川,工業工程與管理,五南圖書出版公司,民國 88 年. 其中,程序分析屬於整個製程的大體分析,主要在研究如何利用剔除 (eliminate) 、合併(combine) 、重排(rearrange)與簡化(simplify)技巧, 使各個操作合理化,常用之分析方法包括: 1.. 操作流程圖:一種鳥瞰式的通盤瞭解,僅包含了操作與檢驗兩個符號。. 12.
(17) 2.. 流程程序圖:運用操作、檢驗、搬運、儲存、遲延五種現象,對整個流程作 一詳細的紀錄。. 3.. 線圖:主要功能在分析產品或人員的流動路線圖,依序標於服務地點之平面 佈置圖。. 4.. 組作業程序圖:為流程程序圖的延伸,在記錄同一時間內一個團體中個人所 作的事。. 而在資訊分析方面常用的圖表包括: 1.. 系統流程圖:主要用來瞭解一個系統內活動的順序。. 2.. 表單流程圖:用來瞭解部門間表單流動的情形。. 3.. 資料流程圖:主要在表現出傳輸資料的先後次序及其關聯性。. 政 治 大 確認流程圖的範圍:就企業經營而言,假如一個系統可以依不同程序拆解成 立. 王貳瑞建議繪製流程圖時,可依照下列步驟: 1.. ‧ 國. 學. 某些次系統,其各個次系統亦皆可繪製成流程圖。藉此一觀念,企業內的採 購、銷售訂單處理、生產、收入/支出、客務、網路作業等各項作業資訊,. 2.. ‧. 均可形成流程圖。. 獲取與流程圖相關的資料與資訊:此一步驟乃是流程圖繪製過程中最重要的. y. Nat. er. al. n. 3.. io. 模糊的情形。. sit. 工作。缺乏足夠的資料、資訊或對系統認識不完整,皆會導致流程圖錯誤、. Ch. 號構成一個有意義的圖形。 4.. v. 繪製流程圖:將上一步驟所得之文件、表單、程序以及組織部門,以標準符. engchi. i n U. 確認流程圖:對於流程圖的簡明性與正確性加以檢驗與測試。其可供參考之 依據包括: (1) 循著流程圖追蹤文件表單之處理情形。 (2) 允許流程相關人員檢討察視流程圖是否尚有改善空間。 (3) 邀請與流程圖無關之人員檢討所設計之流程圖。. 13.
(18) 第二節 六標準差品質改善手法. 一、六標準差之起源與發展 早在一九七○年代末,Motorola 公司內部對於產品品質便出現危機感,於 是在當時的董事長巴普.伽爾賓的號召之下,開始發起一系列的品質改善活動。 隨後於一九八○年代初期,Motorola 當時正打算將袖珍型呼叫器打入日本市場, 但與日本廠商的不良率相較之後發現,Motorola 的品質水準仍究不敵日本企業, 因而決定推動以提升品質為目標的「六標準差品質計畫」(Six Sigma Quality Program) ,於是 Motorola 便在這樣的時代背景下展開六標準差品質改善活動(周 漢光,民 92 年)。. 政 治 大. 在 Motorola 成功推動六標準差改善活動之後,陸續出現企業相繼投入六標. 立. 準差的研究行列,如聯訊、德州儀器等。但真正讓六標準差聲名大躁者,乃奇異. ‧ 國. 學. 公司於一九九五年,由當時的執行長傑克.威爾許(Jack Welch)大力推動下的 六標準差品質改善活動,該活動專注在產品製程,以缺陷改善為主要目標,藉由. ‧. 系 統 化 改 善 手 法 及 流 程 中 每 百 萬 件 不 良 品 數 ( Defect Per Million Opportunities; DPMO) 之衡量,達到改善流程與產品品質的目的 ,其帶給. y. Nat. sit. Motorola 的效益包括每年銷售成長五倍、淨利成長近 20%、成本節省達 140 億美. n. al. er. io. 元、股價成長 20%等,執行長傑克.威爾許便形容六標準差為「奇異所經歷最具. i n U. v. 挑戰性、最具回報潛力的活動」。由於奇異執行六標準差的成效十分顯著,一些. Ch. engchi. 知名國際企業陸續跟進,如杜邦(Dupont) 、聯邦快遞(FedEx) 、嬌生(Johnson & Johnson)、柯達(Kodax)等,使得六標準差知識體系之應用與發展更加地完 整。 自從八○年代中,Motorola 開始推動六標準差活動以來,學術界陸續針對 六標準差建立理論架構,同時為實務界的推行提出建議。Breyfogle(2003)依 推行六標準差之目的,將六標準差之發展歷程分為三個時期,包括缺陷降低 (Defect Reduction) 、成本降低(Cost Reduction) 、價值創造(Value Creation) 三個世代。Pearson(2001)則根據美國企業推行六標準差的期間及執行內容, 將六標準差的發展分為設計期、淨化期、成果期、競爭意識期及新技術期等六個 階段,如表 2-4,從該表可推測六標準差知識體系之發展已漸趨成熟。. 14.
(19) 表 2-4 時間. 六標準差之發展階段. 1985~1992. 1993~1994. 1994~1996. 1996~1997. TI Motorola. ABB. Allied Signal GE. Bombardier Lockheed GE Martin Nokia Sony Crane Polaroid Corporation Avery Dennison Shimano. 設計期. 淨化期. 成果期. 競爭意識期 新技術期. 代表企業. 發展階段. 1997~. 政 治 大 寶電子、英業達、漢翔航空等企業,迄今雖僅有六年的時間,但在目前的國內企 立. 國內企業則於一九九九年開始漫延六標準差品質改善熱潮,如長榮航空、金. ‧ 國. 90 年)。. 學. 業界中,六標準差品質改善手法卻已成為最炙手可熱的管理方法(賴榮仁,民. ‧. 二、六標準差之意義. 本節將分別說明六標準差的統計意涵及管理意涵,從不同專家學者的觀點. y. Nat. er. io. (一) 統計意涵. sit. 中,彙整出六標準差之意義。. al. n. v i n C 年),母體的標準差一般希臘字母「σ」表示。 平均數的方根」(顏月珠,民 78 h engchi U 就統計學的角度而言,標準差係指「一群數值與其算術平均數之差異平方的. 標準差所代表的意義為母體中的每個數值與母體平均數的距離之平均數的概 念,可用來表示母體中數值的離散程度(Hilton,1995),在到達正負六標準差 的水準之下,可幾乎涵蓋全部數值,僅剩下百萬分之零點零零二未被涵蓋。. 就六標準差而言,則要視提供給顧客的產品或服務「上下規格包括流程產出 的數值或流程產出物特性的數值母體的幾個標準差,包括 2k 個,便稱此為 k 個 標準差」(王丕丞,民 92 年)。 然而,在六標準差的架構之下,須包含一個典型情況,即流程將隨著時間變 化而有 1.5 標準差的中心偏移(1.5 Sigma Centering Error Shift)(Harry and Schroeder,2000) 。Pande, Neuman 與 Cavanagh(2000)認為此情況在統計學家 之間仍存在爭議,而陳文化(1994)亦提到過去只要正負 4 標準差,中心偏移 1 15.
(20) 標準差即可,但在六標準差的架構之下,認為其並非隨機干擾(Perturbing Nonrandom Influences)所造成的中心偏移為 1.5 標準差(1992)。所以,當一 家公司宣穩其為六標準差公司時,其實質意義為短期內公司的表現為六標準差, 但長期而言,由於上述中心偏移的現象產生,公司的表現應為 4.5 標準差(Harry and Schroeder,2000)。 (二) 管理意涵. Harry(1997)認為六標準差的方法為提供企業一連串手法及統計工具,使 企業獲得突發性的獲利能力,以及品質提升的策略,不管是企業的產品或服務, 均可使用六標準差的方法。 Pande 等(2002)認為六標準差是個結合強勢領導和基層動力及參與的系統;. 政 治 大 大企業的成功。而六標準差之驅動要素,在於對顧客需求的深入掌握,並嚴謹地 立. Pande 等(2002)認為六標準差為全面且具彈性的系統,可用以獲得、維持並擴. ‧ 國. 學. 運用事實、資料和統計分析,以及全面聚焦於業務流程的管理、改善與創新。 Brue(2002)認為六標準差是一種精確而有適應性的方法,用以連結員工、. ‧. 流程及產出,藉此獲得所要的結果。不論是在產業、經營、產品或服務上都可在 專案中看到顯著成果。. y. Nat. sit. Young(2001)指出,公司通常由內而外地,以近來平均值為衡量基礎,進. er. io. 行績效評估。但顧客卻不以平均值來評斷公司的表現,六標準差強調變異基礎思. al. n. v i n Ch Smith 等(2002)認為六標準差是一種高績效及數據導向手法,用以分析企 engchi U. 維(Variance Based Thinking),先降低流程變異,再改善流程能力。. 業問題的根本原因並解決之。六標準差連結了企業產出與市場需求。. Ehrlich(2002)定義六標準差為一種持續改善流程品質與生產力,以得到 獲利底線(Bottom Line)之紀律化與資料導向方法。它主要經由降低流程上的 變異,進而導致一致性且可預測之產出。 鍾朝嵩(民 91 年)認為六標準差管理就是以 6σ值為目標,在增強顧客滿 意,使經營資源的消費控制到最小限度下,活用統計手法,改善日常的業務流程, 使能突破性地改革企業利益的有效管理方法;楊錦瑤、陳建雄與陳高山(民 91 年)認為六標準差是一種長遠性的企業變革方案,藉由突破性手法,達到大幅降 低產品價格、提升品質、提供服務與縮短交期,最終提升企業的獲利,以作到全 方位的顧客滿意。 16.
(21) 王晃三(民 91 年)則進一步將六標準差區分為三種性質定義: 1.. 統計性定義:流程變異範圍不超過設計允差的一半(Cp = 2.0),且平均值 左右偏離目標值 1.5 倍標準差範圍情況下的品質水準。. 2.. 操作型定義:相當於每百萬次作業中,失誤低於 3.4 次(DPMO)之品質水準。. 3.. 系統性定義:確保作業流程達到每百萬次的操作機會中,至多出現三點四個 失誤(3.4 ppm)的品質水準之方案或配套措施。 綜合多位學者對六標準差的看法,六標準差的意義並非僅止統計數字而已,. 它是一項完全的管理承諾,以顧客導向、追求卓越、改善流程、以衡量為基礎的 哲學。六標準差使得組織內每個層級更加貼近顧客、市場與外在環境的轉變,並 且使得員工、顧客與利害關係人進而受益。因此,廣義而言,它是一種管理導向. 政 治 大 客滿意度。六標準差同時也是一項技術,推動時須搭配適當的管理措施,以強化 立. 的系統手法或改善流程的科學作法,不僅創造卓越的財務績效,更能顯著提升顧. ‧ 國. 學. 企業競爭力,並達成企業獲利的目的。其關鍵在於透過顧客聲音得知其需求、以 統計觀點來檢視問題,慎選資料來源以蒐集數據,利用統計分析技術發掘問題的. Nat. y. 品作業品質。. ‧. 原因,並經由系統化的訓練與權責清楚的組織分工執行專案,最終達成完美的產. er. io. (一) 管理策略. sit. 三、六標準差之管理與執行. al. n. v i n C 立的規劃(Plan) 、實施(Do) 、查核(Check) h e n g c h、處置(Action)四大步驟,簡稱 i U. 一般而言,企業進行品質改善運動時所採用的改善模式,多半依循戴明博士所建. 為 PDCA。六標準差品質改善手法進一步將 PDCA 改良為界定(Define)、衡量. (Measure)、分析(Analyze)、改善(Improve)、控制(Control)五大步驟, 簡稱為 DMAIC 五階段的改善循環。隨著,競爭環境的改變,以及不同組織特性, 便發展出三種不同的管理策略,即流程改進、流程設計/重新設計、流程管理等 策略,不管哪一種策略,其本質皆為組織的流程。以下便針對三種不同的六標準 差管理策略進行說明,並整理如表 2-5: 1.. 流程改進:藉由方案的執行,使企業找出流程績效不良之問題根源,並妥善 解決之。其解決的方式是在不變動流程本質的前提下,除去其中的變異。以 六標準差而言,流程改進會找出產出不想要的 Y(誤差)的主要 X(肇因)。. 2.. 流程設計/重新設計:當企業發現若僅僅改進現有流程將無法達到顧客要求 17.
(22) 的品質時,便藉由此策略進行流程再造。Hammer & Champy(1993)曾指出 持續改進與流程再造,在流程的存續中,可以長期相輔相成。而六標準差則 是整合兩者,成為維繫成功之主要互補策略。 3.. 流程管理:專注於全體已知的流程管理,以取代由不同的內部單位來管理個 別部門,內容涉及全面改裝一個組織的結構和管理方式。. 表 2-5. 六標準差三大管理策略. 管理策略. 流程改進. 流程設計. 流程管理. 結構. DMAIC. DMADV. DMAC. 定義. 維持工作流程基本 架構不變的情況 下,除去影響企業績 效問題根源,以修正 問題之少數致命因 素。因此,大多數之 六標準差專案都是 武了改善流程而努 力。. 當原本結構或流程 跟不上市場需求變 動時,企業就須對其 主要流程重新思 考,設計新的流程, 乃此結構下之策略。. 流程管理是專注於 全體組織的管理流 程,內容涉及了全面 改造組織之結構和 管理方式,故流程管 理通常是三者中最 難駕馭者。. 1. 界定(D) :界定問. 1. 界定(D) :界定流 程、產品、服務的 顧客要求和目標。 2. 衡量(M) :衡量並 做到符合顧客要 求的績效。 3. 分析(A) :分析並 評估流程、產品、 服務設計。 4. 設計(D) :設計並 執行新流程、產 品、服務。 5. 驗證(V) :驗證結 果並維持績效。. 1. 界定(D) :界定流 程、關鍵顧客要求 和流程擁有人。 2. 衡量(M) :衡量主 要流程指標及績 效是否達到顧客 要求。 3. 分析(A) :分析資 料以強化衡量並 修正流程管機制。 4. 控制(C) :控制績 效,透過監視投 入、作業、產出, 對問題和流程變 異做出即時回應。. n. 細部流程. Ch. y. sit. er. io. al. ‧. Nat. 題。 2. 衡量(M) :衡量誤 差和流程作業。 3. 分析(A) :分析資 料並找出問題的 肇因。 4. 改善(I) :改進流 程並去除誤差的 肇因。 5. 控制(C) :控制流 程以確定不再發 生誤差。. 學. ‧ 國. 立. 政 治 大. engchi. i n U. v. 以上三種策略可複合應用,端看企業在選擇策略時,需要哪些步驟加以分析及衡 量,許多公司採用 DMAIC 或稍做改變的模型來推行六標準差專案。本研究亦採用 DMAIC 步驟展開,乃因本研究主要是在不改變現有流程情況下,加以衡量並且針 對缺點提出改善建議,因此,適用於流程改進之策略。 18.
(23) (二) 導入要領. 以下就六標準差之導入要領作一簡單說明。 1.. 六標準差須高階主管的承諾與領導,方能成功,例如 GE、Motorola、 AlliedSignal 等企業,皆由其執行長身先士卒,將六標準差品質改善手法 推動到組織內部各階層。. 2.. 若初次推動六標準差專案,可由製造部門開始,著眼於降低成本與浪費、提 升良率與生產力,藉此達到顧客滿意及績效提升的目的。待專案獲致成效, 同時組織內部人員對六標準差也有基本的瞭解,則可逐步推廣到非製造部 門。. 3.. 以品質、成本、交期及產量為績效衡量的標的,並且以財務數據評估專案的. 政 治 大 一件專案的績效以每年節省或增益五萬美金為目標,以 AlliedSignal 為 立 重要性,藉此選定專案的依據及評估實際的成效。. 4.. ‧ 國. 5.. 學. 例,初期專案利益超過一百萬美元。. 實際執行專案的主要人員,其六標準差專案佔其工作時間之比重,約可佔. Nat. y. (三) 執行程序. ‧. 50%~100%。. n. al. er. 理論面. io. 1.. sit. 六標準差的執行程序可從理論面與實務面兩個方向進行說明。. v. Eckes【23】認為,六標準差的執行程序乃運用科學的方法來處理事務,方 法包括:. Ch. engchi. i n U. (1) 觀察:善用直覺及經驗,確認目標及其特性,並辨別出各項細微的變化。 (2) 分類:根據標的之屬性,進行集群,並從不同的集群之間,找出相同及 相異處。 (3) 量測:運用相同的量測工具及衡量單位,比較兩個相似量。 (4) 組織及歸納:由簡入繁地敘述、記錄、比較、分類、排序各項資料,找 出其歷史軌跡。 (5) 演繹及推論:化繁為簡、由簡馭繁地解釋各種現象的發生過程與成因。 (6) 確認變數:根據假設,建立模型,並使用方法工具來証明假設。 (7) 系統化:整合實驗設計中的流程、技巧、並將其標準化。. 19.
(24) 2.. 實務面 實務面則以 GE 所採用的 DMAIC 之 5 個步驟最具代表性,其目的分別是以流 程觀點界定(Define)核心問題點、衡量(Measure)以蒐集數據、分析 (Analyze)以瞭解造成問題的關鍵因素、改善(Improve)以排除關鍵因素 的不穩定性、控制(Control)則以統計製程管制技術確保所有的指標在管 理範圍內。茲將 DMAIC 改善流程整理如下: (1) 界定(Define):確認問題,並準備進行專案。 (2) 衡量(Measure):量化問題及相關參數。 (3) 分析(Analyze) :利用統計及品質工具,對數據進行分析,並找出流程 中的變異。. 政 治 大. (4) 改善(Improve):利用品質改善手法,提出改善方案來消除流程中的變. 立. 異。. ‧ 國. 學. (5) 控制:持續不斷的監控,確認變異不再發生,以及效益持續增加中。 Eckes(2001)亦指出,一旦組織利用六標準差的商業流程概念來進行組織. ‧. 內部基礎建設,其所面臨的問題乃將原有的流程加以改善或創造新流程。但流程 改善的方式在組織內部需率先執行。建立新流程的動機,包括以下幾點:. al. er. io. (2) 當原有流程經多次改善仍無法妥善運作。. sit. y. Nat. (1) 為達成商業策略目標。. n. v i n Ch 不論由理論面或實務面來探討六標準差執行程序,其原則皆為:確認問題、 engchi U. (3) 原有流程雖可運作,但無法達到六標準差的標準。. 找出根本原因、模組化解決之道、測試改善的方法、並維持成效。 四、執行六標準差之關鍵成功因素 鄭榮郎、郭倉義(1993)指出六標準差之成功關鍵因素為:. (一) 高階承諾:由於六標準差技術密集的管理特性,參與人員與生產設備都是主. 要的核心資源,要使兩者均能充分發揮,必須有目標明確的經營理念、使命 與願景。六標準差管理活動必須靠人員、組織與領導,高階經營者是否有強 烈的企圖心,是企業進行六標準差改造不可或缺的條件。 (二) 績效產出:六標準差專案的實施能夠產生效益,才會引起企業經營層的重. 視。以 GE 而言,六標準差開始進行投資的 1996 年出現虧損狀況,然而在 1998 年馬上產生 750 萬美金的六標準差效益,同時年度都有六標準差專案 20.
(25) 在進行,威爾許聲稱因為力行成本降低與排除無效率,一年所節省可達 8 億 至 15 億美元的結果。 (三) 流程架構:六標準差具有解決問題與提升競爭力的結果,但其前提必須是以. 流程導向,若是全面品質管理沒有經過依顧客的需求進行流程分析,瞭解顧 客期望與現況流程之間的差距,六標準差無法從現有流程當中,依照顧客的 期待有效率改造工作流程。 (四) 顧客市場導向:六標準差所要努力的方向,是要如何維持顧客的忠誠度與滿. 意度,也必須隨時注意市場的動態,因此企業有完整的流程搜集消費者與市 場的資訊,並將此資訊加以加工、分析與判斷,並與企業流程產出進行比較、 分析、檢討與改善。. 政 治 大 與其他品質改善專案不一樣,因此誘因設計基本上要導引企業往正面的角度 立. (五) 誘因導向:企業的報酬制度不可以排除六標準差專案,因為六標準差基本上. ‧ 國. 學. 發展,如 GE 將六標準差的任務,與人力資源管理晉升考核進行結合,完成 六標準差的任務者,可以成為企業高階主管的候選人,企業也可以設立各項. ‧. 獎勵辦法,讓全員積極參與各項六標準差工作。. (六) 六標準差專職人員:由於六標準差品質管理的專業性,要導入六標準差的企. y. Nat. sit. 業必須能夠訓練高度專業人員,以全職的方式組成改善的專案團隊,如同黑. n. al. 人員對於六標準差的實施具有關鍵的地位。. Ch. engchi. 21. er. io. 帶(Black Belt)與大黑帶(Master Black Belt)的功能,六標準差專職. i n U. v.
(26) 第三節 生產力. 一、生產力的意義 企業經營所面臨的環境瞬息萬變,相對地經營管理能力也益形重要,凡是耗 用較少資源而獲得相同產出,或是耗用相同資源而獲致較多產出的企業,皆能在 面對激烈的市場競爭中立於不敗之地,因此,生產力乃企業競爭攸關勝敗的一項 重要關鍵。 生產力(productivity)一詞最早係由重農學派創始人 Quesnary 在 1776 年 所提出,主要是代表一個國家勞動人口平均產出,而至廿世紀初,生產力才有較 為精確的定義,即產出物與為生產此物所需要之平均花費關係。Sumanth D.J.. 政 治 大. (1985)在 1977 年版大英百科全書對生產力的定義為,生產力乃由產出與生產. 立. 該產出所需投入因素之比率。而經濟學家 Siegel(1980)認為生產力是一組數. ‧ 國. 學. 據的比率,分子是產出量,分母是有關投入量。. 綜上所述,生產力是指一系統在某一期間的產出水準與投入資源之比,即一. ‧. 系統的整體效率。申言之,一個系統從其外界環境中引入資源,經過加工處理, 然後製成產品或服務等產出,這種轉換過程的效率,就稱為「生產力」 。 (余朝權,. sit. y. Nat. 1996). n. al. er. io. 綜觀不同專家學者對生產力的定義,都持相似的觀點,在穰穎堅(1994)加 以整理納,具有以下共同的特性:. Ch. engchi. i n U. v. (一)生產力係針對某一系統而言,即任何一生產力量度均有其涵蓋範圍。 (二)生產力可用一系統之產出與投入之比率表示。 (三)生產力反映一系統運作之客觀情形,因而可以當作一項績效指標。 生產力(Productivity)為一般企業於生產管理最常用之績效衡量指標,其 代表投入與產出的關係,它同時需要投入與產出的資料,其公式為: 總產出 所完成之結果 效向 生產力 = ──── = ─────── = ─── 總投入 所消耗之資源 效率 由上述公式觀之,生產力的提高,可透過三種方式,一種為投入的減少而產出不 變,另一種為投入不變而產出增加,亦可能投入減少而產出增加。因此,高生產 力所代表的意義為「單位成本的降低」。這也說明了生產力提升之重要性所在。. 22.
(27) 二、生產力的衡量與評估 Kendrick and Creamer(1965)所提出的企業生產力衡量模式,視生產力為 實質收益與實質成本之比例,並指出三項基本衡量的指標:總生產力、總要素生 產力及偏生產力。Sink 則定義出兩項生產力衡量的基本類型:第一類型為靜態 生產力比率(productivity ratio),即在某一時間之產出的衡量/投入的衡量; 第二類型為動態生產力指標(productivity index),為在某一時期之靜態生產 力比率(現期)/相同比率在先前某一時間(基期) ,指標係指從這個時期至下一 個期間生產力的變化。 杜順榮(1994)認為企業在整個生產系統的演進過程中,會因各種內外因素 的改變而面臨不同的問題,因此在每一階段所選定之生產力改善方案也將有所不. 政 治 大 化、自動化及系統整合等特性,對其進行分類,整理歸納各種評估準則以作為評 立 同。所以,便朝二個方向進行研究,收集各種生產力改善技術並依標準化、合理. ‧ 國. 學. 估生產系統之依據,並依此發展系統評估模式。故希望藉此二者之配合,能透過 生產力改善技術及生產系統評估之結果,來幫助企業找出現階段最適當之生產力. ‧. 改善方法,以達到提升生產力之目的。. 邱江明(1984)認為,在進行企業生產力分析時,生產力係表示產出與投入. y. Nat. sit. 的比例,因此衡量出來的生產力比例數字所代表的意義並不大,唯有將生產力數. al. n. 力的方式:. er. io. 字與其他生產力數字相比較才能發揮生產力衡量的功能。據此提出三種評估生產. Ch. engchi. (一)與過去各期數字的比較。. i n U. v. (二)與預定標準數字的比較。 (三)與同業數字的比較。. 余朝權的研究指出,提高製造部門生產力的要訣,在於使製造或生產作業達 到合理化;而藉由一些生產不合理的徵候,找出問題根源,再以系統的方式加以 解決,便能使得生產力獲得改善。而其列舉出生產不合理時,常顯示出的徵候如 下: 1.. 產品供不應求,經常延期交貨。. 2.. 部份產品供不應求,而部份產品存貨堆積如山。. 3.. 次級品、報廢品多。 23.
(28) 4.. 在製品遍佈,原材料庫存滿溢。. 5.. 作業線上時常停工待料,或時常轉換製程、產品。. 6.. 機器設備經常損壞,或是開工時數不高,經常停機。. 7.. 有些工作站非常忙碌,有些工髼站則過份悠閒。. 8.. 有些員工工作負荷量太大,有些則相反。. 9.. 沒有操作時,機器、燈光仍繼續運轉或開亮。. 10. 加班天數或時數太多。. 以上這些生產不合理的現象最終都會影響生產力,因此應透過生產作業之整 理規劃,對於各項資源做最佳配置,並且公司每一個生產部門的人員,皆能夠具. 政 治 大 廠資源的生產力達到理想的地步。 立. 有生產力意識,對於自身所掌握的資源,不讓其閒置、浪費,如此最後必可使整. ‧. ‧ 國. 學. n. er. io. sit. y. Nat. al. Ch. engchi. 24. i n U. v.
(29) 第參章 研究方法 本章的主要目的在於配合個案公司之「生產力提升」改善專案,歸納出一套 具體可行之六標準差改善流程,藉由描繪六標準差改善流程之界定、衡量、分析、 改善、控制等五個階段之不同的管理活動,以確立個案公司之改善流程,並為專 案的執行提供一個明確的依據。. 第一節 界定階段 六標準差改善流程的第一個階段為界定(Define),其主要的用意在於釐清. 政 治 大 段所獲致的結果以書面化的方式呈現。界定階段之步驟流程如圖 3-1,以下分別 立 描述各項步驟之作業內容。. 專案所面臨的問題,定義改善範圍,並訂定明確的改善時程,最後,並將界定階. ‧ 國. 學. Nat. 定義專案範疇與目標. n. al. er. io. sit. y. ‧. 建立專案團隊. i n C確認關鍵影響因素 hengchi U 訂定專案時程. 確立專案小組章程 圖 3-1. 定義階段步驟流程圖. 25. v.
(30) 一、建立專案團隊 建立專案團隊有助於組織在改善初期,掌握現有問題的狀況與影響幅度,同 時透過專案團隊之溝通協調,將專案內涵具體地傳達至所有利害關係人,並藉此 凝聚組織內部共識。專案團隊的形成須透過組織挑選適當的人才組成,並賦予明 確的改善標的與充足的資源與承諾,使專案團隊能夠在最短的時間內定義問題的 現況。 二、定義專案範疇與目標 專案團隊成立後的第一個任務為定義專案範疇與目標,使有限的資源能夠有 效地集中於關鍵問題的改善上,並設定具體可行的專案目標,作為專案團隊努力 的方向。. 政 治 大 案的目的與影響幅度,並就專案可能達成的結果,制定明確的改善目標。 。SIPOC 立. 在進行專案範疇的定義過程中,專案團隊與高階主管須充分的互動,探討專. ‧ 國. 學. 圖(SIPOC Chart)為六標準差改善流程的界定階段中,最普遍也最實用的一項 圖表工具,其代表:. 其可為內部或外部之人員、流程或公司。. Nat. y. ‧. (一) 供應者(Supplier) :提供給流程所需的物料、資訊等之人員、流程或公司,. sit. (二) 投入(Input) :流程所需之物料、人員、機器或資訊。. er. io. (三) 流程(Process) :將投入轉換為產出的一連串步驟,其步驟可分為加值或非. al. n. v i n Ch (四) 產出(Output) :交予顧客之產品或服務,為投入經由流程轉換的最終結果。 engchi U 加值步驟。. (五) 顧客(Customer) :產出的接受者,可能是下一個流程或是最終使用者。. 當專案團隊確立改善標的,並規範出專案的範疇後,建立務實且具挑戰性的 目標將有助於導引出專案團隊的士氣,並為整個專案制定比較的基礎。在此步驟 中,須注意目標的訂定必須能夠反映顧客最關注的焦點,亦即目標的提升將使得 顧客的滿意度明顯提升,同時組織也能因此獲致最大效益。 三、確認關鍵影響因素 六標準差的核心手法在於運用一個重要的公式 ,即關鍵影響因素公式 Y=f(X),Y 為所欲改善的標的,X 則為關鍵影響因素,藉由調整關鍵影響因素, 將現況導引到所欲達成的結果。專案團隊可透過歷史資料分析、基本數據蒐集、 成員的觀察與腦力激盪,深入問題的核心,找出關鍵影響因素。若能有效運用關 26.
(31) 鍵影響因素公式,找出影響結果之最關鍵因素,專案成效將大為提升,而後續的 衡量、分析、改善、控制等階段所進行之工作,也才得以朝正確的方向進行。 四、訂定專案時程 專案團隊在此步驟中將為專案制定出明確的工作項目,並預估工作完成所須 的時間,以排定專案進度,最後繪製成專案時程圖,以協助專案團隊掌握工作進 度,使專案在既定的時間框架下達成。 五、確立專案團隊章程 專案團隊章程載明專案攸關之重要事項,亦即將專案初期所獲致的資訊與結 論進行彙整,為組織內部的專案認知與專案團隊所達成的共識,建立一份書面化 的聲明文件。基本上,專案團隊章程包括以下七個項目: (一) 專案名稱. 立. (二) 專案執行期間. 政 治 大. ‧ 國. 學. (三) 專案團隊組成 (四) 流程關係人. ‧. (五) 專案重要性 (六) 專案可行性. sit. n. al. er. io 第二節 衡量階段. y. Nat. (七) 專案目標. Ch. engchi. i n U. v. 六標準差改善流程的第二個階段為衡量(Measure) ,其主要目的在於量化問 題的現況,導引出問題的根本原因,並作為分析階段之研究基礎。因此,衡量標 的與資料的正確性為衡量階段之關鍵議題。另外,在衡量階段所蒐集的數據可作 為改善後專案成效之比較基礎,突顯專案之具體實績。圖 3-2 為本研究歸納之步 驟流程,藉此方式將可有效管控資料之正確性,以下分別描述各項步驟之作業內 容:. 27.
(32) 選擇衡量標的. 決定數據類型與抽樣方法. 蒐集數據. 分析衡量系統 圖 3-2. 立. 一、選擇衡量標的. 衡量階段步驟流程圖. 政 治 大. ‧ 國. 學. 選擇衡量標的之意義在於決定適當的指標反應問題的真實情況,不當的衡量 標的不僅無法突顯問題的全貌,也將誤導專案朝向錯誤的方向進行,造成資源人. ‧. 力的無效浪費。因此,改善小組在選擇衡量標的時,須確認其涵蓋於專案範疇內, 並且能夠精準地反映關鍵問題。. y. Nat. sit. 二、決定數據類型與抽樣方法. n. al. er. io. 數據主要分為連續型與離散型兩種,不同的衡量要素決定了數據的類型。所. i n U. v. 謂連續型數據是指具備「無限可除計數」特性的衡量要素,如分貝、溫度、時間. Ch. engchi. 等;而連續型數據以外者,則是離散型數據,其包括滿意度、產品類型、教育水 準等。由於連續型數據能夠進行深入的分析,因而能夠協助研究者察覺細微的資 訊。 抽樣方法主要分為簡單隨機抽樣、分層隨機抽樣、系統抽樣與集體抽樣四種 方法。由於簡單隨機抽樣之便利性,同時具備母體代表性,因而在實務上較為常 用。 三、蒐集數據 此步驟的工作乃針對衡量標的之特性,決定適當的數據類型,並依照抽樣方 法的原則,運用量測工具進行數據的蒐集,以作為分析階段之研究基礎。 四、分析衡量系統. 28.
(33) 在六標準差衡量系統之分析中,最常用者為重複與再生分析(Gauge R&R), 其目的在於確保衡量系統具有統計上之穩定性。此分析手法能夠衡量研究者之量 測方式,進而確認衡量系統的每個構面是否正常運作,並決定研究者的投入是否 具備分析價值。 重複與再生分析之步驟包括測量實際的衡量標準、令不同之團隊成員根據不 同的試作隨機樣本進行測試,以及評估統計資料的穩定性。該分析手法能夠讓研 究者判斷資料是否具有正確性、重複性、再生性與穩定性。若欲獲致改善效益, 確認資料具備上述特性是必要的,否則不適當的資料將導致無意義的後續分析。 進行重複與再生分析可運用以下之公式,獲得指標數據,並判斷出衡量系統 是否具備正確性、重複性、再生性與穩定性:. 政 治 大 透過上述公式所獲得之數據,將落在三個數字區間內,不同的區間反映出量測值 立 %GRR=量測標準差×6/產品規格公差(USL-LSL). ‧ 國. 學. 的可靠度,其區間包括: 1. %GRR<10%:量測值十分可靠. ‧. 2. %GRR<25%:量測值可以採信 3. %GRR>25%:量測值不宜採用. sit. y. Nat. n. al. er. io. 第三節 分析階段. i n U. v. 分析階段的主要目的在於根據衡量階段所蒐集的資料,進行深入的研究分. Ch. engchi. 析,釐清個別問題的真正原因,並透過假設檢定的過程,針對造成問題的因素發 展解決方案,並驗証之。分析階段之步驟流程如圖 3-3,以下分別描述各項步驟 之作業內容。 掌握問題現況. 進行問題分析. 確認問題成因與解決方案 圖 3-3. 分析階段步驟流程圖 29.
(34) 一、掌握問題現況 根據衡量階段所量測到的數據,進行數據分析,導引出初步結論,以反應改 善前的真實情況。 二、進行問題分析 分析問題的結果將找出問題的真正肇因,但此步驟是衡量階段耗時最長、過 程最複雜的步驟,但卻是專案與否成功的轉捩點,因此,若能善用適當的分析工 具,將有助於釐清問題的肇因。常用的分析工具包括傳統的人機圖、包括柏拉圖、 盒型圖、推移圖等等。 三、確認問題成因與解決方案 找出問題的肇因之後,便要針對肇因,提出解決方案。進行此步驟時,改善. 政 治 大 由提出構想而不被批評的機會,即便是天馬行空的想法,改善小組的每位成員也 立. 小組可善加利用腦力激盪的技巧,讓參與改善的每個成員能夠暢所欲言,擁有自. ‧ 國. 學. 必須保持開放的心胸,不放棄任何可能達成改善目標的提案。 在解決方案建立並執行後,改善小組須針對方案的有效性進行驗証,其方式. ‧. 乃根據試行結果,再次蒐集數據,並從中瞭解問題是否獲得有效改善。若確認解 決方案之有效性後,便可將此方案列入改善階段的整合性改善方案內容當中。. sit. y. Nat. n. al. er. io. 第四節 改善階段. i n U. v. 在分析階段中,改善小組透過數據的蒐集與統計工具的運用,研判出問題的. Ch. engchi. 真正肇因,並透過腦力激盪,提出創意的解決方案,同時驗証其有效性。進入改 善階段後,改善小組所須進行的工作,乃將改善階段已驗証其有效性之解決方案 結合為一套整合性解決方案,並執行之。改善階段之步驟流程如圖 3-4,以下分 別描述各項步驟之作業內容。. 提出整合性改善方案. 導入整合性改善方案 圖 3-4. 改善階段步驟流程圖 30.
(35) 一、提出整合性改善方案 此步驟須針對分析階段所發展出之個別解決方案進行再次評估,評估的方式 乃將個別解決方案交由公司內部的專業工程師進行研究。專業工程師在評估專案 時,須考量的原則包括以下幾點: 1.. 方案是否能夠消弭問題的真正原因、降低流程或產品的變異程度、避免問題 的重覆發生、符合原先預定達成的目標。. 2.. 方案的改善效率、風險評估、成本效益,以及最終是否滿足顧客的期望。. 3.. 方案是否耗用過多的資源、執行期間是否過長、對組織其他運作是否造成負 面影響。 當解決方案經過評估,確認其可行性後,便可考量個別方案之間的影響關. 政 治 大. 係,排列出方案的執行順序,據此結合為一個整合性的改善方案。. 立. 二、導入整合性改善方案. ‧ 國. 學. 當個別方案經由專業工程師評估其確實可行,並結合為一個整合性改善方案 後,接下來,便由改善小組將該整合性方案依照規劃的導入順序,依序執行。. ‧. 方案執行的步驟中,改善小組的主要任務為訓練、文件化、除錯、績效管理、 衡量。訓練是將改善方案的細部作法教授給所有相關使用者,並向該專案所涉及. y. Nat. sit. 到的利害關係人,進行詳細說明,爭取其支持與配合,避免溝通不足造成觀念上. er. io. 的衝突;文件化是針對改善方案執行過程所產生的結果資訊進行記錄的工作,並. al. n. v i n Ch 決方案,並克服改善過程中衍生的相關問題;績效管理是指改善專案須搭配適當 engchi U. 作為未來持續改善的基礎或進行其他類似改善專案的參考;除錯是指持續監控解. 的人力資源政策,建立新的獎勵制度,以激勵相關人員績極配合與投入;衡量則. 是撰寫改善專案的成果報告,記錄解決方案的改善成效,並建檔管理。. 第五節 控制階段 在確認解決方案有效且正面地影響關鍵影響因素後,改善小組應持續監控改 善結果,防範不良結果再度發生,並且維持改善結果的穩定性與一致性。唯有落 實執行控制階段的每個步驟,將改善成效控制在合理的水準,才算是成功的改善 專案。控制階段之步驟流程如圖 3-5,以下分別描述各項步驟之作業內容。. 31.
(36) 發展管制計畫. 建立六標準差改善模式 圖 3-5. 控制階段步驟流程圖. 一、發展管制計畫 在這個步驟中,必須運用特定的計量指標與衡量工具持續記錄與觀察流程, 以評估改善成效是否繼續維持。一般而後,管制計畫的內容包括:. 治 政 大 將專案執行的整個過程,包括專案目的與目標、執行細節、改善方法等,進 立 行詳細說明,作為專案執行的成果報告,並提供未來其他改善計畫執行之參 改善記錄. 2.. 流程圖. 學. 考依據。. ‧. ‧ 國. 1.. 包含改善前後之流程圖及差異說明,其目的在於利用圖示解說,使閱讀者得. io. y. sit. 操作說明. er. 3.. Nat. 以立即瞭解改善前後的流程差異。. 對於細部操作的改善須有一套完整的描述,以作為人員調整之參考依據,此. n. al. Ch. i n U. v. 文件可利用作業流程圖、圖像等輔助工具,使閱讀者輕易瞭解作業上的調整。 4.. 獎懲制度. engchi. 上述的文件乃針對作業的調整改善進行說明,但人員的配合則有賴獎懲制 度。公平的獎懲制度有助於提高人員的配合度與士氣,並維持作業紀律。. 二、建立六標準差改善模式 根據專案執行的經驗,將六標準差改善流程中的每個階段,摘錄出重要準 則,協助組織成員進一步掌握六標準差之睛髓,並促成六標準差知識的推廣與應 用。. 32.
(37) 第肆章 個案研究 第一節 全球手機市場發展現況 一、全球手機需求概況 由於資訊科技的進步,以及對於通訊服務的需求,全球手機產業在近幾年來 發展迅速。根據 Gartner 的研究報告指出,2004 年全球手機銷售量高達 6 億 7,400 萬支,相較於 2003 年,大幅成長 30%之多,成長的原因來自於新興市場需求帶 動與歐美市場的換機需求。針對 2005 年之全球手機需求情況,各家看法不一。 Gartner 樂觀預估,2005 年手機市場可望繼續成長,銷售量上看 7 億 3,000 萬支,. 政 治 大 求的結果。相較之下,大陸佐思的研究結果卻認為,2005 年全球手機需求僅有 6 立 億 6,500 萬支,需求減緩的理由在於市場缺乏強而有力的新應用與新技術,且換. 其原因來自於行動用戶汰換機種需求依舊維持成長的趨勢,以及新興市場帶動需. ‧ 國. 學. 機需求減弱,再加上新增用戶的增長率走低。儘管各家意見不一,但手機產品在 歐美市場已趨近飽和狀態則是不爭的事實,可預見的是,手機需求成長較高之區. ‧. 域將漸漸轉向新興市場,且產品主力以低階手機為主。資策會市場情報中心(MIC). sit. y. Nat. 便指出,未來的新機用戶市場可望延續至拉丁美洲、東歐及非洲等第三世界國. io. er. 家;而歐美系統服務業者以搭售彩色/照相手機產品方式將持續推動換機需求, 預估 2005 年全球市場規模可達 6.6 億,成長幅度則趨緩至 6.8%。. al. n. v i n 2005 年正值手機世代交替之際,隨著全球手機大廠規劃陸續推出 3G 手機, Ch engchi U 且各國 3G 系統業者亦配合手機大廠時程開始營運,再加上 3G 手機之整合性功能 特點,諸多預測機構預期 2005 年下半,3G 手機將逐漸取代現有手機,成為市場 主流。IDC 預測未來幾年,多媒體功能強大的 3G 手機將引領整體市場成長,預 估 2006 年,3G 手機將佔整體手機市場的 18%;2007 年則可達到 25%。目前,全 球每七人中就有 1 人正使用 GSM 服務,佔數位無線市場的 72%,未來隨著 3G 時 代的來臨,預計多數電信系統業者仍將採用 GSM 所延伸的系統,如我國在 2002 年所核發的五張 3G 執照中,就有四張是採用泛歐規的 WCDMA 標準,僅一張採美 規的 CDMA2000 標準。 消費性電子產品的生命週期短暫,使得產品汰舊換新的速度居所有產品之 冠,消費者往往尚未熟悉一項新產品時,另一世代產品又即將出現。儘管如此, 33.
(38) 此特性對於消費者而言,仍是利多於弊。由於汰換速度過快,手機業者為求回收 成本,因而採取短期降價策略,以吸引消費者的購買。而另一個好處是,新穎而 完整的功能不斷推出,使消費者能夠同時享受到通訊便利性與消費性電子的娛樂 性,將手機功能整合到人的生活中。預計未來手機的發展方向包括:提供更快的 處理速度、更大的儲存容量、更清晰的音質,以及更好的視覺享受。 二、全球手機廠商競爭概況 手機市場向來呈寡佔型態 前五大廠幾乎涵蓋逾七成的市場佔有率。目前全 球手機市場,Nokia、Motorola、Samsung 已形成三足鼎立的局勢。2004 年,Nokia 最終以 30.7%之全球手機市場佔有率獨佔鰲頭,而以設計領先的手機製造商 Motorola 則以 15.4%的市佔率排名第二,第三名 Samsung 亦緊追在後,市場佔有. 政 治 大 6.3%。表 4-1 為 2004 年全球手機銷售數量統計表。 立 表 4-1. 30.7. 104,124,2. 15.4. y. 85,238,4. 12.6. io. Siemens. 207,231,3. sit. Samsung. 2004 年市場佔有率(%). Nat. Motorola. 2004 年銷售量(千台). er. Nokia. 2004 年全球手機銷售數量統計表. ‧. 公司名稱. 學. ‧ 國. 率為 12.6%。Siemens 及 LG 分居第四及第五名,市場佔有率分別為 7.2%以及. 48,455,8. 7.2. 42,031,7. i n U. 其他. 144,643,7. 21.6. 總計. 674,001,9. 100.0. LG. n. SONY Ericsson. al 42,276,8 Ch. 6.3. engchi. v. 6.2. 資料來源:Gartner Group,2005/03. Nokia 的產品功能向來以貼近生活、掌握流程趨勢聞名,從 2005 年初,該 公司所推出的 40 款手機看來,三分之二比例為照相手機,同時半數以上也配備 MP3 功能,可說是全力迎合市場流行;相較之下,Motorola 的產品特性在於獨性 的設計,從該公司新近推出的產品外觀來看,其試圖加大設計領先地位的野心不 容小覷;Samsung 在推出新款手機的速度上,向來較競爭對手來得緩慢,因而往 往未能搶得先機而失掉市場,且其手機功能對消費者的吸引力小,導致競爭失利。. 34.
數據

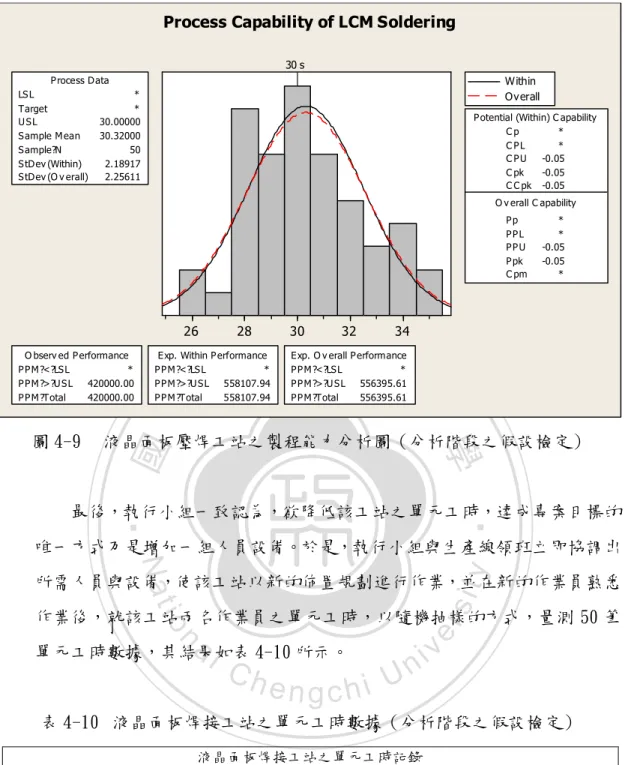

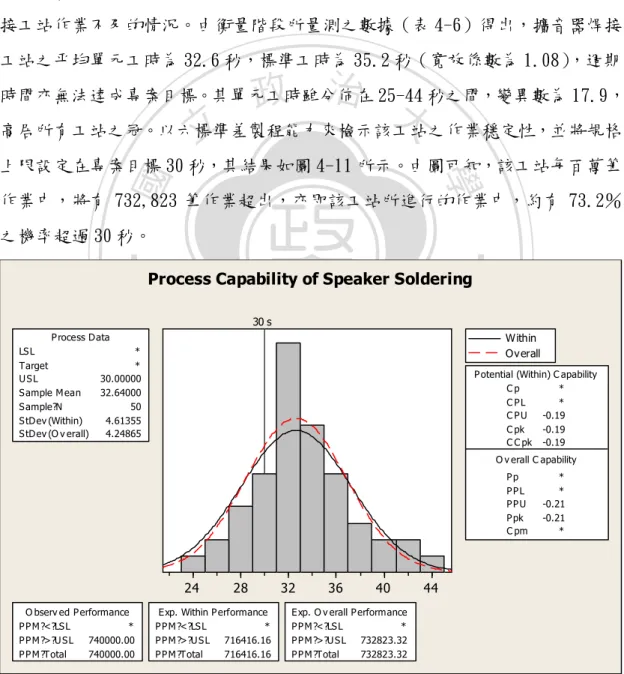
+6
相關文件
為降低時程及成本以及增加巴西產品海外競爭力,巴西貿工部於 2017 年 3
(五) 永續成長:研發創新與環境(R&D + i)。此領域相關政府 部門資源整合及參與,以提高 R&D + i
(二) 另依產證管理辦法第 5 條第 2 項規定,附加價值率之計
為配合政府推動六大新興產業及十大重點服務業之發展與開拓就業
為協助廠商因應全球區域經濟整合及自由貿易協定 之衝擊,提升產品出口競爭力,經濟部已協調財政 部針對進口關稅 4.3 %以上之產品,恢復外銷品出
為配合政府推動六大新興產業及十大重點服務業之發展與開拓就業
利潤指數 (PI) = 投資現值 (PV) / 投資成本 (IC)。..
1970 年代末期至 1995 年:許多農業生技公司開始投入研發以迄 1995 年第 一個產品上市。Monsanto 為此時期最早的投資者,且為第一個將農業生技產 品上市的公司,其他如 Syngenta 與